Advanced Framing Techniques
In today’s construction world, where green is the future, it pays to know about building techniques that not only count toward a green building rating but can actually reduce up-front costs. One such method is known as Advanced Framing, sometimes called Optimum Value Engineering (OVE). Advanced Framing takes a good hard look at the way we frame buildings and tries to eliminate wood whenever possible without compromising structural integrity. All of these techniques, when properly executed, comply with the International Residential Code (IRC), but you should check local codes before beginning a project.
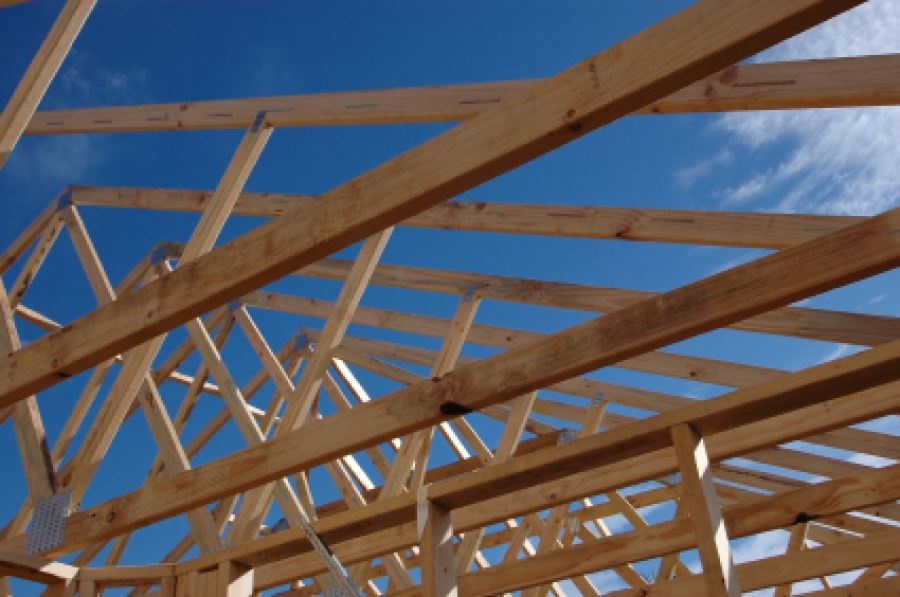
Modular Layout
Most stick framed structures can be done on a 19.2” or even 24” wall and floor spacing, especially if the exterior wall is to be built with 2 x 6s. For optimum efficiency, at least one side of window and door openings should be kept on the module. Keeping the entire building design on a 2’ module will save on waste and labor. This will not always be possible, because items such as tubs and hallways usually break the module, but designers should keep this goal in mind from the beginning of the project. If you do widen the stud spacing, make sure that cladding, subflooring, and finish materials are properly sized for the span to avoid too much deflection. Also note that 19.2” spacing is not a common width for batt insulation. You may need to use a spray foam insulation.
Stack Framing
One aspect of advanced framing or OVE is known as stack framing. Simply put, this means that the trusses (or rafters), studs, and floor joists all align so that the load transfers directly to the structural member under it. With no need to transfer load sideways to a stud, there is no need to double the top plate at the roofline or the top of the first floor walls. Interior walls can always be built without a double top plate, as long as point loads are picked up by a stud or column. A simple connector plate is used at splice points in the top plate.
The Right Header Size
Have an engineer calculate the right size for each header; the right size for a header is the size most appropriate for its load. If this is not feasible, you can follow several guidelines to reduce the amount of wood used in headers. For instance, if you’re installing a window in a non-bearing wall, you do not need a structural header because no load needs to be transferred around the window. (Some dead load is associated with the wall construction itself but this hardly justifies a double 2 x 8.) Headers in openings under gable ends, for example, can be eliminated. If the first floor has many openings, consider using a double rim joist at the second floor line instead of cutting and installing all of those headers. Just be sure that there are no joints above the openings. You may be surprised how many times you can omit some wood simply by asking yourself, “What load is this supporting?” If you cannot give a good answer to that question, the wood could be extraneous.
Jack Studs and Cripple Studs
Again, this is a place where status quo practices find the construction industry using more wood than is really required. The use of header hangers can eliminate the need for jack studs in most cases, and the only reason for putting in a cripple stud is for drywall attachment. Today’s windows are hung, not supported from below, so putting cripple studs under a window for purposes other than drywall attachment is simply a waste of time and material.
Eliminate Extraneous Blocking
Blocking drywall is a job that commonly finds builders using more wood than necessary. Not only does this waste wood and money, but it can create pockets of uninsulated exterior wall that lead to energy loss and cause cracking drywall. By using drywall clips, ladder bracing, and scrap wood blocking we can eliminate this excess wood. Your plumber and electrician will also love these methods because they eliminate the need to drill holes through extraneous wood blocking.
Elimination of Sheathing
Many aspects of advanced framing or OVE have met with some resistance from the construction community. None of these methods has met with more resistance than the elimination of exterior plywood sheathing, and this may well be for good reason. It is possible to eliminate exterior sheathing from a wood framed building by providing metal strapping for lateral stability. Some systems have flat straps, while others are T-shaped. These systems are basically metal alternatives to 1 x 4 let-in bracing, with less labor involved. For complete confidence, you should probably have a structural engineer design the bracing; at the very least you should proceed with strict adherence to the manufacturer’s specifications. Another method of gaining shear resistance without sheathing is by installing shear panels. Metal or wood pre-engineered panels are used in the stud spaces near the corners of the building. Again, panels should be placed with strict adherence to the manufacturer’s specifications and/or according to the design of the structural engineer.
Some of the issues with these systems include the concern that it can be difficult to get enough strapping for lateral bracing in a wall penetrated by many windows and doors. Also, wood sheathing tends to lock the entire structure together. The wood sheathing spans the entire wall, from the bottom of the rim joist to the bottom edge of the roof trusses. Wood sheathing thus provides an extra level of rigidity that metal strapping and panels generally cannot provide.
The U.S. Department of Energy estimates that advanced framing or OVE can save an average in materials cost of $500 per 1,200 sq. ft. of house, with an additional 3%–5% labor savings. It also estimates that the elimination of cold corners and other insulation voids, coupled with the reduced thermal bridging of wider stud spacing, can increase the effective R-value of exterior walls by as much as 30%, resulting in 5% annual energy savings for the homeowner. After a brief learning curve, the material and labor savings associated with advanced framing will result in getting projects under roof faster, and that means fewer weather delays and less water soaking into building materials. Wet building materials can possibly cause indoor air quality issues down the road, including black mold. If you want to learn more about advanced framing, the Energy and Environmental Building Alliance has a series of Builders Guides that are great resources. Energy Star also puts out a checklist on quality framing that focuses on Optimum Value Engineering (OVE).
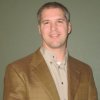
Robert Shearer
Robert W. Shearer is a licensed architect and member of the American Institute of Architects. He holds a Bachelor of Architecture degree from Kent State University, with a minor in mathematics. He is a LEED Accredited Professional, and a Certified Green Professional (National Association of Home Builders). He has more than 13 years of experience in the building and design field, with 5 years of experience working for a commercial developer. Green building and renovation is a passion that he has had for years, and he has done extensive research on the subject. He has also honed his DIY skills during extensive renovation on his own century home.
Website: www.rwsarchitect.com/