Seismic Retrofit Lessons Learned: Contractual and Planning
The project was a seismic retrofit of a 15-story building constructed in 1991. The steel portion of the project consisted of systematically strengthening the moment connections throughout the building and installing over 200 dampers in a 750,000 sq. ft. office building without interrupting the operation of the tenants. The contract dictated that the work would start in the basement, progress through the ground floor and the parking garage (floors 2-5), and then continue through the occupied office floors (6-15). The contractor could only occupy three half floors at any one time and a set number of parking spaces due to contract restrictions. The contract also restricted work hours, noise levels, and delivery times. These restrictions would drive the pace of the work.
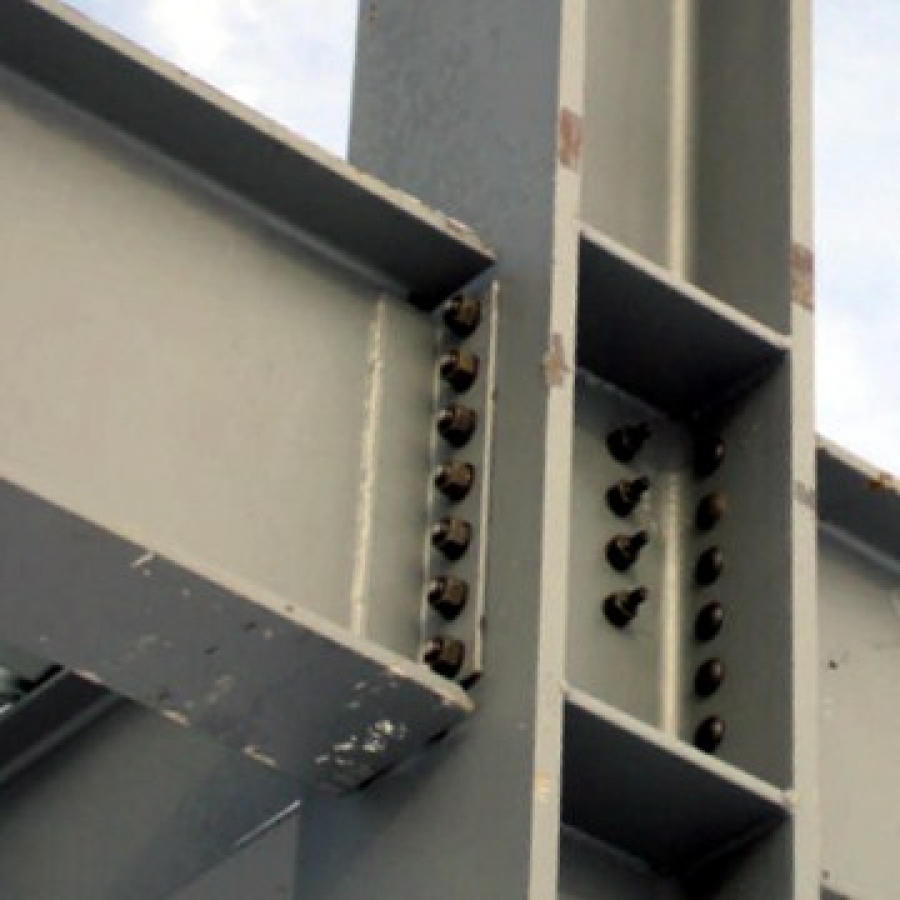
Dealing with Work Hour Restrictions
Work hour restrictions are not uncommon in any construction project and most construction professionals look at this provision of the contract or specifications very carefully. Managers and schedulers need to realize that the production rates of night shift workers are about 75% of day shift workers. Burnout also becomes an issue when working nights or extended hours, but we didn’t have to address this problem because our contract restrictions forced intermittent work. My team did have to address the drop in production while not increasing labor costs. We were able to increase our production by getting the owner to allow us to come in one hour early to hold our safety meeting and to set up our equipment. We carefully constructed our request so that our production work was confined to work hour restrictions in the contract. This allowed us to work one hour before and after the contract work hours. This may seem like an insignificant increase, but two hours of additional welding time meant that work points were completed in 10 days instead of 12. When this two-day per work point difference was evaluated in a time impact analysis, the difference resulted in more than two months of saved project time. To offset the cost of the overtime, the last hour of the day was taken only by the fire watch crew, which had to monitor the work areas to ensure that they were safe.
It’s All in the Details
The burden placed by the restrictions in the contract was difficult to manage but foreseeable. The burden placed by a lack of detail in the design drawings, however, was not as predicable. One detail in the design drawings that did not have a dimension resulted in an issue that was not resolved for more than a year after it was originally addressed and resulted in 20 separate change orders. During that year-long negotiation, we carried over $400,000 in labor and material costs. This single dispute required four separate bulletins and 16 separate WPSs for the excavation and strengthening of the existing moment connections. As insignificant as it may seem, a difference of 1/8 inch on this detail meant a monetary difference of $250,000 across the building. This difference also meant two hours of additional work on each connection.
Managing Expectations
Another unpredictable but preventable burden is often caused by the general contractor. This is not a popular topic, but the general contractor on this job could have reduced the problems we experienced with the tenants by managing the expectations of the client from the award of bid. Although it is very difficult to do, the general contractor needs to manage the expectations of the client and not agree with baseless accusations. This can be extremely difficult when dealing with state workers or other institutional workers who may object to the natural disruption that a construction project brings to any area. The general contractor should prepare the client for the inevitable culture clash that will occur during a prolonged project and should establish rules that apply to both the construction workforce and the tenants. Although rules for the tenants may be a hard sell at the beginning of the project, rules that prevent the tenants from disrupting the construction workforce will enhance the safety, wellness, and productivity of both parties. Just as the general contractor needs to manage the expectations of the client, the subcontractor needs to manage the expectations of the general contractor. I saw the difference this could make firsthand while on this project. Some subcontractors were very giving at the beginning of the project and were bullied, threatened with liquidated damages, and generally ordered around with little dignity. Other subcontractors were very strict about their adherence to the contract, and I am sure that the representative for the general contractor felt that they were difficult to work with. This second group of subcontractors experienced a substantially better relationship toward the end of the job.
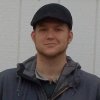
Robert Amstead
Robert is a project manager for a steel erection firm with projects in Northern California, Southern California, and Nevada. His current project types include wind energy, occupied building seismic retrofits, existing bridge seismic retrofits, and new bridge erection. Robert graduated from the University of Missouri Rolla with a Masters in Engineering Management and from the United States Military Academy with a Bachelors Degree in International Relations. Robert has also worked in the luxury residential sector in Florida and as an Officer in the Corps of Engineers.