Form Traveller System Bridge Construction: Out-spanning Traditional Methods
The use of form traveller systems offers significant cost savings for bridge construction projects throughout the world. We've partnered with Miguel Barreto from ConstruGomes of Portugal to highlight the key aspects of form traveller systems: how they offer cost advantages over traditional construction systems, in what situations they can best be utilized, and how they function.
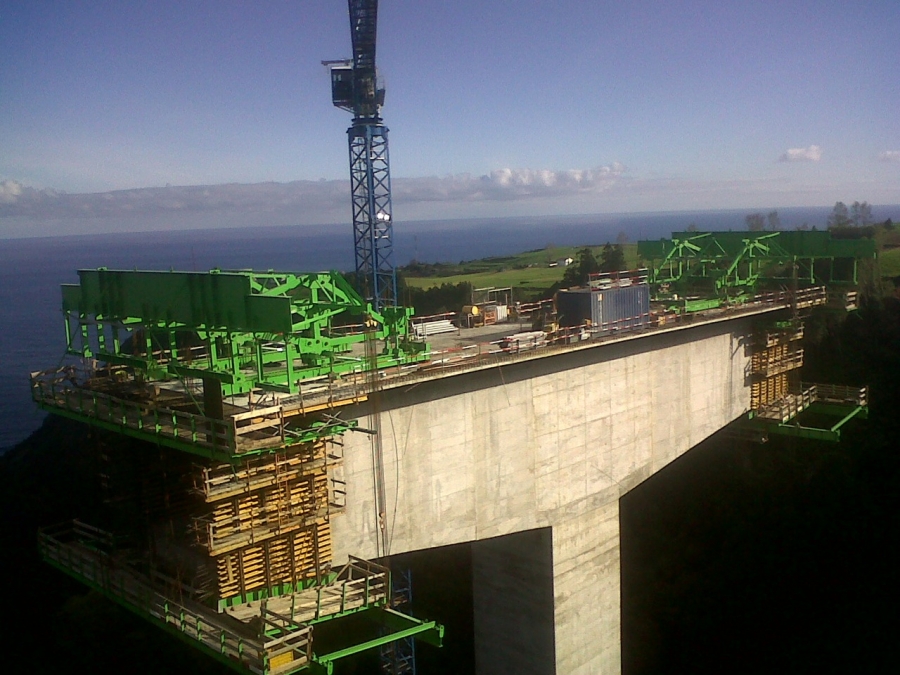
Form Traveller Bridge Construction
Form Traveller Specifics
Form travellers can be employed during cantilevered concrete girder construction when a bridge pier can be used as a starting point. Opposite directions of span construction are facilitated by using the top of a pier as the initial anchor point for two separate form travellers (each pair of form travellers operates as a unit). Cantilevered construction is allowed by moving each pair of form travellers farther away from a pier in tandem. The weight is therefore always balanced, and the static forces on the pier maintain equilibrium. The incremental movement of each pair of form travellers is the critical path to project completion.
Work progress is limited to span increments of approximately 5 m (approx. 16') or 400 tons per week on each side of a pier. However, the key advantage of form travellers is their ability to span great distances in remote locations. If the contractor can access the piers, the bridge can generally be built with form travellers, including angled bridge decks with varying turn radii. Form travellers are preferred for building spans over deep valleys, waterways, and roads where access from the ground is a challenge and the number of piers is limited (especially for the central span).
- Form Traveller Delivery: Form traveller equipment can be trucked to the job site in multiple shipments or barged to the site if a bridge is being constructed over a navigable waterway.
- Form Traveller Operation and Training: Form travellers are powered by a hydraulic system, requiring the crews that operate them to receive specific training. The structural framework of the form traveller moves forward on rails anchored to the previously constructed span segments. The individual steel structural members of each form traveller are connected with pins to facilitate mobilization/demobilization.
- Form Traveller Installation: Form traveller equipment is assembled on the ground, and segments are then lifted by crane to their starting points on a specific bridge pier. Demobilization follows the same process in reverse. Sections are placed on the ground by crane and further disassembled into shippable parts.
Form Travellers vs. Traditional Construction
The main advantage of form travellers over other construction methods is that they allow for longer and wider spans to be built in challenging site conditions. Form travellers are better suited for bridge designs involving fewer piers because they can span much greater distances than other methods. This chart generically summarizes the maximum spans, widths, and timelines allowed by various concrete bridge construction techniques.
Form Travellers |
Moving Scaffolding Systems (MSS) |
Incremental Launching |
Pre-Cast |
Heavy Duty Propping System |
Traditional Scaffolding |
|
Max Span |
250 m (approx. 820') |
90 m (approx. 295') |
80 m (approx. 262') | 60m (approx. 196 feet) |
Limited to 40m (approx. 131 feet) between propping towers |
Limited to 25m (approx. 82 feet) between scaffold towers |
Typical Span |
Up to 170 m (approx. 557') |
Up to 55 m (approx. 180') |
60 m (approx. 197') |
45m (approx. 147 feet) |
35m (approx. 114 feet) |
20m (approx. 65 feet) |
Max Width |
30 m (approx. 98') |
20 m (approx. 65') |
20 m (approx. 65') |
No limit |
No limit |
No limit |
Typical Width |
Up to 25 m (approx. 82') |
20 m (approx. 65') |
15 m (approx. 49') |
No limit |
No limit |
No limit |
Max Span/Week |
10 m (approx. 32') per pair of form travellers |
60 m (approx. 197') |
40 m (approx. 131') |
60m |
One span per week |
One span per week |
Moving Scaffolding Systems (MSS)
Moving scaffolding systems (MSS) cannot take full advantage of cantilevered construction techniques as compared to form travellers. Customized (expensive) MSS equipment is required for bridge decks greater than 20 m (approx. 65'). Moving scaffolding systems can be more cost-effective for long bridges with equal repeated spans (or multiple spans) because it is generally a quicker method: 30–60 m (approx. 98–196') span every week, or 60–90 m (approx. 196–295') span every two weeks. For bridge decks with a substantial turn radius, the MSS become less easy to operate. The MSS structure has to extend outward and move around constructed bridge piers as shown in this video.
Incremental Launching
Incremental launching is preferred for long straight bridge spans or those with a large and constant turn radius. This method becomes less feasible when the design requires an angled bridge deck relative to the horizon or a flat deck with a varying turn radius. The placement of each span increment is limited by the size of the hydraulic system pushing each span segment into place. Initial installation costs of the launching equipment (cables, hydraulics, rollers, etc.) is high, generally becoming more cost-effective as total bridge lengths approach 400 m (approx. 1,312'). It is usually good for small wide bridge decks that can be built in consistent segments, such as railroad bridges. It is also a good option in places where the bridge is high because the contractor doesn't need to use cranes or transports along the bridge to place deck segments. Concrete and steel materials are staged at a consistent location, so the system works similarly to a production factory.
Pre-Cast Materials
Pre-cast construction is often not suitable for larger spans. The length of the pre-cast concrete members is limited by factory equipment, the behavior of formed concrete, and shipping considerations. The use of pre-cast members is not feasible in some remote areas due to poor access roads. Transporting and elevating pre-cast members with cranes can be particularly challenging for bridge projects with poor access, rivers, or low support conditions. The higher a project’s bridge piers, the higher the cost of crane operations (i.e., larger crane equipment is required).
Heavy Propping and Traditional Scaffold Formwork
When the bridge spans are located at significant heights above grade, traditional formwork becomes no longer feasible since it requires bracing to ground. It becomes more labor-intensive and tedious as span lengths and pier heights increase. ConstruGomes has used heavy propped formwork up to only 40 m (approx. 131') of bridge span and height. These systems are normally limited to a height of 40 m because of material limitations and safety considerations. The spans can be large because they can have multiple support towers on the ground. The limit of 40 m of span is between a set of propping towers only.
Self-Climbing Formwork
Self-climbing formwork operates similarly to form travellers but builds piers vertically in increments as opposed to bridge decks laterally. Self-climbing formwork is installed at grade and can be used to construct the entire height of a new cast-in-place concrete pier. Lifts of up to 5 m (approx. 15') every 2–3 days can be achieved. Self-climbing formwork needs a constructed pier height of only 1 m (approx. 3') to begin operations.
Image Gallery
This image gallery below of ConstruGomes projects in the Marao Mountains and the Azores highlights their use of form travellers and self-climbing formwork in state-of-the-art bridge construction.
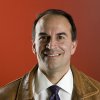
Andrew Kimos
Andrew Kimos completed the civil engineering programs at the U.S. Coast Guard Academy (B.S. 1987) and the University of Illinois (M.S. 1992) and is a registered Professional Engineer in the state of Wisconsin. He served as a design engineer, construction project manager, facilities engineer, and executive leader in the Coast Guard for over 20 years. He worked as a regional airline pilot in the western U.S. before joining the Buildipedia.com team as Operations Channel Producer.
Website: buildipedia.com/channels/operations