Glazing
Most glass used in glazing today begins as float glass, so called because it is produced by floating molten glass onto molten tin. This primary glass may be clear or tinted and is produced in several standard thicknesses. The typical process for producing glass involves reheating and then slowly cooling the glass to reduce internal stresses. The result of that process is annealed glass. Annealed glass may be heated a second time followed by rapid cooling to produce heat treated (strengthened) or fully tempered glass.
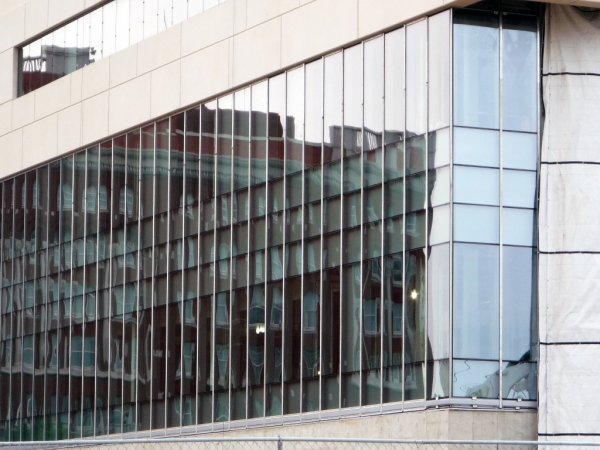
Clear float glass typically refers to products that are nearly colorless and have visible light-transmittance values ranging from 75% to 92%, depending on the thickness.
Tinted float glass is made with colorants that not only affect its appearance and reduce visible light transmittance but also reduce solar transmittance (and, therefore, solar heat gain) by absorbing solar energy.
Monolithic glass is a term used to describe a single sheet of glass used for glazing. Insulating glass is comprised of two sheets of glass, either with a sealed edge or a spacer edge separating them. Spacer edges are typically formed of metal and contain a desiccating material, and join the glass by using sealants.
High performance glass units often incorporate coated glass. Very thin metal coatings are deposited on one face of the glass to limit certain parts of the light spectrum and enhance the energy performance of the glass. Low-e glass uses a coating that selectively reflects long-wavelength infrared radiation to keep out heat in the summer and reflect heat back in during the winter, without producing mirror-like visible light reflectance.
Laminated glass combines two or more sheets of flat glass with plastic interlayers. Because laminated glass tends to stay intact when broken and is usually retained within the opening, it is ideal for use in skylights and security glazing applications.
Fully-tempered glass breaks into small cubes and is often used for safety glazing. Laminated glass may also meet the requirements for safety glazing. Safety glass is required for entrance and exit doors, storm doors, sliding patio doors, glazed panels, and doors and enclosures for bathtubs and showers.
Patterned glass is produced using patterned rollers to impart texture onto molten glass.
Wired glass is produced by rolling glass with stainless-steel wires within the glass and then polishing its surfaces. Because glass shards are retained in an opening after it is broken, wired glass may pose a severe risk to someone accidentally breaking through it, and permissible uses are strictly limited by code.
ASTM C 1036 and ASTM C 1048 are the standards for specifying the qualities for individual annealed and heat-strengthened glass plies respectively. ASTM C 1376 is the standard for reflective-coated glass. ASTM C 1172 is the standard for laminated-glass products for building glazing. It covers units consisting of two or more plies of flat glass bonded together with an interlayer. ASTM E 2190 is the standard for insulating-glass units.
ASTM E 1300 is referenced in the 2006 International Building Code (IBC) for determining glass thicknesses and glass types required to resist design wind loads and, for sloped glazing, design snow loads. The 2003 IBC contains its own requirements for determining glass thicknesses and glass types, which are different from those in ASTM E 1300.
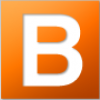
Buildipedia Staff
The Buildipedia research and writing staff consists of dozens of experienced professionals from many sectors of the industry, including architects, designers, contractors, and engineers.
Website: buildipedia.com/