In 2013, thousands of tons of materials were salvaged from demolition sites across the country. The environmental advantages of such salvage operations are obvious. Every ton of material that can be reused means one less ton is thrown into landfills. Considering that the United States creates 136 million tons of Construction and Demolition (C&D) waste annually, any efforts to reduce landfill volumes are laudable. However, the number one reason that salvage operations are now standard in demolition is because asset recovery can significantly reduce demolition project costs.
Property owners, therefore, have a natural motivation to recycle as much as possible. From fixtures to appliances to industrial machinery, every defunct building contains real salvage value for those willing to extract it. Today’s leading demolition firms specialize in salvaging procedures to maximize return for their customers. On a residential level, deconstruction by hand yields the most recyclable material, although it does require plenty of labor. Industrial demolition contractors tend to reclaim salvage value over several steps, starting with a sweep of fixtures and ending with processing of raw materials such as concrete.
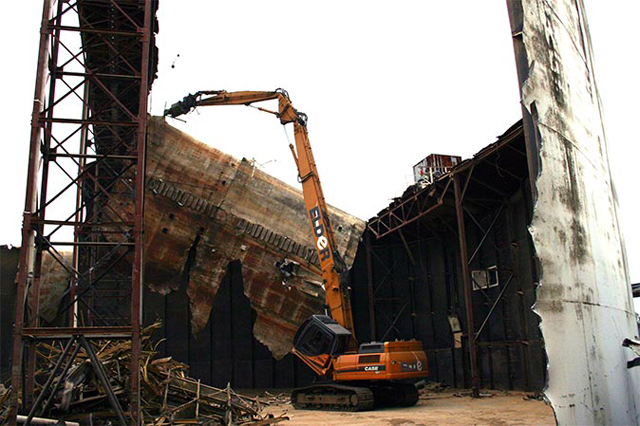
Because building materials made with recycled elements are often less expensive than their virgin counterparts, there’s a healthy demand for salvaged building elements. It’s a win-win-win situation; developers enjoy lower project costs, contractors appreciate less expensive materials, and environmental activists love sending less trash to dumps. Understandably, demolition asset recovery is a sought-after service these days, and the five at the top of the list offer high resale value.
1. Asphalt Shingles
Shingles have to be tough to survive the scorching and bone-chilling temperatures a roof suffers. Once their roofing lifespan ends, shingles can be recycled into pavement projects such as patching potholes. Moreover, because asphalt shingles contain crude oil, they can also be repurposed as fuel for cement kilns and other operations.
2. Reclaimed Wood
Provenance, beauty, and strength—these are the characteristics that make reclaimed wood products so appealing to today’s designers and consumers. Many older buildings contain weathered wood products that can be milled and processed into stunning new products, such as paneling, flooring, and countertops. Reclaimed timber may also be used for structural lumber in new building projects.
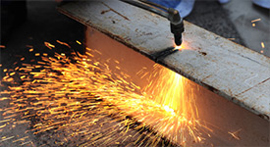
3. Steel
Steel is the one of the most frequently recycled materials on the planet, for the simple reason that it doesn’t lose structural strength after being recycled. For more than 150 years, recycled steel has been used in new buildings, bridges, cars, and more. Recycled steel is less expensive to produce than virgin steel. Plus, recycling steel causes far fewer carbon emissions than extracting new steel. In 2008, scrap metal recycling was an $86 billion industry that supported 85,000 good-paying American jobs. Steel salvaging and similar recycling efforts help to offset the country’s trade deficit while replacing former manufacturing jobs.
4. Drywall
Sandwich gypsum between two sheets of paper and you have drywall. Its high recycling value is due to drywall’s varied recycling potentials: Gypsum scraps can be used to patch walls, to form concrete, or to create new drywall. The gypsum in drywall is beloved by gardeners, who use it to nourish plants. Finally, the paper in drywall can be recycled as well. Salvaging drywall is an Earth-friendly operation, not only because it reduces landfill volumes, but also because drywall in landfills can leak sulfate into nearby watersheds.
5. Glass and Windows
Like steel, glass can be repeatedly recycled with no loss of quality. Environmentally conscious consumers and businesses are drawn to glass because it’s inherently green—for every ton of glass that’s recycled rather than extracted, a ton of natural resources are saved. Windows salvaged from demolition sites can be recycled for any number of applications, from sandblasting to paving parking lots.
Currently, 40% of the country’s landfill stream is composed of construction and demolition (C&D) debris. By salvaging as much as possible from buildings slated for destruction, demolition contractors can make a real difference for the planet. Because salvaging reduces demolition costs as well as landfill fees, building owners are naturally inclined to seek out demolition firms with salvaging expertise. The three basic steps of asset recovery—(1) identifying value, (2) redeploying what can be reused on site, and (3) selling materials that can’t be used on site—bring capital to stakeholders. Looking to the future, demolition salvage techniques can only improve, so we can expect more of today’s buildings to be reincorporated into tomorrow’s edifices.