Guardrails: Design Criteria, Building Codes, & Installation
Designing and Installing a Safe System
Almost every commercial and public building, whether it is an office building, sports arena, place of worship, or school building, contains a guardrail system. Guardrail systems are installed to provide safety and protection for the building occupants and are placed at or near the outer edges, of flights of stairs, ramps, landings, platforms, balconies and accessible areas of roofs. They will also be found at the perimeter edge of any opening or accessible surface, such as an opening for a stairway, or at a location where operating conditions require limited access to a designated area in order to guard against accidental falls.
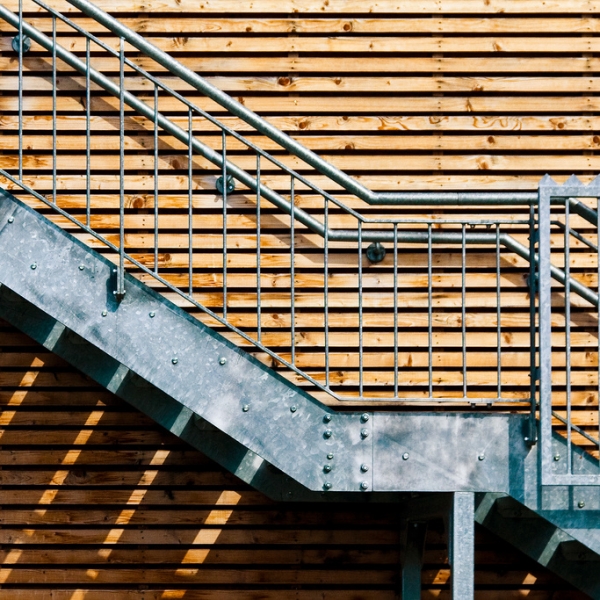
The International Building Code (IBC) definition of a "Guard" (also typically referred to as a "guardrail") is "a building component or a system of building components located at or near the open sides of elevated walking surfaces that minimizes the possibility of a fall from the walking surface to a lower level." A horizontal or sloping rail intended for grasping by the hand for guidance and support describes a handrail, which should not be confused with a guardrail.
For a guardrail system to perform as designed and provide a safe environment, the follow items need to be considered:
- Design criteria and codes
- Design responsibility
- Appropriate installation methods
Design Criteria and Building Codes
Railing System Standards
ASTM International:
- ASTM E 894 Test Method for Anchorage of Permanent Metal Railing Systems and Rails for Buildings
- ASTM E 935 Test Methods for Performance of Permanent Metal Railing Systems and Rails for Buildings
- ASTM E 985 Specification for Permanent Metal Railing Systems and Rails for Buildings
- ASTM E 1481 Terminology of Railing Systems and Rails for Buildings
American Society of Civil Engineers:
- ASCE 7 Minimum Design Loads for Buildings and Other Structures
American National Standards Institute:
- ANSI A 117.1 Guidelines for Accessible and Usable Buildings and Facilities
- ANSI A 1264.1 Safety Requirements for Workplace Floor and Wall Openings, Stairs, and Railing Systems
National Fire Protection Association:
- NFPA 101 Life Safety Code
There are many government regulations that the architect and engineer need to be aware of during the course of designing a building. There is the new, updated International Building Code, which contains references to such associations as American Society of Civil Engineers (ASCE), American National Standards Institute (ANSI), and ASTM International. Also, the Occupational Safety and Health Administration (OSHA) and Americans with Disabilities Act (ADA) must be considered. Designers face the continuing task of interpreting these documents and applying them to specific situations. With all of these codes, regulations, and standards, designing guardrail systems can be challenging. These regulations will also have a significant impact with the fabricator and ultimately the contractor during installation. The intent of design regulations for guardrail systems is to help to determine the sizes and dimensions of components, ensuring that the system meets the specified loads for the required service conditions and, ultimately, provides protection against persons falling when installed correctly.
The 2006 International Building Code (IBC 2006) generally requires guardrails when the difference in elevation between the upper and lower surfaces is 30 inches or greater.
The following is based on the 2006 IBC:
- Structural capacities: handrails, guardrails, and their supports must be designed for 50 lbs per linear foot, applied in any direction at the top of the top rail, and a concentrated load of 200 lbs applied in any direction at any location along the top of the top rail.
- Guardrail infill and bottom rails are to be designed for 100 lbs acting on a projected area of 1 sq. ft, including the open space between components.
- Height: where required, guardrail height must be a minimum of 42 inches above the leading edge of the tread or walking surface.
- Opening limitations: open guards shall have balusters or ornamental patterns such that a 4 inch diameter sphere cannot pass through any opening up to a height of 34 inches. From 34 inches to 42 inches above the walking surface, a sphere 8 inches in diameter shall not pass.
- Mechanical equipment: rooftop equipment that requires servicing, as well as roof hatches that are located within 10 feet of the roof edge, require guards. These guards shall be constructed to prevent the passage of a 21 inch diameter sphere.
It is more common than one might expect to find guardrails and handrails that do not meet the minimum code requirements, or that are not installed or designed properly. Guardrails that do not meet the minimum structural load capacities, or those that have excessive deflection, present a real danger to the public.
When a guardrail has a significant amount of deflection, it will give a sense that the railing is not safe or that it is not structurally stable. In this condition, the railing can be considered improperly constructed or designed. With repeated excess deflections, the connections can become fatigued and possibly fail. Railing posts should be designed for a maximum allowable deflection of L/120 (h/60).
Design Responsibility
A major consideration for architects and engineers is the liability that guardrails and handrails present. As is evident in many of the federal regulations and codes, more stringent requirements of design loads for railing systems have been adopted and implemented to provide an increased level of public safety. As such, the structural design of railing systems has become exceedingly important. Additionally, it will be the contractor's responsibility to demonstrate compliance with all the performance language required by the specifications as well as all referenced codes.
Initially, the architect, with assistance from the consulting engineer, will produce the drawings needed for guardrail systems. Many times schematic drawings, along with supplementation by the project specification manual, are sufficient for more standard configurations. Schematic drawings will usually indicate the overall dimensions and attachment locations that the fabricator will need in order to provide shop drawings. When necessary, specific member sizes, components, and details are indicated in the construction documents by the architect. At this point the contractor and fabricator will need to comply with these details. However, these do become the responsibility of the licensed design professional.
When only schematic drawings are provided, it is necessary that the project’s specifications be coordinated to provide the necessary language for a complete system. At a minimum, the drawings should show all the locations and the extent of the guardrail system, all sufficiently dimensioned in plans, elevations, and details. The guard infill design can often be covered in the specifications when standard member sizes are adequate to the design intent.
If the contractor is required to assume responsibility for design, this will be defined in the Performance Requirements section of the specifications. The Performance Requirements section of the specifications manual will outline the necessary engineering analysis expected to be performed.
Installation Methods
Once the guardrail system has been fabricated to meet the structural design, the final step is installation. For any given guardrail system to successfully perform its function of providing a barrier that prevents occupants of a building from falling to a lower level, it must be installed correctly. Installation is as important as the structural design and fabrication of the system, since any deficiency in the installation can cause failure. It is essential, therefore, that careful attention be paid to the details of installation and anchorage.
Because it is the posts of the guardrail system that are connected to the building supporting structure, the bases of the posts are the most critical points in any railing system. This is where the greatest stresses will occur. Mounting posts to the building structure can be done in various ways, and each condition may be different. Some more common methods include the following:
- Railing systems mounted on a fascia or face stringer. This method can offer several advantages, including the fact that the railing system does not reduce the width of the stair or platform. Also, with standard stock fittings, installation becomes easy as there is no need for field welding.
- Railing systems that are set into new concrete or masonry floors. Sleeves of pipe, sheet metal, removable fiber, cardboard, or foam polystyrene (provided by the railing system fabricator) are used during construction to form holes for receiving the posts. The sleeves shall be large enough to allow for field variation in their spacing or alignment and still leave sufficient space for grouting. The sleeves are to be of sufficient depth to provide ample post support and shall be kept covered until the railing system is installed, to prevent accumulation of debris or collection of water subject to freezing.
- Railing systems that are set on an existing floor. When a railing system is to be set on an existing floor, post holes will need to be drilled with a core drill. The edge of the hole should be at least 3 1/2" from the edge of the concrete or masonry.
- Railing systems that are mounted on the floor surface or stair tread. This mounting system will need to be designed to withstand the required loading. Bracing can be achieved by providing a change in the direction of the rail. If a railing system is to be mounted on top of the narrow flange of a light (MC) stringer channel, calculations on the stringer will need to be done to determine if stiffeners are required. A railing system attached to an open riser stair having thin concrete or terrazzo treads and no face stringer poses a special attachment problem. This condition will require additional bracing and engineering calculations.
Code requirements, material availability, and even material costs can affect the final design of the guardrail. Structural design will be required for each specific condition to assure the system's integrity. Finally, it needs to be clear from the beginning who will be responsible for ensuring the design. The design of the guardrail must consider strength and serviceability that meets ADA requirements.
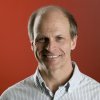
David Ingold
David Ingold is a graduate of The Ohio State University School of Architecture and a member of the Construction Specifications Institute (CSI) with Construction Documents Technology (CDT) certification. With more than 18 years of experience, David brings a broad knowledge base and understanding of design and construction to a wide variety of project types. He is an accomplished senior project administrator with experience in developing all phases of architectural documents. David has performed key responsibilities as a project leader, specifications writer, and coordinator for projects of all types and complexities including low- and high-rise condominiums, sporting facilities, higher education and government research laboratories, manufacturing facilities, wastewater treatment plants, parking garages, and campus master plans. David’s greatest aspiration is to provide construction administrative services to fully execute project designs.
Website: buildipedia.com/channels/on-site