Building Automation Systems
It's likely that most Americans got their first glimpse of Building Automation Systems in 1939, when the Wizard of Oz appeared from behind his black curtain, frantically pulling levers to remotely spread smoke, his green visage exposed to Dorothy and her pals. Modern Building Automation Systems (BAS) are different than Oz’s in their focus, technology and desired outcomes, but similar in their concept of centralized remote monitoring and control of mechanical systems.
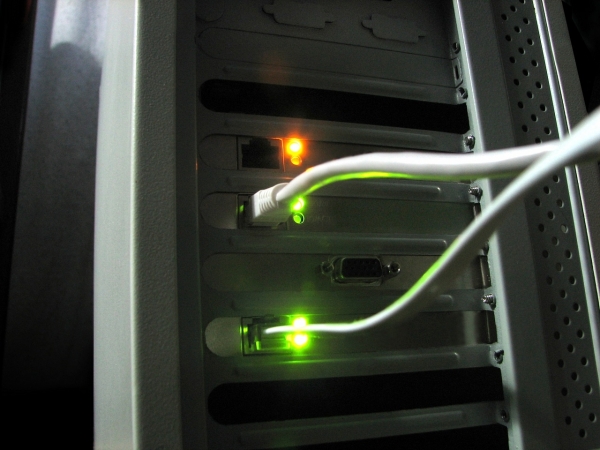
Building Automation Systems (BAS) are also commonly referred to as Building Management Systems (BMS), although some people define BAS as applying only to mechanical/electrical systems, and BMS to further include fire prevention and communications networks such as remote cameras and speakers. Whatever name is used, centralized management of heating, ventilation, air conditioning, lighting, fire detection and alarm, communications, and security systems is now commonly available to, and used by, facilities managers.
A convenient at-home example of BAS would be the programmable thermostat, which can define temperature settings for air conditioning and heating equipment based upon the time of day. Many homeowners are currently using, or can still recall, the old-school thermostats with carefully installed metal coils and mercury switches that start and stop heating and cooling equipment based on one manually set temperature. But more modern digital and programmable thermostats typically allow for varied temperature settings to be implemented according to a weekly calendar and a 24-hour cycle.
Programmable thermostats are a very simple kind of automated system, and cannot provide a full sense of the scope and complexity that it is possible to achieve with BAS. However, household thermostats do illustrate the fundamental principle of BAS and are an example that is familiar to many homeowners.
Basic Concept
Building Automation Systems are composed of an array of mechanical and electrical equipment in a building or on a campus; their valves, switches and/or speed are controlled by installed electrical devices. The devices are connected to a control station, usually a computer, where system oversight can be accomplished by an operator who is trained in its use. A tethered or wireless network connects the control station(s) to the equipment control devices. In more advanced BAS, a control station could be a cell phone or handheld computer which communicates with the device through an internet-capable interface. Overall system conditions are displayed graphically on computer screens or, in more advanced systems, on wall-mounted electronic status boards. Common graphic data will include: equipment that is on vs. off, temperatures within the building spaces, temperatures (air or water) within the mechanical systems, valve positions, and flow rates.
Advance Trend Warnings & Better Customer Service
One big advantage of BAS operated mechanical and electrical systems is early detection of any deviations from standard norms, not only in the building spaces, but also within air handlers and hot/cold water circuits. This means there is no waiting for building customers to call-in maintenance trouble tickets when they’re too hot or cold in a particular space, relative to a desired standard. If there is a call-in situation, then the BAS has not functioned as intended; equipment operating trends can be adjusted before the building occupants notice any substantial temperature deviations in the working spaces. If there’s an unplanned equipment failure that cannot be quickly rectified, savvy BAS operators can predict when the phone calls will start rolling in from dissatisfied building occupants by monitoring the system as various operating parameters are compromised on their status screens.
Saves Money
Tighter temperature controls across daily timeframes result in less energy expenditure and greater savings. For example, if a building is going to be occupied from 8am to 4pm in the wintertime, the heating systems can be warmed up efficiently and start providing heat in the hours before 8am. The BAS might then be programmed to shut down heating beginning at 3:30pm. In the case of electrical systems, photocells and/or occupancy sensors can be used to energize campus lighting systems, in addition to, or separate from, clock-time based scheduling devices.
Saves Time
Cost savings from using BAS come in the form of technicians being sent out to focused areas, where they can quickly and efficiently address root problems. In partnership with Computerized Maintenance Management Systems (CMMS), trouble tickets for mechanical/electrical system adjustments can be generated and closed-out in advance of more significant equipment repairs that would otherwise occur. Like CMMS systems, Building Automation Systems, when properly installed and operated, are an excellent tool for achieving greater efficiencies and cost savings.
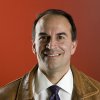
Andrew Kimos
Andrew Kimos completed the civil engineering programs at the U.S. Coast Guard Academy (B.S. 1987) and the University of Illinois (M.S. 1992) and is a registered Professional Engineer in the state of Wisconsin. He served as a design engineer, construction project manager, facilities engineer, and executive leader in the Coast Guard for over 20 years. He worked as a regional airline pilot in the western U.S. before joining the Buildipedia.com team as Operations Channel Producer.
Website: buildipedia.com/channels/operations