Successive Alkalinity-Producing Systems (SAPS)
Video
A challenge of mining operations and any project that disturbs large volumes of earth below grade is the potential to generate contaminated water runoff at the surface known as acid mine drainage (AMD). Precious metal and coal mine shafts traditionally require excavation below the water table, exposing metal sulfides in the disturbed earth and waste soils to the atmosphere and water. Similar exposure can occur during major highway construction projects. Stormwater runoff and water discharged from dewatering pumps related to these construction activities can be very low in pH (acidic) and can contain harmful metal ions. Eric McCleary of Greenhorne & O’Mara helped develop the successive alkalinity-producing system (SAPS) process to treat this AMD water and shares insights regarding this innovative technology with the Buildipedia audience.
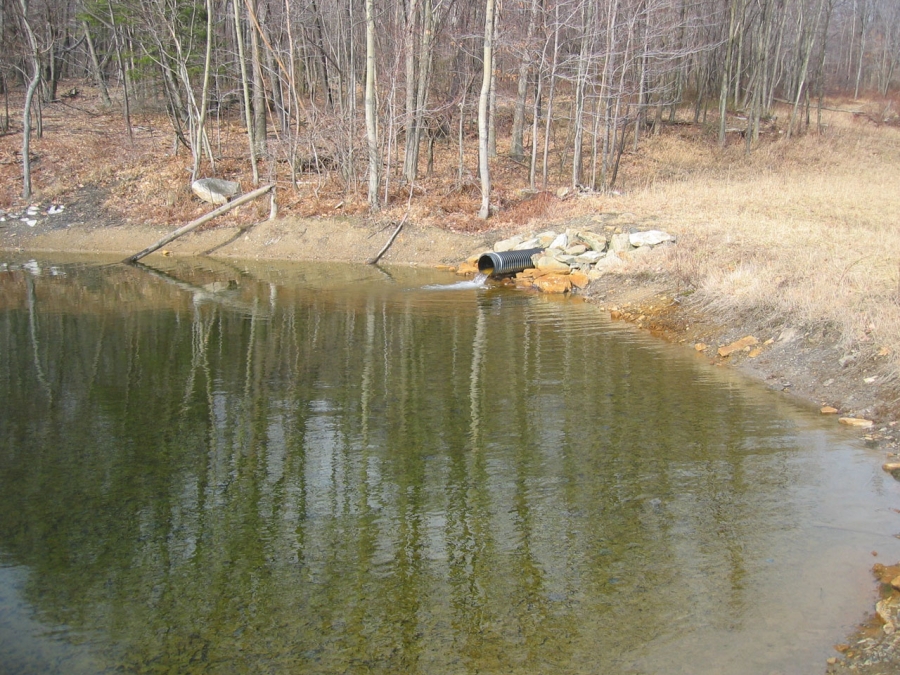
SAPS Overview
A successive alkalinity-producing system (SAPS) collects acid mine drainage (AMD) water, stores it vertically within a containment structure, and allows the hydrostatic pressure of the stored water column to push the AMD water through layers of organic material and limestone. A concentrated layer of organic material (mushroom compost) replicates the natural chemical and physical processes that occur in a compost wetland. A limestone layer beneath the compost layer adds alkalinity. Metal ions, including iron, aluminum, manganese, and others can then precipitate from AMD water. One advantage of a vertical flow system over a horizontal flow system is the hydrostatic head provides a self-cleaning side effect – metal deposits are not as likely to clog discharge lines, especially if proper design features are added.
Water Chemistry Basics
Metal Ions and pH. Metal sulfide exposure results in chemical reactions that release free hydrogen (and metal ions) into water discharged from the mine or mining wastes, lowering the water’s pH value. As the pH of the water is lowered and becomes more acidic, the metal ions in the discharge water tend to remain in solution. Water from mining operations that contain high concentrations of metal ions and/or are low in pH can be very damaging to the surrounding environment when discharged without treatment.
Above find a successive alkalinity-producing system (SAPS) receiving discharge from a coal mine in central Pennsylvania. The water has a pH below 3.5, an iron content above 100 mg/L, and an aluminum content of about 45 mg/L. Note the ferric iron that has precipitated on the rocks near the in-fall pipe.
Alkalinity and Acidity. Alkalinity is the opposite of acidity and represents the capacity of a water sample to react with hydrogen ions [like those released by the metal sulfides’ chemical reactions in acid mine drainage (AMD) water] and neutralize acidity. Once the alkalinity of the water and the pH are increased, metal ions in the wastewater stream can be removed from solution more readily. AMD water has particularly high concentrations of metal ions and also has a lower pH value than most typical stormwater flows – pH ranges between 3 and 5 are common in untreated AMD water.
Traditional System Challenges
Considering the flow rates, pH levels, and metal ion concentrations of acid mine drainage (AMD) water presented to a given treatment process, achieving the desired acidity and metal ion reductions required can be challenging. Traditional alkalinity-producing systems like horizontal-flow anoxic limestone drains (ALDs) are constructed similar to French drains. They are not effective at handling high acid concentrations and the typically high aluminum and ferric iron levels within AMD water. ALDs are designed to add alkalinity but not to remove metal ions, so outflow clogging is common. Compost wetlands are effective but require large land areas and high retention times to achieve the desired results. The successive alkalinity-producing system (SAPS) combines these two techniques and allows for greater acidity reduction with more reasonable processing times and physical area allowances.
Above find the same SAPS unit drained for maintenance. The compost layer shown will be removed and replaced. The limestone layer below the compost will be replaced.
SAPS Basic Design and Construction
A successive alkalinity-producing system (SAPS) can be constructed within buried polyethylene tanks or concrete vaults similar to septic tanks, new excavations, or reconditioned surface impoundments. Approximately 2’–4’ of limestone is placed in the bottom of the containment structure. Directly above that layer of limestone is a 6" – 12” layer of organic material, consisting routinely of spent mushroom compost (i.e., an organic medium comprising materials like manure and straw that was sterilized during mushroom cultivation). The limestone and compost layers remain separate and stratified during SAPS use: there’s no need for filter fabrics or screens to keep these layers in place. A nominal 3'–4’ layer of acid mine drainage (AMD) water is typically maintained above the compost layer during treatment.
The compost layer’s purpose is to prepare an anoxic environment created by the high biochemical oxygen (BOD) demand of the compost material and to filter some precipitates (iron sulfide, for one) that will adhere to the compost material as the acid mine drainage (AMD) water transitions to the anaerobic zone of the compost. The limestone layer beneath increases alkalinity and raises pH levels – the anaerobic environment created by the compost above aids in the production of carbonate alkalinity as the limestone dissolves. These physical and chemical processes are required in succession to treat the AMD water efficiently, increase the water’s pH, and precipitate the targeted metal ions from the waste stream when exposed to oxygen.
Above find a SAPS unit for an electric utility on the East Coast. This pond receives groundwater with an initial pH between 3.5 and 4, pumped at a rate of 110 gallons per minute from an abandoned fly-ash landfill.
Perforated PVC piping and flush valves are installed at various zones throughout the containment structure to draw off (or bypass, when needed) treated water at the desired points from the SAPS. Piping manifolds are constructed to allow for the envisioned gravity flow rates to and from the SAPS.
Each SAPS can treat a maximum of about 300 mg/l of acidity. SAPS tanks or containment structures can be arranged in series, if necessary, to treat AMD water with higher acidities. For example, AMD water with a total acidity of 1,000 mg/l might be treatable with three to four SAPS containers in series.
In addition to the central key component – the SAPS containment unit with compost and limestone layers – piping, sedimentation ponds, and aeration spillways may also be recommended, depending on the AMD water flow rates and chemical constituents at a particular site.
SAPS Operational Details
Acid mine drainage (AMD) water is intercepted as a point source discharge in most cases. In the occasional instances where AMD water appears as seepage throughout a broader area like a hillside, trenches can be constructed at the base of a hill to collect the AMD water and then provide it to the successive alkalinity-producing system (SAPS) unit. An analysis of the AMD water is required in advance of the SAPS design, but there are many consistencies that emerge due to basic water chemistry.
Aluminum Removal. Aluminum will precipitate out of water at a pH level of about 5.0 (or higher). Therefore, part of a SAPS design envisioned to treat high aluminum content will be to flush AMD water from a SAPS.
Effluent flushed at this stage from a SAPS specifically designed to treat aluminum contamination will be diverted to a settling pond. Inert elemental aluminum will settle across the base of the pond as a layer of sediment. One potential benefit of future SAPS is the recovery of aluminum from settling ponds; this recovery has yet to achieve marketability due to economy of scale, but studies continue.
Above find a SAPS unit being constructed near Snow Shoe, Pennsylvania. This unit is designed to handle flows of 70 gallons per minute. The PVC underdrain system has a limestone bed and will be covered with another 3' of limestone (visible in the background). Mushroom compost will be placed on top of the limestone layer.
Iron Removal. Iron (Fe) will tend to remain in solution as ferrous iron (Fe+2) in anaerobic environments with low pH (or "reducing environments"), such as those in subsurface groundwater flows or when acid mine drainage (AMD) water transitions through the compost layer within a successive alkalinity-producing system (SAPS) containment. When AMD water is exposed to ambient air, the ferrous iron in solution will oxidize and transform into the more stable, insoluble form of ferric (Fe+3) iron. SAPS designs may include a riprap spillway to process effluent downstream from the SAPS containment. This step oxygenates the AMD water and precipitates iron from it, staining the riprap with the typical rust coloring.
Other Metal Removal. Manganese behaves similarly to iron. It tends to remain in solution in water without oxygen and with a low pH. Therefore, the successive alkalinity-producing system (SAPS) process is effective at removing manganese from water (after iron and aluminum have been removed,) and some SAPS are now also being employed to treat acid mine drainage (AMD) water containing various metal contaminants from precious metal mines in the western United States.
The chemical and pH properties of SAPS influents and effluents routinely undergo laboratory testing as desired by the site owners or as required by regulatory agencies. Recurring inspection and maintenance of the compost and limestone layers, pipes, and valves over intervals of many months are recommended depending on site conditions and flow rates. A SAPS can operate for many years with minimal replenishment of the compost and limestone layers, achieving low operational costs. In contrast, many of the traditional AMD water treatment processes require more expensive chemical solutions involving sodium hydroxide, sodium carbonate, or hydrated lime.
Eric McCleary is a biologist and water treatment specialist with Greenhorne & O’Mara. He developed the SAPS and and is now working to implement SAPS for treating frac water from natural gas wells and metal mines in the western United States in addition to waters associated with coal and other mines.
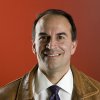
Andrew Kimos
Andrew Kimos completed the civil engineering programs at the U.S. Coast Guard Academy (B.S. 1987) and the University of Illinois (M.S. 1992) and is a registered Professional Engineer in the state of Wisconsin. He served as a design engineer, construction project manager, facilities engineer, and executive leader in the Coast Guard for over 20 years. He worked as a regional airline pilot in the western U.S. before joining the Buildipedia.com team as Operations Channel Producer.
Website: buildipedia.com/channels/operations