Mitigating Elevator Noise in Multifamily Residential Buildings
Today’s modern mid rise and high rise luxury condominiums and apartment buildings offer numerous amenities to attract potential owners. They can offer spectacular vistas through floor to ceiling walls of glass, high end finishes on the floor, gourmet style kitchens with all the modern features one could ever want, and a master bedroom suite that offers a tranquil and quiet place to escape. In these building types, elevators become a necessary component for vertical circulation to access the floors. For those residences that are adjacent to the elevator equipment room or the elevator hoistway, the noise and vibration caused by the operation of the elevator can be a potential source of sound intrusion. Because today’s buildings are constructed with lightweight materials, and because there is a need to generate maximum useable square footage, sound transmission issues are compounded. All this combined can result in unsatisfactory living conditions for tens of thousands who live in condominiums or apartments.
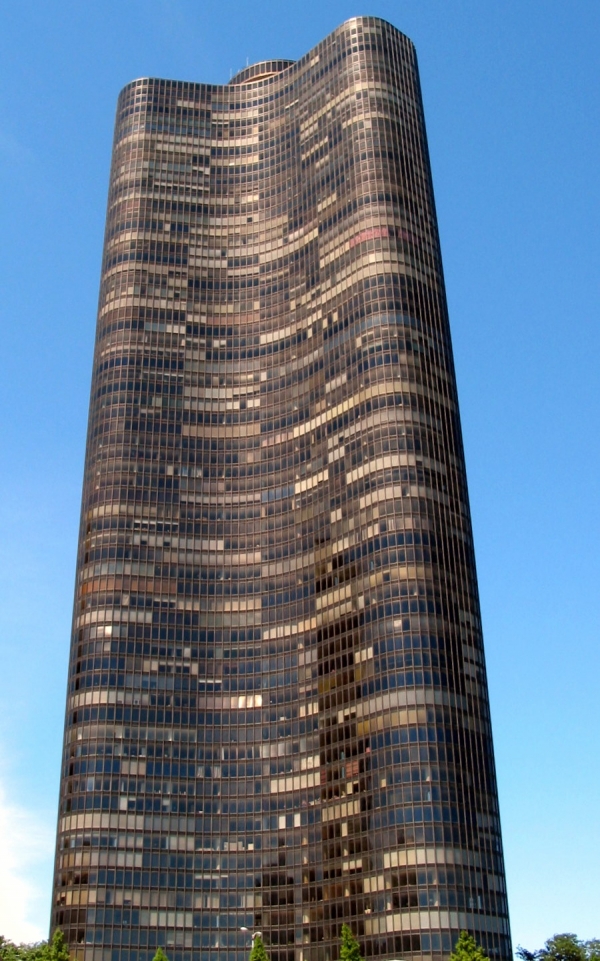
The acoustical environment of each residential unit must be taken seriously by both the architect and the developer during the design and planning phase of a project . The operation of elevators will generate significant sound and vibration, which needs to be considered due to the potential impact on adjacent residences. To specifically address these issues related to elevator noise is a challenge. It can be very complicated to identify the source of noise, be it air-borne or structure-borne, after the construction is complete. Many of the impact noises result from structure-borne transmission issues that are not easily calculated or projected prior to the actual construction of each specific project. Additionally, it is difficult for elevator manufacturers to quantitatively produce sound level data for their systems, due to each individual project being uniquely different.
To lessen any future litigation and as part of providing due diligence, it is recommended that a consultant who specializes in architectural acoustics be a part of the design team. An experienced acoustical consultant can provide the architectural team with a number of design options early in the design phase, as well as help explore options to meet the necessary acoustical needs of the facility. Addressing sound isolation and acoustic privacy from mechanical system noise and vibration is a critical part of the final success of the project.
Sound Transmission Class
Sound is the vibrations transmitted through an elastic medium such as a solid, liquid or gas, with frequencies that range from 20 to 20,000 hertz. This is the frequency range which is typically capable of being detected by human ears. Since it requires an elastic medium, sound cannot travel through a vacuum. The more elastic a substance, the better it will conduct sound. An example of this would be comparing lead with steel. Lead is considered inelastic and thus will not conduct sound very well. Steel is considered elastic, making it an exceptional conductor of sound.
A standard by which the construction industry uses building materials for sound attenuation is known as the Sound Transmission Class (STC). The Sound Transmission Class is a number rating of a material or an assembly's ability to resist air-borne sound transfer at frequencies 125-4000 Hz. This range represents the speech frequencies. In general, a higher STC rating will block more noise from transmitting through a partition or assembly. However, STC ratings do not take into account low frequencies below 125 Hz. The ratings are based on laboratory testing and do not take into consideration weak links within the wall assembly such as joints, penetrations and gaps around the perimeter of the wall assembly.
The STC number is derived from sound attenuation values tested at sixteen standard frequencies from 125 Hz to 4000 Hz. These transmission-loss values are then plotted on a sound pressure level graph and the resulting curve is compared to a standard reference contour. Acoustical engineers interpolate these values to determine an STC rating.
Changes in STC with Resulting Changes in Apparent Loudness |
|
STC Rating Change | Apparent Loudness Change |
+/- 1 | Barely Imperceptible |
+/- 3 | Just Perceptible |
+/- 5 | Clearly Noticeable |
+/- 10 | Twice (or half) as Loud |
Typical Examples of Sound Levels |
|
Source of Sound | Decibel (dB) |
Calm Room | 20-30 |
Normal Human Speech | 40-60 |
Moving Car from 30'-0" Away |
60-80 |
Traffic Noise on a Major Road from 30'-0" Away |
80-90 |
Typical Jackhammer |
100 |
Jet Engine from 300'-0" Away |
110-140 |
Hearing Damage Begins with Short Exposure |
120 |
Human Threshold of Pain |
130 |
Another form of sound measure is impact or structure-borne noise known as Impact Insulation Class (IIC). This rates a floor/ceiling assembly’s resistance to the transmission of structure-borne or impact noise. Achieving a higher IIC rating, such as 70, does not always ensure that footfall noise will be totally eliminated. Of all noises, totally eliminating the impact noise of footfall is very difficult.
Sources of Elevator Noise
The air-borne sound and vibration from elevator systems can result from a variety of sources and transmission paths. Several of the more significant sound sources are:
- Tonal noise from traction elevator hoist machinery
- Tonal noise from switchgear for traction elevators
- Hydraulic elevator pumps and machinery
- Transient noise from poorly adjusted elevator car guide rollers or bumps in rails
- Elevator doors
- Door enunciators
Machine-Room-Less Elevators have a drive system that is supported by the rails. Therefore, the vibration generated at the time an elevator runs can easily be transmitted to the hoistway enclosure from the rails. For this reason, architects need to be cautious of generating structure-borne noise by the vibration from the hoistway to adjoining rooms.
Most of the sound energy will be transmitted by the separating wall assembly itself, but there are many opportunities for "flanking paths" or "sound leaks" to occur. Some of the common air-borne sound transmissions through flanking paths in buildings are:
- Plenums and suspended ceilings
- Ducts with no sound attenuation material
- Transoms and air grilles
- Unblocked ceiling plenum spaces
- Wall perimeters with no acoustical sealant
- Ducts, piping, electrical devices and fixtures
- Masonry joints
Sound travels not only in a straight path from its source but also bounces off partitions, bends around barriers, and squeezes through small openings, all of which can allow noise to reach surprisingly far beyond its point of origin.
Basic Principles for Controlling Sound
In general, loud speech can be understood fairly well through an STC 30 wall, but should not be audible through an STC 60 wall. An STC of 50 is a common building standard and blocks approximately 50 dB from transmitting through the partition. However, occupants would still be subject to some barely audible sounds of loud speech. Wall assemblies with a higher STC such as 60 would be as much as 10dB better. For particularly sensitive areas where sound transmission is a concern, this higher STC rating should be installed.
- A separate wall around the perimeter of the elevator hoist must extend to the structural deck in order to achieve optimal isolation. Walls extending only to a dropped ceiling will result in a flanking path for sound.
- Sound will travel through the weakest elements, such as doors, plumbing penetrations or electrical outlets.
- When the mass of a barrier is doubled (increasing the STC rating), an increase by approximately 5 dB will be gained. This increase will be clearly noticeable.
- Installing insulation within a wall or floor/ceiling cavity will improve the STC rating by about 4-6 dB, which is also noticeable.
- Metal studs perform better than wood studs. Staggering the studs or using dual studs can provide a substantial increase in isolation.
- Increasing air space in a wall assembly will also improve isolation.
Building codes such as The Uniform Building Code (UBC) and International Building Code (IBC) contain requirements for sound isolation between adjacent dwelling units or between dwelling units and adjacent public areas such as halls, corridors, stairs or service areas. These codes also apply to hotels, motels, apartments, condominiums, monasteries and convents.
- Code requirements for walls: STC rating of 50 (if tested in a laboratory) or 45 (if tested in the field).
- Code requirements for floor/ceiling assemblies: STC and IIC ratings of 50 (if tested in a laboratory) or 45 (if tested in the field).
An assembly rated at STC 50 will satisfy the building code requirement. However, as mentioned above, occupants could still be subject to awareness, if not understanding, of loud speech. Therefore, it is typically expected that luxury accommodations have a more rigorous design goal. When field testing is done, this evaluates the dwelling's actual construction assembly and includes all sound paths.
Typical STC Ratings for Masonry Walls
STC ratings for masonry and CMU walls are based on the weight of the block. Improved performance can be achieved by filling the cells with additional materials as shown in the chart below.
Estimated STC Ratings for CMU Walls
Wall Thickness, Inches |
Hollow Units | Grout Filled | Sand Filled | |||
Weight | STC | Weight | STC | Weight | STC | |
4 | 20 | 44 | 38 | 47 | 32 | 46 |
6 | 32 | 46 | 63 | 51 | 50 | 49 |
8 | 42 | 48 | 86 | 55 | 68 | 52 |
10 | 53 | 50 | 109 | 60 | 86 | 55 |
The STC rating of a CMU wall can be estimated based on its weight using the following formula:
STC = 0.18W + 40
Where W = pounds per square foot (psf)
There are many unique factors that can change the final STC calculations. The estimate could be off by as much as +/- 4 dB. There are numerous other issues that need to be addressed to get a more accurate calculation.
Improving STC Rating of Walls
While the science behind sound is well understood, using that science to create the desired acoustical quality within a building or room is complex. No single acoustical solution can be universally applied to all designs. Each environment features unique parameters that the architect and designer must consider when developing floor plans, selecting materials, and designing assemblies. Virtually every material from furniture and wall and floor coverings to computer equipment will affect sound to some degree. However, designing wall partitions, ceiling systems and floor/ceiling assemblies for the distinct qualities of a space will achieve the most effective sound control.
- Adding mass: When the mass of a barrier is doubled, the isolation quality (or STC rating) increases by approximately 5 dB, which is clearly noticeable.
- Air space: airspace of 1 ½" will improve the STC by approximately 3 dB. An air space of 3" will improve the STC by approximately 6 dB. An airspace of 6" will improve the STC by approximately 8 dB.
- Cavity insulation: installing insulation within a wall or floor/ceiling cavity will improve the STC rating by about 4-6 dB, which is clearly noticeable.
Sound Suppression Guidelines for Noise Reduction
- The surrounding walls, floor, and ceiling assembly should have a substantial STC rating. If noise sensitive areas are nearby, STC 50 or 55 at a minimum should be used as the design criteria for the surrounding structure. All cracks and gaps around the perimeter must be filled with the appropriate acoustical caulking.
- In situations where noise-sensitive areas are not an issue, two layers of drywall (four total) are still recommended, and the area around the perimeter should be sufficiently caulked. Double-layer drywall with staggered seams works best.
- Doors must have a good STC rating. A rated door and frame assembly are needed if a noise-sensitive area is nearby. Ideally an STC 55 door system would be best, to match the walls. Rated doors may have cam hinges that raise the door and then lower it when it closes to eliminate the gap at the base and a tight seal around the perimeter, along with sufficient mass to give the door a good STC rating. Doors with a lower rating, such as STC 40, may be adequate for a non-noise sensitive areas.
- If a standard door is used, good sealing hardware is needed to seal around the perimeter of the door.
- Penetrations through the equipment room walls must be kept to a minimum. When pipes and conduit pass through the walls, they must be sealed with mortar or the appropriate acoustical sealant to prevent noise leaks. A heavy, solid material must be used. Do not use fiberglass.
- If the walls are concrete block, do not paint them. Unpainted block has about 33% absorption, which is lost with a coat of paint. Fiberglass panels on the ceiling or walls covering 25% of the area are beneficial, but not mandatory.
- Vibration isolation of the elevator machinery normally will not be needed when the unit is attached to a concrete foundation. If used on elevated floor slabs, 2” deflection springs properly sized and installed are suggested.
- Conduit from the power unit to the hoistway should be “vibrationally” isolated from the wall and the perimeter of the pipe should be sealed with the appropriate acoustical sealant to prevent acoustical leaks or flanking paths for vibration noise.
Regardless of the building type, elevators will generate considerable amounts of noise and vibration. In acoustically sensitive spaces, such as residences around the machine room and hoistway, it is important that the design team review all guidelines and criteria carefully. With the input of the elevator manufacturer, the structural engineer and the architect, the sound and vibration from the operation of elevators can be successfully mitigated.
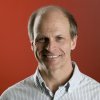
David Ingold
David Ingold is a graduate of The Ohio State University School of Architecture and a member of the Construction Specifications Institute (CSI) with Construction Documents Technology (CDT) certification. With more than 18 years of experience, David brings a broad knowledge base and understanding of design and construction to a wide variety of project types. He is an accomplished senior project administrator with experience in developing all phases of architectural documents. David has performed key responsibilities as a project leader, specifications writer, and coordinator for projects of all types and complexities including low- and high-rise condominiums, sporting facilities, higher education and government research laboratories, manufacturing facilities, wastewater treatment plants, parking garages, and campus master plans. David’s greatest aspiration is to provide construction administrative services to fully execute project designs.
Website: buildipedia.com/channels/on-site