Masonry Mortaring
Although in ancient times masonry was often erected without mortar, the Romans discovered the benefit of using cement in making mortar to produce masonry structures which were stronger and more durable.
Contemporary Masonry Mortar is composed of cement, lime, sand, and water. The quality of the mortar depends upon the quality of its constituent parts, and the proportion of each affects the physical properties of the mortar. Each ingredient brings something different to the mix. Cement gives mortar its strength and durability; lime provides water retention, set control, and elasticity; sand acts as an inexpensive filler; and water contributes plasticity. Entrained air in the cement improves the mortar's resistance to freeze and thaw cycles.
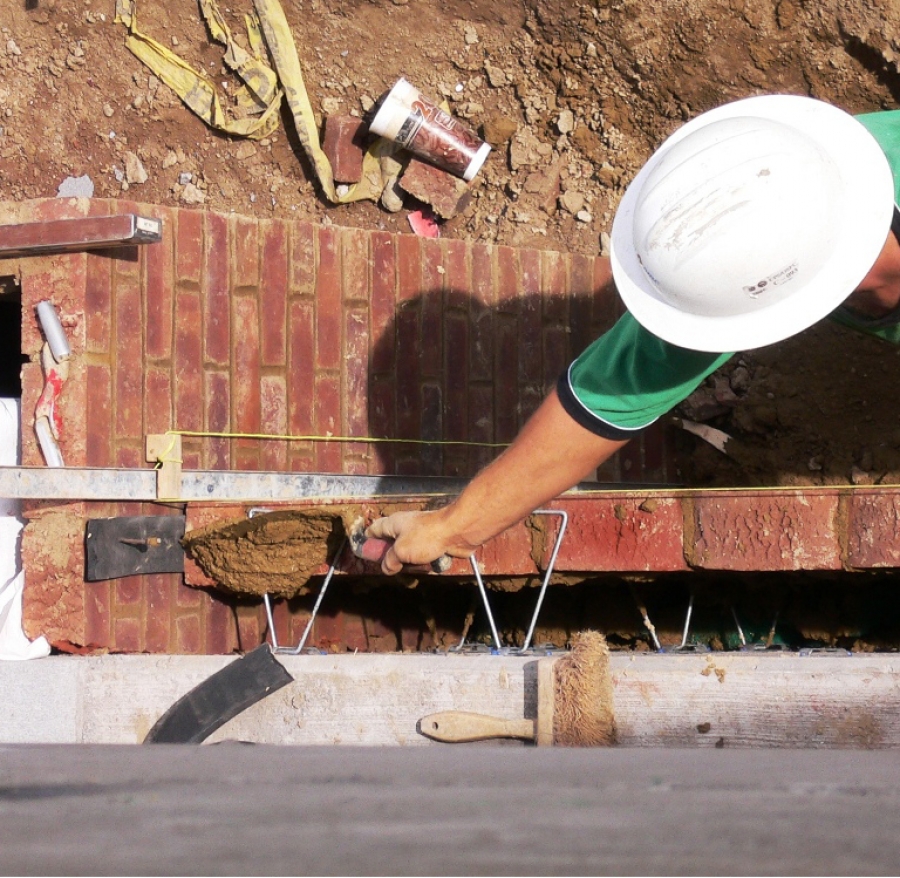
Topic Summary
Straight lime mortar was common prior to the invention of portland cement in the late 1800's. Lime mortar hardens slowly, exhibits low shrinkage, and develops relatively low compressive strength. Although lime mortar is not highly resistant to freeze-thaw cycles, when small cracks occur, it is able to mend itself by rehydrating and reconstituting. As a result, it is not unusual to find the masonry of an older building with lime mortar still in good condition.
Mortar made with straight portland cement (no lime) hardens quickly, develops high compressive strength, and has good resistance to freeze-thaw cycles, but at the same time, has low water retention and low workability. The quick setting of portland cement leaves a smaller window of opportunity to use the mortar before it starts to harden, and causes it to draw more water out of masonry units, thus reducing its ability to develop a strong bond.
Portland cement lime mortar combines the advantages of both materials and each compensates for the disadvantages of the other. Masonry cement mortars are proprietary blends of portland and other cements. The majority of designers specify portland cement lime based on its well-documented performance characteristics, while the majority of masons prefer to use masonry cement mortar, claiming the enhanced workability produces a better result while still meeting the specified performance.
The ideal sand for mortar is well-graded, with enough fine and large-sized particles to interlock into a dense, compact blend that will require a minimum of cement binder, resist flowing out of joints, and support the weight of masonry units.
Water for mortar should be free of acids, alkalis, chlorides, and organic material that could affect the performance of the mortar. Water that is pure enough to drink usually meets such criteria.
Unlike concrete, which should have as little water content as possible to maximize strength, masonry mortar needs as much water as required to maintain optimum workability. Retempering of mortar (the adding of water to replace moisture lost by evaporation) should be permitted, so long as the cement has not started to harden. Generally, mortar may be retempered as needed any time during the first 1-1/2 to 2 hours after mixing at temperatures above 80 degrees Fahrenheit, and up to 2-1/2 hours at temperatures below 80 degrees Fahrenheit. On very hot or dry days, mortar may begin to set much quicker and other measures may need to be taken.
ASTM C 270, Standard Specification for Mortar for Unit Masonry, classifies five standard mortar types, which relate to the proportion of cement and lime in the mix and the desired properties required for the particular use in a building. No single mortar type is universally recommended for all applications. The most commonly specified types, in order of decreasing minimum compressive strengths, are M, S, N, and O.
- Type M mortar is a high-compressive strength mix recommended for walls subject to high compressive loads.
- Type S mortar has high tensile bond to resist lateral loads, for locations such as below-grade walls or walls exposed to high winds or seismic forces.
- Type N is a good general purpose mortar recommended for above-ground use.
- Type O is high-lime, low compressive strength mortar, often used in residential construction for non-load-bearing walls and veneers, where exposure to freezing in the presence of moisture is not anticipated.
ASTM C 270 includes two tables specifying each mortar type design by either proportion of component materials or by minimum tested physical properties. Where engineered masonry is required, usually for larger projects that include load-bearing or reinforced walls, the property specification should be used. Proportion specifications spelled out in the building code are conservative enough to assure at least the minimum strengths of the corresponding property specification without the added cost of testing mortar mix designs.
Mortar strength does not equal durability. As a rule of thumb, mortar should have the lowest compressive strength that still meets structural requirements. The lower the compressive strength, the more flexible the mortar will be in accommodating movement in the wall without cracking.
For most projects, mortar is mixed onsite by measuring individual ingredients. Bagged, premixed mortar is available, to which only sand and water are added to the mixer on the job. The less the amount of mixing done on the job, the more consistent the mortar will be throughout the job. In some localities, ready-mix concrete suppliers also produce ready-mixed masonry mortars and grouts. Ready-mixed mortar can be delivered dry (needing only water) for storage on the jobsite in small silos or ready for use with water already mixed in. Ready-mixed mortar could be a good option for a tight jobsite with no room to store and mix ingredients.
Admixtures are neither mentioned or recommended by the standard mortar specification. Products that accelerate or retard setting may have adverse effects on mortar performance. Nothing should be added to the mortar that contains chlorides. Integral water-repellent admixtures may be added to mortar intended for use with water-repellent-treated concrete masonry units.
Natural and synthetic pigments may be used to color mortar. Most colorants are produced from iron oxides, which have proven to be stable in weathering and ultraviolet resistance. Black and dark brown pigments produced from lamp black are less resistant to weathering and fading. Products are typically supplied in premeasured packages, in powder or liquid form, to assure consistency from batch to batch.