Environmental Testing of Heavy Duty Equipment
Environmental stress testing reveals the reliability of heavy-duty construction equipment.
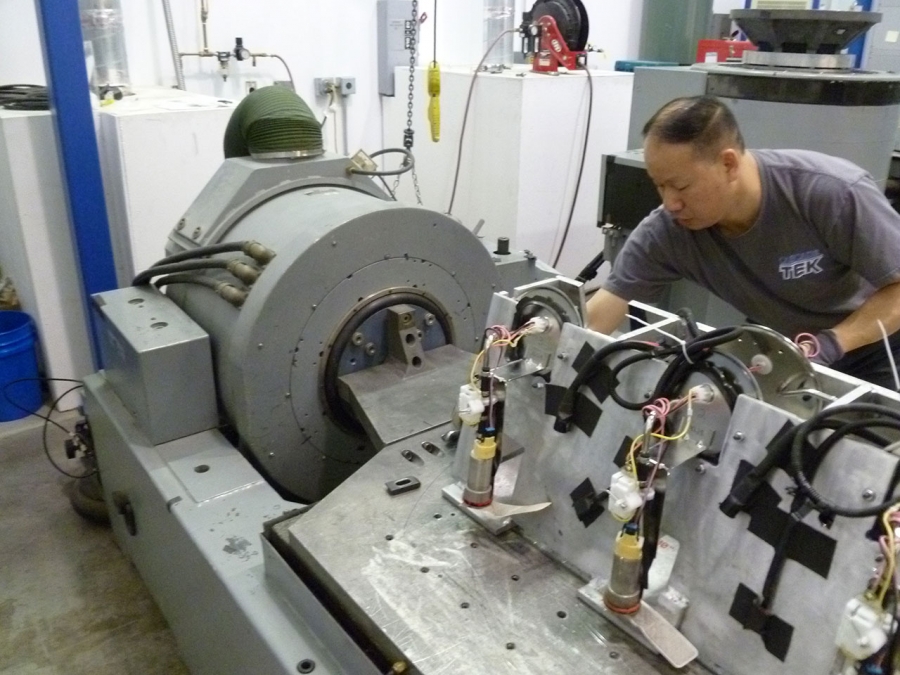
Construction equipment takes a beating. To ensure a reliable product in the field, manufacturers subject the working parts, coatings, seals, and electronics to Environmental Stress Testing before ever releasing the product to market. Here are a few of the most popular environmental tests performed in a laboratory environment on construction equipment and its components.
Sand and Dust Testing
Sand and dust test specifications are designed to test a component’s resistance to a dust-filled environment or particle bombardment. Fine dust causes problems with moving parts, forms conductive bridges, and acts as an absorbent material for the collection of water vapor. Some electromechanical components may be able to tolerate fine dust, but larger particles affect or totally inhibit mechanical action. Testing resistance to larger particles, such as sand or gravel bombardment, can ensure that the enclosure, seals, and coatings are protective. In a laboratory environment, large enclosed chambers with blowers move very specific dust, gravel, and sand types all around the product – measuring concentration, pressure, temperature, and humidity levels during the process.
Shock (Transit and Bench Handling)
Shock testing subjects the equipment to the shock impulses it will experience during shipping, loading, transport, being dropped or kicked, etc. In the laboratory environment, shock testing is performed using free-fall shock towers calibrated to emulate shock waves such as saw-tooth and half-sine shock waves. Drop testers can angle and drop a product at specified angles and from various heights to test impact on corners and sides.
Random Vibration Testing
Random vibration testing introduces vibrations the product will experience, from the hum of an engine while running to the movement of the back of a truck or on a trailer during transport. Random vibration testing can simulate very high frequencies (i.e., an engine running) to lower frequencies (i.e., transport via trailer). Vibration testing is typically done with the product positioned in all three axes (X, Y, and Z).
Temperature and Humidity Testing
Construction equipment can be used in extreme temparatures, from freezing North Dakota winters to sticky Mississippi summers. To make sure that the equipment performs in both extremes, it is subjected to temperature and humidity cycles. Extremes from –40 to 85 degrees Celsius, with conditions of 85 percent relative humidity, are common. Environmental test chambers can cycle between these temperature and humidity extremes. The product is typically operating during these tests.
Chemical Resistance Testing
Splashing, soaking, or spraying equipment and components with fluids such as fertilizers, degreasers, insecticides, hydraulic fluid, anti-freeze, fuel, bleach, and WD-40 to watch for reactions or degradation of coatings or seals is a simple, very telling exercise.
UV Exposure Testing
Weathering and UV exposure are important causes of damage to coatings, plastics, inks, and other organic materials. This damage includes gloss loss, fading, yellowing, cracking, peeling, embrittlement, loss of tensile strength, and delamination. Xenon-arc UV exposure is best for construction equipment. Xenon arc bulbs are more capable of providing a natural sunlight spectrum.
Corrosion – Salt Fog Testing
Subjecting equipment to a salt-corrosive atmosphere for extended durations can determine the quality of the coatings, plating, and seals. Large salt-fog chambers bathe the equipment in a hot, sticky salt solution. Often any connectors to and from the equipment are also part of the test to determine the ability of the connectors to withstand corrosion or moisture penetration. One of the most popular salt-fog tests used today is ASTM B117, typically a 96-hour exposure to a 5 percent salt solution.
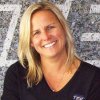
Mary Babitz
This post was written by Mary Babitz, vice president of Cascade TEK, which operates two accredited environmental testing laboratories in Oregon and Colorado. They perform reliability testing on construction equipment along with many other types of product testing.
Website: www.cascadetek.com