From Pencil and Paper to Computer-Based Cost Estimating
Ted Kokenos is a veteran construction cost estimator. He initiated a transition from pencil and paper cost estimating to computer-based while working for a construction company employing about 60 people. His experience might inspire some construction firms that have been thinking about making the leap to computer estimating to finally go for it!
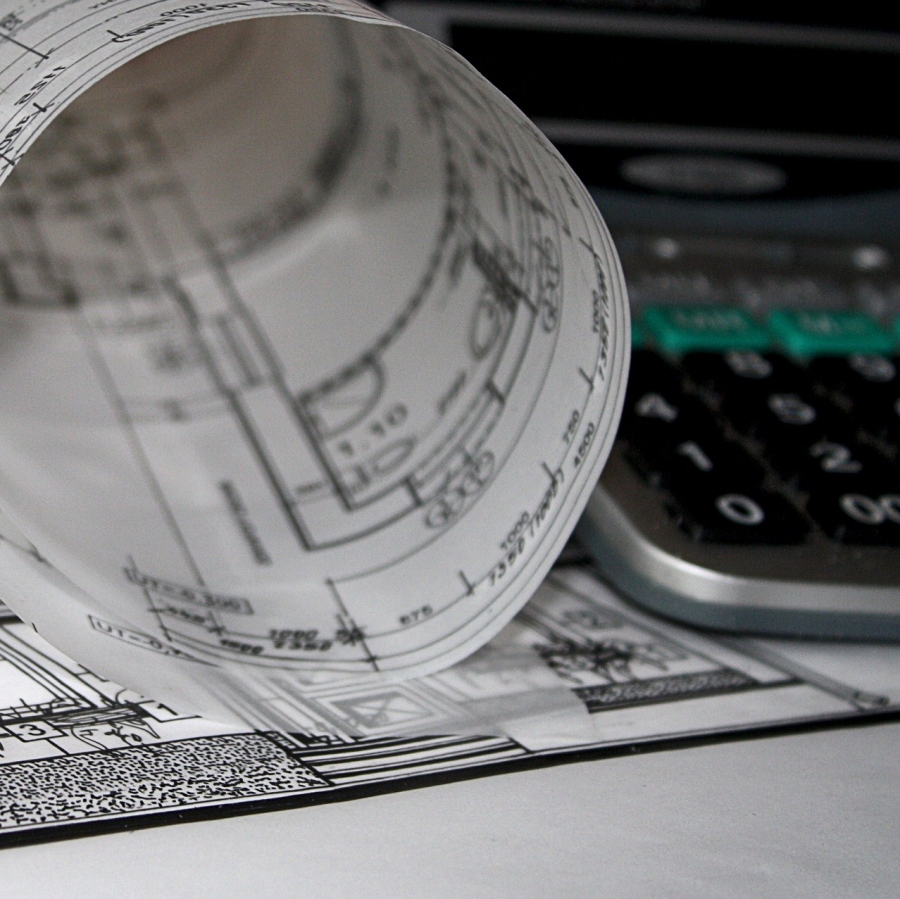
The Old School Method
According to Ted, the typical pencil and paper cost estimating method might go something like this.
- A Project Manager (PM) would receive an Electronic Invitation for Bids (IFB) notice by email.
- The PM would then request an electronic copy of the IFB package’s drawings and specifications, and would forward it along to the Estimating Department.
- Once Ted was assigned a project (from the PM), he would log it into the system as a new estimating project.
- From the client’s electronic files, Ted would print out the drawings and specifications for his own use as well as any other required copies for subcontractors and coworkers. This involved printing out and mailing paper copies.
- Then the actual estimating work would begin. It required taking many measurements while hunched over a drawing set using a Lufkin architectural tape! Ted’s company had a standard Excel spreadsheet they used as an estimating template. The template was effectively a spreadsheet for entering line items representing the Construction Specifications Institute (CSI) format. As Ted measured all takeoffs (determined quantities) using the tape, he would have to then enter them into the appropriate line item within their estimating template, recording all necessary materials and quantities.
- Finally, he would apply the company’s standard overhead and profit values. Once complete the bid would need approval from both his boss, the PM, and the company president.
Tricks of the Trade: Ted would use different colored highlighters during his days of manual estimating. As each item was measured on the drawing and placed in the estimating template, Ted would correspondingly highlight each scope element on the paper drawings. It helped him keep track of what he had already measured, and reduced the likelihood of missing an item and therefore underbidding the job.
Trying Out the New
One day Ted discovered a dust-covered box of estimating software in the office and decided to install it. Once installed, he found that his mouse would replace his architectural tape and the estimating template could be populated automatically at the same time his measurements were made. The estimating software would also make it easier to determine and set the scale of any digital drawing. Drawings and specifications were now able to be received electronically, lessening the need to print multiple paper copies. In fact, his full-sized paper copies were no longer needed to perform the takeoff.
After Ted logged each new project into the system and began his work, he would prepare a new estimating project in the takeoff software. Each project’s new estimating template was prepared from the software’s updateable database of materials and CSI Divisions appropriate for that job. Template line items can also be customized for unique materials and known unique costs instead of using the database’s recommended values.
All the estimating software that Ted is familiar with will perform takeoffs (determine quantities from the drawings) in three modes -- by count, by linear segment/continuous line, or by area.
- By Count: Let’s say the project being estimated requires removing old restroom fixtures and replacing them with Americans with Disabilities Act (ADA) compliant fixtures. The template might be set-up with a line item for “ADA Compliant Sink Fixtures,” which includes all the required plumbing and caulking sub-tasks necessary for each fixture replacement. As the estimator is preparing the estimate, he can simply click the location on a digital drawing where a new ADA compliant sink fixture is required. This leaves an electronic symbol on the digital drawing and populates the estimating template with the proper quantities and line item costs.
- By Linear Segment or Continuous Line: Similar to the measuring tape, mouse clicks can total up the linear segments for such things as Vinyl Composition Tile (VCT) base or trim. The segment lengths captured with each mouse click are transferred and instantly tabulated in the estimating template. Continuous lines can also be selected instead of a line segment for measuring a run of pipe or ductwork.
- By Area: While plan views of digital drawings are only two dimensional, self-tabulating wall area calculations can be performed by entering wall heights into the software’s estimating template. For example, the estimating template might have a line item for “3 - 5/8” Metal Stud/Drywall." Linear wall segments on each drawing may be recorded, but total areas can also be captured if the wall height has been previously entered in the estimating template for that line item.
The Advantages of Computer-Based Estimating
- Consistent Nomenclature: When using the older methods, estimators might have labeled their wall estimate line items as Wall 1, Wall 2, Wall 3, etc. The estimates they prepared required their unique insights for the company to confidently decode line items when changes were needed to an estimate. If an estimator was sick, on vacation, or otherwise not available, the accuracy of the final bid could be compromised. Using the new computer generated estimates ensures consistency of line item nomenclature. A line item might read “3-5/8” Metal Stud Drywall, 10’ High, First Floor West” for a specific project, regardless of who the estimator was. Estimators agreeing on the appropriate descriptions can control this by entering them into the software.
- Quantities Are Easily Verified: There was no need for Ted’s colored highlighters when he used the estimating software. He could read specific floor areas right off the digital drawings. He would then verify that the floor area matches his corresponding floor covering line item. Each unique takeoff item can be color coded for easy reference.
- Faster Takeoffs: As previously mentioned, faster measurements are a huge advantage. Manually transferring careful tape measurements by typing them into a computer spreadsheet after the fact is a tedious process. This also created a substantial opportunity for errors. The estimating software allows the line items to be tabulated as fast as the mouse is clicked.
- Better Accuracy: Another benefit of computer-based takeoffs is the ability to set the drawing scale from a known dimension on the drawing. Scales of 1/4”, 3/8”, and 1/2” to the foot are typical on drawings and the ability to specify scales of all sizes is a standard feature of takeoff software. If you can find a known dimension on the drawing, the scale can be manually set.
Computer Familiarity Is the First Step
In terms of prerequisites, Ted suggests would-be computer estimators simply be computer literate. You don’t want to be learning about computers at the same time you are trying to learn how to use computer-based estimating software. Specifically, Ted suggests familiarity with the structures of various file types like *.tiff’s, *.jpg’s and *.gif’s; a basic understanding of how to manage file folders; how to upload and download files from servers; understanding file paths (ex C:\Documents and Settings\My Documents\ etc); how to use applications menus (views/files/tools, etc); and basic computer mouse skills.
Give It a Try!
In Ted's objective experience, making the switch to computer-based cost estimating is worth the initial overhead investment of software purchase, installation, and self-training. The payback period is short and the computer systems require fewer man-hours, allowing him to prepare more cost estimates for his company in any given timeframe.
Ted Kokenos was a technical contributor to this feature. He is an Akron, Ohio-area construction Cost Estimator and Project Coordinator with over 5 years of related work experience.
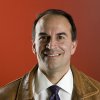
Andrew Kimos
Andrew Kimos completed the civil engineering programs at the U.S. Coast Guard Academy (B.S. 1987) and the University of Illinois (M.S. 1992) and is a registered Professional Engineer in the state of Wisconsin. He served as a design engineer, construction project manager, facilities engineer, and executive leader in the Coast Guard for over 20 years. He worked as a regional airline pilot in the western U.S. before joining the Buildipedia.com team as Operations Channel Producer.
Website: buildipedia.com/channels/operations