Slabs for Colder Climates, Part 1: The How and Why of Frost-Protected Shallow Foundations
As energy savings and the conservation of resources increasingly drive decision-making for homebuilders, frost-protected shallow footings offer a good method for constructing slab-on-grade foundations.
As a builder constructing townhouses, commercial buildings, and the occasional slab-on-grade (SOG) house in frigid Nebraska, I always thought it silly to dig footings half as deep as a full basement when the point of SOG construction was to spend less on foundations. A basement seemed the better value, to me, given that only token cost savings came with a slab ... until one year, while attending the National Association of Home Builders (NAHB) International Builders' Show, I heard a lecture on a new (at least for me) approach to constructing slabs in northern climates that did not require footings to extend below the frost line. I immediately perked up and listened closely; it sounded like a good cost-saving measure.
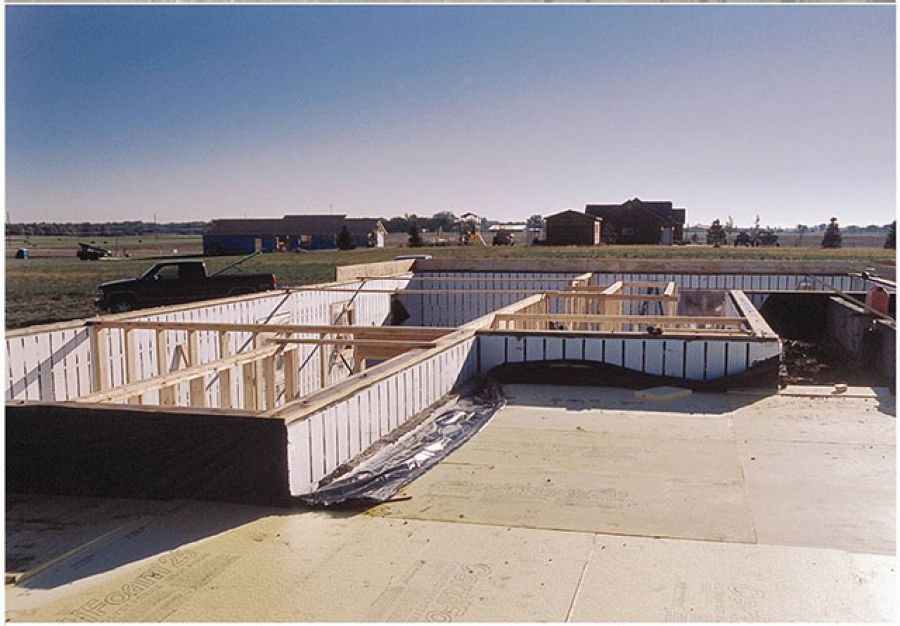
I listened, did a little research, and learned the method. Then (after wrestling with the building department a few rounds), I tried it. Since then, I have built at least 100 structures successfully using frost-protected shallow foundations (FPSF) and saved more than money. Now that environmental stewardship and reduced energy consumption have become the most significant focus of better buildings, FPSFs have become the norm for contractors using resource-sparing methods to build highly insulated structures.
Let’s start with the money savings, however. A slab may still be the most affordable foundation, but if you use conventional techniques, the difference in cost between full basements and slabs will be marginal: you dig below the frost line, 36" or more, and then pour a foundation before forming the slab. Many builders, including myself, reasoned that more value for the dollar could be gained by just digging a few feet more and building a full basement. This was true until codes began to accept FPSFs in 2000. The method has been used in the colder regions of Europe and Canada for more than 50 years, and in parts of the United States for more than 25. In fact, architect Frank Lloyd Wright designed and built a type of FPSF intended to achieve affordability in his Usonian Homes.
The principle is simple, yet it took me a little while to understand how a little bit of insulation can raise the frost depth under a building from 40" to just 12". An easy analogy is the down comforter. Without it, on a frigid winter night your body loses its internal heat and you get cold quickly. Pull the cover snugly under your chin and the comforter preserves your body heat until you feel toasty warm. A FPSF works in exactly the same way as a comforter, except it uses rigid foam insulation as a "quilt" and uses the heat emanating from the earth, along with heat captured from the interior temperature of a heated building, as sources of warmth.
Fros- Protected Shallow Foundations are generally installed on concrete slab foundations, but they can also be used for other types of foundation systems including crawl space foundations (as shown), and wood foundation systems.
By adding insulation around the exterior perimeter of the foundation wall and in some climates extending beyond the perimeter horizontally at the base of the foundation wall, FPSF technology captures the geothermal and conditioned building heat to effectively reduce the depth that frost can penetrate around the perimeter of a structure. Even in the coldest climates, a typical FPSF only requires installation of 1" to 2.5" of extruded polystyrene insulation on the face of the footing and foundation wall and, in the coldest areas outward, 12" to 36" horizontally at footing depth.
Employees from Bill Eich Construction install ridged foam insulation for a garage slab. Over the last 25 years, Eich has installed hundreds of FPSFs without a single failure or foundation-related call back. Eich says that he saves $1,500 to $4,000 on every home he builds or remodels by using this technology.
The system can also be used to build unheated structures. Design methods exist to capture and concentrate ground temperatures sufficiently to use FPSFs in outbuildings and, in perhaps the most practical application of this technology, to eliminate the need for frost depth (frost-free) footing around an attached garage.
The subtleties of the FPSF require careful study. It’s important to select the right insulation, because only a few products can maintain an effective R-value throughout the expected lifespan of a building, and the design of FPSFs is dictated by climate zone. Prescriptive design requirements are provided in International Residential Code 403.03, and guidelines available from the NAHB Research Center’s Revised Builder's Guide to Frost-Protected Shallow Foundations are useful resources. Once you learn the method appropriate to your region, it’s as easy as any other foundation to deploy again and again.
In addition to substantial construction cost savings and reduced excavation and concrete use, Frost-Protected Shallow Foundations also provide significant energy savings as the insulation required typically exceeds existing code requirements.
The next post, “Slabs for Colder Climates, Part 2: Installing Frost-Protected Shallow Foundations, will discuss design criteria for and installation issues with FPSFs.
The American Society of Civil Engineers (ASCE) developed Standard 32-01 for the Design and Construction of Frost-Protected Shallow Foundations. Order it by calling the NAHB Research Center at 800-638-8556 or the ASCE at 800-548-2723. Learn more at ASCE 32-01. In March 2000, the NAHB released Energy-Efficient Resource-Efficient Frost-Protected Shallow Foundations (FPSFs) for those interested in learning more about FPSFs.
- RevisedFPSFGuide_Sept2004.pdf (4883 Downloads)
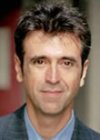
Fernando Pages Ruiz
Homebuilder, developer and author Fernando Pagés Ruiz builds in the Midwest and Mountain States and consults internationally on how to build high-quality, affordable and energy-efficient homes. As a builder, his projects have numerous awards including the 2008 “Green Building Single Family House of the Year” and the 2007 “Workforce Housing Award” from the National Association of Home Builders. In 2006, the Department of Housing and Urban Development's PATH project chose him to build America's first PATH Concept Home, a home that is affordable to purchase and to maintain while meeting the criteria of LEED for Homes, ENERGY STAR, MASCO Environments for Living, and the NAHB's Green Building standards. A frequent contributor to Fine Homebuilding and EcoHome magazines, Pagés is also the author of two books published by the Taunton Press: Building an Affordable House: A high-value, low-cost approach to building (2005) and Affordable Remodel: How to get custom results on any budget (2007).
Contact Fernando on facebook or by way of his website buildingaffordable.com.