The New Standard of Sustainable Manufacturing Practices
Video
Gone are the days when cutting-edge sustainability practices yielded a significant competitive advantage for building product manufacturers. Today’s builders and homeowners not only expect to be able to choose from a wide assortment of environmentally friendly products, they also expect that the companies behind the products to engage in robust sustainability practices when it comes to company culture as well as operations and manufacturing processes. As a result, sustainability has become a cornerstone of doing business for manufacturers, rather than an afterthought.
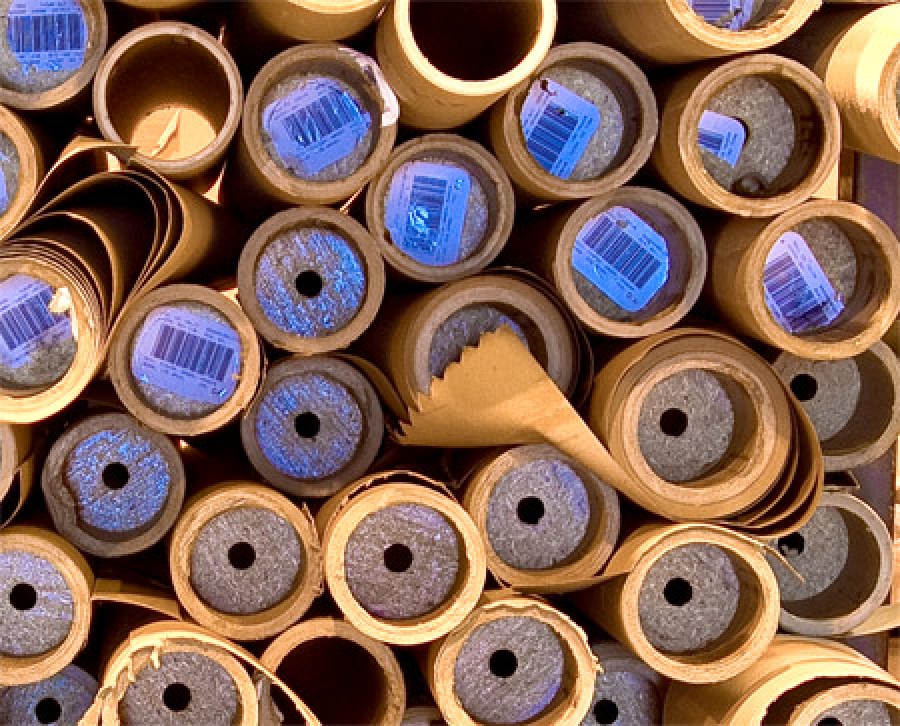
“Environmental stewardship doesn’t just impact a few aspects of our business,” says Tammy Weadock with Wilsonart, a worldwide leader in decorative laminate and solid surface products. “It’s a big part of our culture and what we stand for as a company. It’s the way we do business.”
Kolbe & Kolbe Millwork Co., Inc., a leading window and door manufacturer, shares a similar mindset. “We believe that quality is in the details,” says Lance Premeau. "We strive to make a difference both in how we manufacture our products and the ways in which this makes a positive impact on the environment."
Gary Nesslar with Design Elite Tampa Bay says that a manufacturer’s environmental story matters. “We prefer to work with manufacturers who are sustainability-focused,” he says. “For example, Cambria’s sustainability approach is a factor in us choosing to sell and install Cambria Quartz countertops; it certainly has an impact on the overall quality and value of the product.”
“No matter how small a leak, it takes more energy to push air through a leaky hose. Preventative maintenance not only helps save energy, it also saves money and natural resources.” Lance Premeau, Kolbe & Kolbe Millwork
Although sustainable practices now permeate many aspects of a company’s culture and operations, we set out to uncover the latest environmental trends impacting behind-the-scenes manufacturing processes – only to find that the current practices aren’t exactly trends. Rather, they have become the new standard, and when it comes to the new standard in manufacturing processes, two key tenets of sustainability are front and center: energy usage and waste management.
Energy Usage
Perhaps one of the biggest changes in manufacturing in the last several years has to do with the amount of energy and electricity that is used within a facility, as well as the type of energy that fuels its operations.
For example, in order to minimize electricity usage, Wilsonart replaced nearly 3,600 existing lights in its Temple North and Plate Plant facilities with high-efficiency T8 fluorescent fixtures. “We were able to recycle the old high-intensity discharge bulbs, and our new fixtures are almost twice as efficient in converting electrical energy to light at the same or greater light output,” says Weadock. “This has resulted in a 50% reduction in electrical consumption for lighting, as well as a 10% reduction in our overall electricity use.”
To conserve electricity, Wilsonart also installed motion detectors in low-traffic areas within its facilities. “The lights only come on when people are present, which helps us conserve resources,” says Weadock. “We also shut down our countertop sanders from 2 pm until 4 pm daily to avoid running during peak energy hours and to help reduce the strain on our provider.”
Energy efficiency is also a focus for Kolbe & Kolbe Millwork. “During the last few years, we have retrofitted our lighting in order to have the most efficient bulbs and ballasts possible,” says Premeau.
One other important aspect of Kolbe & Kolbe’s energy conservation plan is the use of preventative maintenance on its pneumatic systems. “We have a rigorous program in place to carefully monitor and remedy air leaks,” says Premeau. “No matter how small a leak, it takes more energy to push air through a leaky hose. Preventative maintenance not only helps save energy, it also saves money and natural resources.”
"This unit [the cyclomizer] stores hot water and allows for its reuse after additional heat is added during the next press load. It also stores the cooling water and re-cools it before the next cycle begins. This equipment not only increases the efficiency of energy use, but it’s a closed-loop system that reuses water over and over.” Tammy Weadock, Wilsonart
When it comes to the type of energy being used to fuel the equipment in manufacturing facilities, manufacturers are turning to cleaner, greener sources than those used in years past. Wilsonart employs several methods within its plants to create renewable energy. “We use the heat from our dust incineration process and the fumes from our resin incineration process to generate steam for our laminate presses,” says Weadock. “This reduces our natural gas use by 30% to 40% annually.”
Weadock also said that the company has reduced its use of propane by using rechargeable batteries to fuel its forklifts and other small vehicles. “The electric advantage includes no fumes and no noise,” she says.
Another energy-efficiency measure that Wilsonart now utilizes in its manufacturing process is the cyclomizer, a system highly engineered to fit Wilsonart's specific process in pressing and which employs various components to achieve the desired results. These components include piping, pumps, automated control valves, a large pressure vessel, and electronic logic controls. (The large pressure vessel is the most notable component and is informally referred to as the cyclomizer, but in reality it is the entire sytem that is the cyclomizer.) “This unit stores hot water and allows for its reuse after additional heat is added during the next press load,” says Weadock. “It also stores the cooling water and recools it before the next cycle begins. This equipment not only increases the efficiency of energy use, but it’s a closed-loop system that reuses water over and over.”
Waste Management
Waste is an inherent part of the product-manufacturing process. Yet manufacturers are now utilizing innovative and environmentally conscious ways to dispose of waste products and to extend the life of tools and equipment through refurbishment techniques.
For example, Wilsonart grinds, bags, and sells its laminate scrap to the oil industry as a drilling fluid additive, recycles kraft paper, and spools, reuses, and recycles the paper used in its press plates, and sends its scrap lumber and broken pallets to a local company that either uses or recycles it.
Kolbe & Kolbe Millwork also has an aggressive recycling plan. “We take many materials that may otherwise be disposed of, such as glass, wood, and vinyl scraps, and recycle it as raw material,” says Premeau. “For example, our Ultra Series extruded aluminum billet consists of 50-75% recycled material, our roll-formed clad for Classic and Magnum products contains 65-70% recycled aluminum, our standard glass contains 25-30% recycled content, and we also use recycled content in the manufacturing of some interior doors.”
In addition to using recycled raw materials in its manufacturing process, the recycling and refurbishment of tools is an area of emphasis for Kolbe & Kolbe Millwork. “We have our own in-house maintenance and machine shop, which helps us facilitate this process,” says Premeau. “Recycling, refurbishing, and reusing tools and materials is definitely an expectation rather than an exception for us.”
“We take many materials that may otherwise be disposed of, such as glass, wood, and vinyl scraps, and recycle it as raw material." Lance Premeau, Kolbe & Kolbe Millwork
Refurbishment is also an area of focus for Cambria. Rather than simply discarding tools that may be in need of refurbishing, Cambria has an extensive program for extending the lifespan of its tools. “Each of our diamond-metal tools can be used for approximately 2,000 lineal feet before it requires refurbishment,” says Jim Gallery with Cambria. “Once we reach 2,000 lineal feet, we restore the tool for use on another 2,000 lineal feet. We repeat the process up to seven times, which allows us to reduce waste while stretching the use of our tools much further.”
According to Premeau, in addition to recycling materials and refurbishing tools, Kolbe & Kolbe Millwork also utilizes several other sustainability measures to reduce waste. “We source products locally to reduce transportation costs, we use sophisticated software to help reduce our overall raw material usage, and we use special cutting equipment to help minimize waste,” he says.
Although sustainability techniques and technology will continue to evolve, there is certainly an increased emphasis and expectation emerging within the industry when it comes to sustainable manufacturing practices.
“Managing and minimizing our impact on the environment in both our product offerings and our daily operations is not just an important part of our business, it’s a necessity,” says Gallery. “Our product needs to have a big impact on our customers, not our environment.”
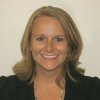
Lisa Taylor Minor
Lisa Taylor is a freelance writer and marketing consultant. She has more than 16 years of experience as a communications professional and has worked with a variety of companies in the home products and building materials industry. Originally from Memphis, TN, Lisa earned a BA in Journalism from the University of Memphis in 1995 and a MA in Journalism from the University of Memphis in 1997. She spent the first 11 years of her career working in account service for Memphis advertising agencies Thompson & Company, Oden Marketing & Design, and Carpenter/Sullivan. Lisa then spent five years in Nashville, TN, with The Buntin Group, an Adweek Top 100 U.S. advertising agency, and Louisiana-Pacific Corporation, a leading manufacturer of building materials. Lisa currently lives in Denver, CO, and is Principal/Owner of Wazee Marketing.
Website: www.wazeemarketing.com