Demolition Best Practices
Demolition projects can range from small, simple jobs to complicated undertakings that require sophisticated and detailed planning. Site conditions can vary significantly, and there is always a degree of imprecision to the wrecking of the building itself. For typical building demolition and site improvements the most common procedure is to use heavy mechanical equipment such as wrecking balls, excavation hoes, grapples, pulverizers, crushers, and hydraulic breakers and shears. Several factors need to be considered prior to and during demolition, including the scheduling of demolition activities, protecting the site (especially important with occupied structures), and dealing with hazardous materials.
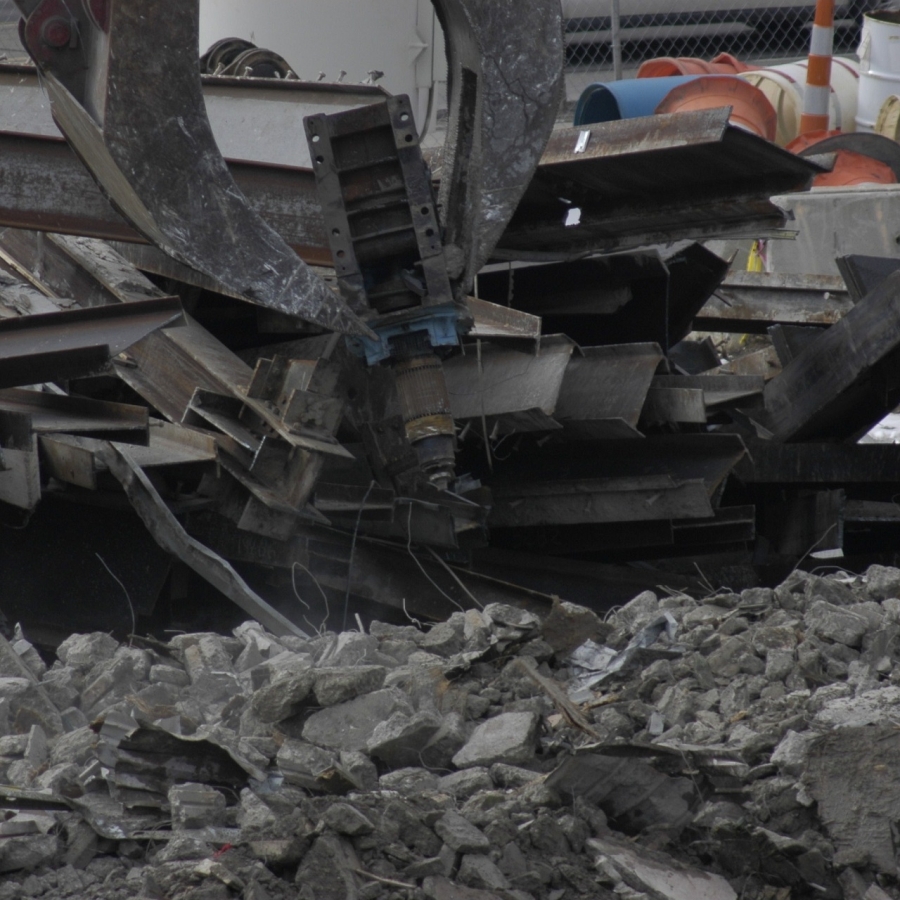
Codes and Standards
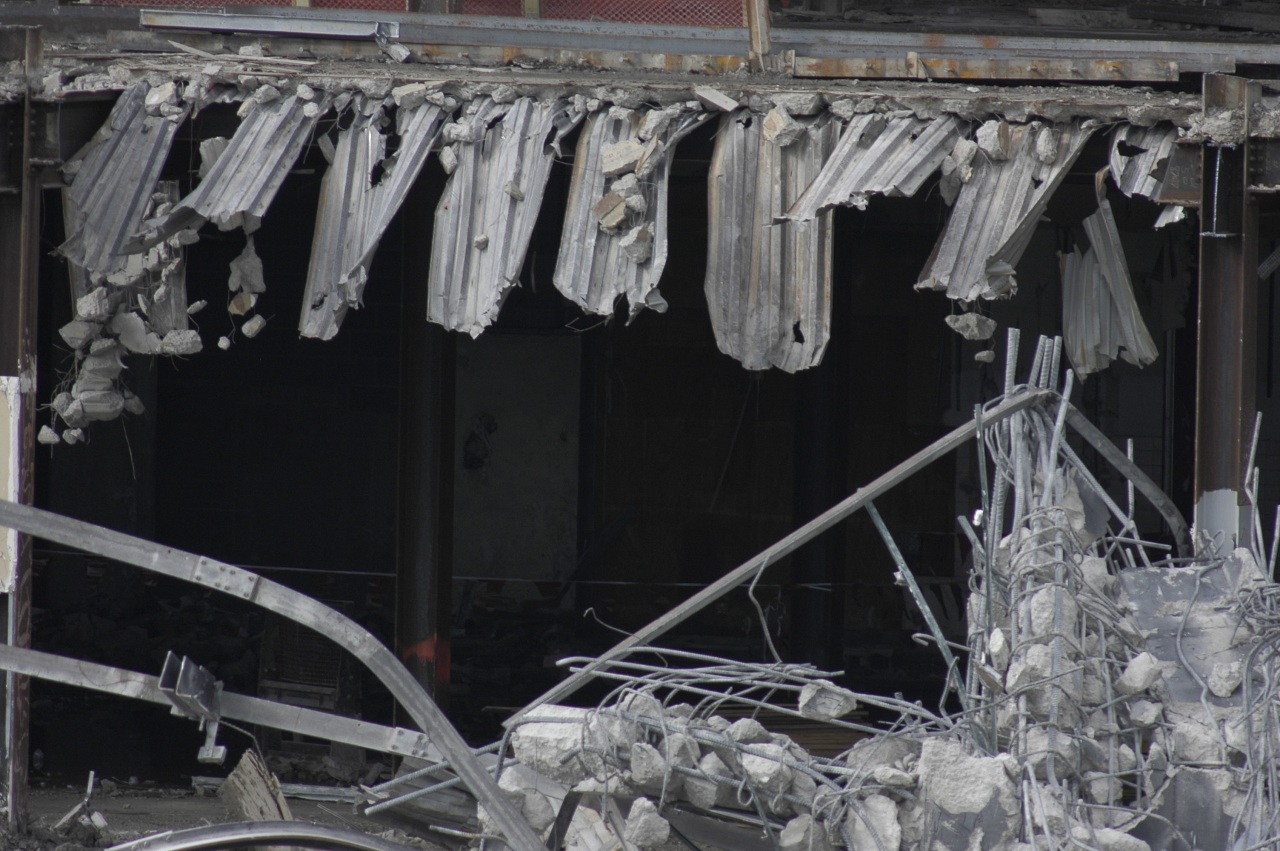
With the demolition of structures, the owner, architect, engineer and demolition contractor need to be aware of several CFR titles and other regulations.
29 CFR 1926.850(a)
Title 29 – Labor
Part 1926 – Safety and Health Regulations for Construction Subpart T – Demolition
Section 1926.850 – Preparatory Operations
"Prior to permitting employees to start demolition operations, an engineering survey shall be made, by a competent person, of the structure to determine the condition of the framing, floors, and walls, and possibility of unplanned collapse of any portion of the structure. Any adjacent structure where employees may be exposed shall also be similarly checked. The employer shall have in writing evidence that such a survey has been performed."
29 CFR 1926.1101(a)
Title 29 – Labor
Part 1926 – Safety and Health Regulations for Construction Subpart Z – Toxic and Hazardous Substances
Section 1926.1101 – Asbestos
"Demolition or salvage of structures where asbestos is present."
40 CFR 61 - Subpart M, Section 61.145
Title 40 – Protection of the Environment
Part 61 – National Emission Standards for Hazardous Air Pollutants
Subpart M – National Emission Standards for Asbestos
Section 61.145 – Standards for Demolition and Renovation
"The owner or operator of a demolition or renovation activity and prior to the commencement of the demolition or renovation, thoroughly inspect the affected facility or part of the facility where the demolition or renovation operation will occur for the presence of asbestos."
40 CFR 82
Title 40 – Protection of the Environment
Part 82 – Protection of Stratospheric Ozone
40 CFR 745
Title 40 – Protection of the Environment
Part 745 – Lead based paint poisoning prevention in certain residential structures
NFPA 241
Standard for Safeguarding Construction, Alteration, and Demolition Operations.Provides measures for protecting life and property from fire during construction, alteration, and demolition of buildings.
ANSI/ASSE A10.6-2006
Safety Requirements for Demolition Operations
For larger-scale demolition projects such as Texas Stadium in Irving, Texas, the use of controlled explosives are the best choice. This method, however, will require months of extensive planning to prepare for demolition. This will require the services and expertise of a specialty explosives consultant. Building demolition can include items that may not be apparent at first such as any below-grade structures that would include various types of footings and foundations. Also underground utilities that provided services to the building will need to be considered during demolition.
alt=""
YouTube video showing the demolition of Texas Stadium
Demolition Scheduling and Site Protection
Requirements for demolition permits vary by state and county codes, but Federal and EPA regulations always need to be considered. State and federal projects always require the hiring of an architect or engineer to produce documents, drawings, and specifications for building demolition.
Demolition is often loosely regulated in rural areas--where buildings are not densely packed--and the built structures themselves are often smaller with fewer recyclable materials. Demolition in these circumstances is usually uncomplicated, in that the structure can be knocked down and the debris can be removed all together and taken to a landfill.
Contractors who specialize in building demolition can be hired directly by building owners, and these contractors will develop the demolition schedule and manage the project. If the owner will be occupying a portion of the site or building during demolition, a schedule of demolition activities will be useful to avoid interference with any concurrent operations and to minimize any disruption of utilities and services. If utility interruptions are not acceptable, such as in a hospital complex, temporary utilities services will need to be furnished during utility disconnects.
The owner may have additional restrictions that the contractor will need to consider when scheduling activities. Some typical owner restrictions include the protection of exterior stairs, loading docks, and entries of adjacent buildings, as well as a limitation on hours during which demolition operations may take place. However, every additional restriction the contractor needs to manage will usually be reflected in higher demolition costs. In areas with greater population density, the demolition of structures is not necessarily more complicated. Some situations are complex and mandate a high level of sensitivity to how demolition is handled, for example, demolition that takes place on a hospital campus. In these instances, a careful, piece-by-piece dismantling of the building is usually necessary, with material sorting often taking place on site. For these projects, an engineer or architect will need to be consulted to produce specifications to which the demolition must conform. The architect or engineer will produce the necessary documents which clearly outline the requirements for protecting individuals, adjacent buildings, and any remaining site improvements and utilities during the demolition operations. This becomes particularly important if the owner is to continue occupying adjacent buildings and maintaining a safe means of egress is critical. Some of the conditions that need to be controlled in order to protect the safety of individuals and property within the vicinity include: the amount of dust created, the potential release of mold into the atmosphere, and the amount of vibration produced that might affect surrounding structures or the operation of nearby equipment. Local authorities having jurisdiction should be consulted to review rules and regulations prior to any demolition activities for specific requirements for the control of dust and other pollutants during demolition operations.
Structures below grade can consist of several items, including concrete footings and foundation walls. The extent of demolition of below-grade conditions may vary depending on specific project needs. Similar to the treatment of below-grade utilities, there are generally three different options for below-grade structures:
- Abandon below-grade construction/utilities and leave in place;
- Remove below-grade construction/utilities only inside the footprint of new construction and abandon it elsewhere; and finally,
- Remove below-grade construction/utilities entirely.
Hazardous Materials
With the demolition of structures and buildings, especially older structures, comes the need to deal with hazardous materials. Through a building survey conducted by a qualified professional, the architect or engineer will know the types, extent, and condition of hazardous materials present. The safe abatement of all expected and concealed hazardous materials will need to conform to various Federal regulations. Hazardous materials include, but are not limited to asbestos, polychlorinated biphenyl (PCB), and lead.
The potential for the release of asbestos, which is the most common hazardous material found in buildings, is of particular concern. When originally used, asbestos was often sprayed or troweled on wall surfaces and also served to thermally insulate pipes and ducts or to fireproof steel members. It was also an ingredient in shingles, siding, floor tiles, caulking, and flooring adhesives. Title 40 CFR 61 – Subpart M, Section 61.145 states that any part of a building that is to be demolished or renovated must be thoroughly inspected for asbestos prior to the beginning of demolition activities. If asbestos is present, Title 29 CFR 1926.1101 provides specific requirements for controlling the exposure of asbestos.
The demolition contractor will use the services of a licensed abatement contractor (i.e., a contractor who specialize in the removal of hazardous materials) as is required when asbestos is involved. Since landfills are the collection point for construction demolition waste, landfill personnel are familiar with EPA regulations and act as a control point for that waste. Special landfills exist to receive asbestos as a controlled waste.
PCBs are heavy, oil-like liquids or solids, clear to yellow in color, and were originally used as an insulating liquid in electrical transformers, capacitors, fluorescent light ballasts, and as an ingredient in caulking. They were produced in the U.S. from 1929 to 1977, and were banned in the late 1970’s. Many studies have shown that exposure to very high levels of PCBs over a long period of time is linked to adverse health effects. The EPA provides guidelines for managing and abating PCBs in caulking.
When lead-based paints have been identified, the EPA only requires that demolition debris be treated as hazardous material if the overall demolition debris, including plaster, masonry, wood, and shingles contains more than 5 parts per million (ppm) of lead.
Homes built prior to 1978 may contain lead-based paints. The EPA has recently adopted more stringent requirements that are designed to address one of the major sources of lead pollution. This rule applies to work performed in homes and buildings occupied by children, including schools and day care centers built before lead-based paint was banned in 1978. Any contractor performing renovation or remodeling work will be required to have training and certification in lead-safe work practices by April 22, 2010, when the new regulation takes effect. In general, workers such as carpenters and painters would have to take steps to contain their work area with plastic sheeting and conduct a thorough cleanup of lead-based paint dust stirred up during construction activities. This rule however does not apply to homeowners performing their own renovations. However, the EPA does recommend that homeowners who plan to renovate, repair, or paint still practice lead-safe work habits.
Environmental Concerns
In a sense, demolition contractors were "green" before going green was mainstream, because there have long been economic incentives to recycle materials such as asphalt, wood, metal, brick, and concrete. As a result, the demolition contractor has a greater awareness of construction waste management and disposal. There is a greater interest in “deconstructing” a building to reduce the amount of waste going to landfills. This method allows the contractor to recover, reuse, and recycle much of the demolition waste.
Today, if demolition of an existing structure is required before new construction can begin on a site, the recycling of demolition waste can count toward the LEED goals for the new building. One point can be earned if 50% of the construction, demolition, and land clearing waste is recycled (or salvaged); two points can be earned if that percentage is 75%.
Codes and Standards
The Code of Federal Regulations (CFR) is divided into 50 titles representing broad areas of subject matter. These are rules published in the Federal Register by the executive departments and other agencies of the Federal Government. The purpose of the CFR is to provide a complete and comprehensive set of references intended to provide Federal regulations covering many different subject matters.
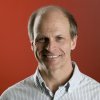
David Ingold
David Ingold is a graduate of The Ohio State University School of Architecture and a member of the Construction Specifications Institute (CSI) with Construction Documents Technology (CDT) certification. With more than 18 years of experience, David brings a broad knowledge base and understanding of design and construction to a wide variety of project types. He is an accomplished senior project administrator with experience in developing all phases of architectural documents. David has performed key responsibilities as a project leader, specifications writer, and coordinator for projects of all types and complexities including low- and high-rise condominiums, sporting facilities, higher education and government research laboratories, manufacturing facilities, wastewater treatment plants, parking garages, and campus master plans. David’s greatest aspiration is to provide construction administrative services to fully execute project designs.
Website: buildipedia.com/channels/on-site