Eco-Friendly Prefab Homes: Unfold the Possibilities
It has been over a decade since Americans began to embrace the notion of living "smaller." During these years interest has risen in living in a way that is more energy-efficient and eco-friendly. Blu Homes, a company finding success in the prefab home market, is not only addressing our wish to live smaller and greener but is offering a solution to potential home buyers in the wake of the burst housing bubble of 2007. They aim to sell their modular product at an affordable price point.

Blu Homes, based in Waltham, Massachusetts, offers four basic house designs, along with attached or detached building additions. The largest of Blu Homes’ original line of products is sized just under 2,000 sq ft (185.8 sq m). As of 2009, Blu Homes acquired mkDesigns, a line of luxury green homes; this product is available in sizes up to approximately 2,500 sq ft (232.3 sq m). Every Blu Homes house is available with energy systems, water conservation features, and finish materials that can make it LEED-certifiable. The company also works with Energy Star and other green building rating systems. Blu Homes are said to have lower carbon emissions than typical new, energy-compliant homes and to reduce operating costs by up to half.
Blu Homes uses state-of-the-art technologies to design and assemble its structures. Computer modeling is used to adapt each building type to owners’ individual sites in order to optimize passive heating and cooling. The buildings are fabricated using a wood/steel hybrid frame, which gives them exceptional strength and durability. Blu Homes has developed a novel technique of folding the structure for shipment that allows it to be trucked in one piece to the job site then simply unfolded. Furthermore, each building can also be engineered to fit different climate zones and weather conditions, such as hurricane, earthquake, and high snow load areas.
alt=""
The fact that Blu Homes are factory-built in a climate-controlled setting means that they eliminate some of the problems associated with site-built homes, such as water damage and mold growth. They are, however, appraised against site-built homes; manufactured homes are typically built to lower HUD Code standards.
One of the primary objectives of Blu Homes is to reduce the amount of time spent in the construction process. Sitework, done by an on-site contractor who works directly with Blu Homes, usually takes about one month, depending on variables such as whether a basement is to be built. During that time, the home is being assembled at the factory; assembly is expected to take at most eight weeks. Once the home is delivered to the site, it can be put up in a single day and have its interiors finished in two weeks. (On-site contractors then add exterior finishes.)
As prefabricated homes such as Blu Homes become better designed, both functionally and aesthetically, they should continue to gain market share. To check out Blu Homes designs in person, see if one of their seminars and/or home tours is available in your area.
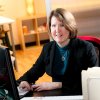
Kristin Dispenza
Kristin graduated from The Ohio State University in 1988 with a B.S. in architecture and a minor in English literature. Afterward, she moved to Seattle, Washington, and began to work as a freelance design journalist, having regular assignments with Seattle’s Daily Journal of Commerce.
After returning to Ohio in 1995, her freelance activities expanded to include writing for trade publications and websites, as well as other forms of electronic media. In 2011, Kristin became the managing editor for Buildipedia.com.
Kristin has been a features writer for Buildipedia.com since January 2010. Some of her articles include: