Loose-Fill Insulation
Loose-fill insulation consists of small particles of fiber, foam, or other materials. These small particles form an insulation material that can conform to any space without disturbing any structures or finishes. This ability to conform makes loose-fill insulation well suited for retrofits and for places where it's difficult to install some other types of insulation.
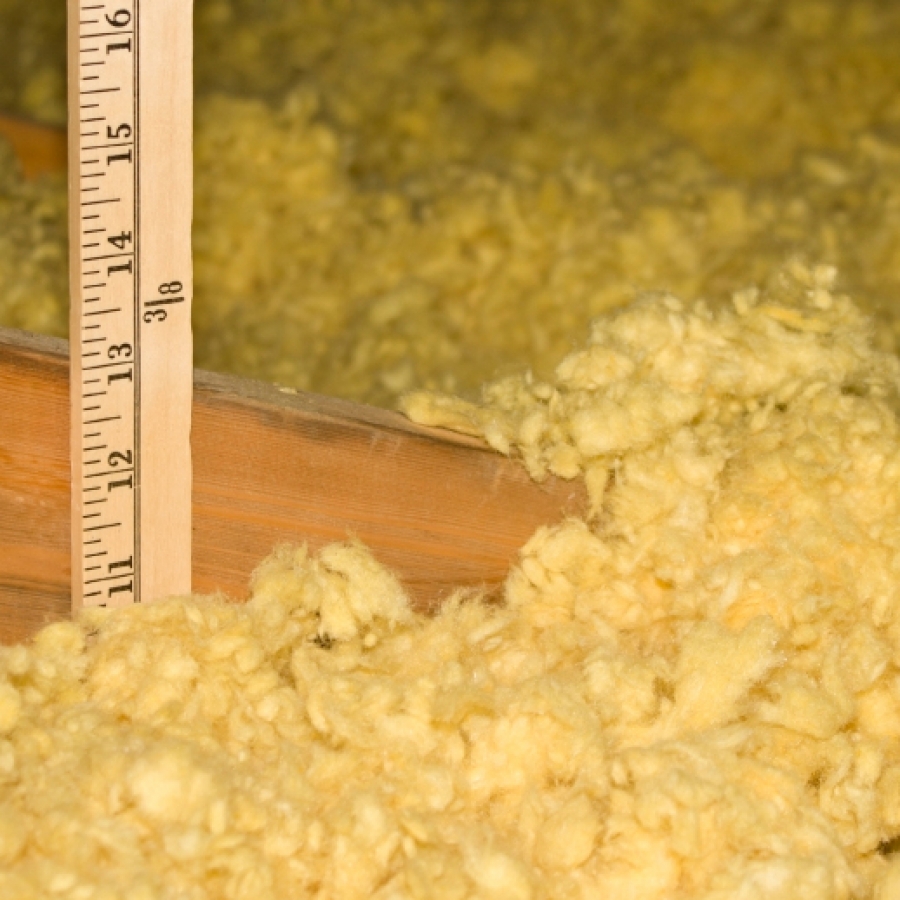
Topic Summary
Types of Loose-Fill Insulation
The most common types of materials used for loose-fill insulation include cellulose, fiberglass, and mineral (rock or slag) wool. All of these materials are produced using recycled waste materials. Cellulose is primarily made from recycled newsprint. Most fiberglass contains 20%–30% recycled glass. Mineral wool is usually produced from 75% post-industrial recycled content. See the table below to learn how they compare.
Recommended Specifications by Loose-Fill Insulation Type |
|||
Cellulose | Fiberglass | Rock Wool | |
R-value/inch | 3.2–3.8 | 2.2–2.7 | 3.0–3.3 |
Inches (cm) needed for R-38 | 10–12 (25–30) | 14–17 (35–43) | 11.5–13 (29–33) |
Density in lb/ft3 (kg/m3) | 1.5–2.0 (24–36) | 0.5–1.0 (10–14) | 1.7 (27) |
Weight at R-38 in lb/ft2 (kg/m2) | 1.25–2.0 (6–10) | 0.5–1.2 (3–6) | 1.6–1.8 (8–9) |
OK for 1/2" drywall, 24" on center? | No | Yes | No |
OK for 1/2" drywall, 16" on center? | Yes | Yes | Yes |
OK for 5/8" drywall, 24" on center? | Yes | Yes | Yes |
Some less common types of loose-fill insulation include polystyrene beads and vermiculite and perlite.
Installation
Loose-fill insulation can be installed in either enclosed cavities, such as walls, or unenclosed spaces, such as attics. Installation usually involves using special equipment that blows the insulation through and into the cavity or space. This includes the "two-hole method," which entails drilling two holes spaced vertically between the exterior walls' framing studs. The holes should be 2 inches (5 centimeters) in diameter. Working between each stud, drill one hole 16 inches (41 centimeters) from the top of the wall. Drill the other hole 24 inches (61 centimeters) from the bottom of the wall. Blow the insulation into the holes and then seal the installation holes. In conventional and cathedral ceilings, insulation is easier to blow in if an access opening through the ceiling already exists. Otherwise, it may be necessary to drill holes in the ceiling or between the roof rafters.
Installation is most commonly done by professionals who are experienced at operating the equipment to ensure proper density and complete coverage. If you'd like to have the insulation installed professionally, you should do the following:
- Obtain written cost estimates from several contractors for the R-value you need. Don't be surprised to find quoted prices for a given R-value installation to vary by more than a factor of two.
- Ask contractors about their air-sealing services and costs as well, if needed.
If you want to install it yourself, you should try to obtain instructions and safety precautions from the insulation manufacturer. Carefully follow these instructions. You should also check your local building and fire codes.
Settling
Over time, loose-fill insulation can lose its installed R-value because of settling, especially in attic cavities. Cellulose settles more than rock wool or fiberglass—20% compared to 2%–4%. Therefore, if you use cellulose, install 20% more in an attic to offset the settling. Cellulose manufacturers are required by federal law to provide the "settled thickness" on their bags. Some even provide the "installed thickness."
Researchers say it's possible to install loose-fill insulations in wall cavities without settling. If the cavity is completely filled with insulation at the proper density, no significant settling should occur. A general density guideline for walls is roughly 3.5 pounds per cubic foot (17 kilograms per cubic meter) of wall cavity for cellulose and 1.5 pounds per cubic foot (7 kilograms per cubic meter) for fiberglass or rock wool. These specifications are roughly twice the density of horizontal applications.
Here's an easy-to-follow guideline to ensure that wall cavities are being filled at a density sufficient to prevent settling: use roughly one 30-pound (13-kilogram) bag of cellulose or about 15 pounds (8 kilograms) of fiberglass or rock wool for every three wall cavities you fill. (Assumptions: 8-foot [2.4-meter] walls, with 16-inch [41-centimeter] on-center wall cavities, and 2x4-inch framing studs.)
Quality Assurance
To ensure quality installation, whether you hire a professional or do it yourself, you should also look for voids and gaps, and fluffing.
Voids and gaps occur if insulation is installed at too low a density or if a cavity isn't completely filled. Voids also occur if the installation holes are improperly located between the vertical framing studs or if there are too few fill holes.
Fluffing occurs when insulation is installed to minimum thickness but not to minimum weight requirements. The result is a less dense application of insulation that requires fewer bags. When insulation is fluffed, air passes more easily through it. This means increased heat loss. Additionally, the fluffed loose-fill insulation will eventually settle, resulting in a loss in thermal resistance or R-value. Fiberglass is more "fluffable" than cellulose or rock wool.
Intentional fluffing by unscrupulous contractors has been a problem in some parts of the country. To avoid these problems, compare bids from several contractors to see how many bags they specify. Count the number of bags used during installation, either by you or a contractor, and compare it to the instructions on the bag. The manufacturer should specify the amount of insulation required to obtain a particular R-value per square foot (or square meter) of space.
Safety and Health Considerations
Insulation blown into your ceiling cavities should cover the top plate of the wall, but be sure the eave vents are not covered. These vents provide necessary ventilation to your attic, and covering them could result in severe moisture problems.
Electrical devices and recessed lights (except "IC-rated" fixtures) require 3 inches (8 centimeters) of clearance from insulation.
Pipes for kitchen stoves, wood stoves, and furnaces should only be insulated with fiberglass or rock wool because cellulose may smolder if flue temperatures become hot enough.
Some observers contend that fiberglass particles can cause cancer if inhaled. Others state that the fire retardants and insecticides added to cellulose may be harmful to breathe. While the debate continues as to the health effects of loose-fill insulations, it is important to protect yourself when installing any type of insulation. Wear a quality respirator, protective eyewear, and clothing such as goggles, gloves, long-sleeved shirts, and pants to minimize contact with the insulation.
Insulation fibers can also be drawn into air distribution systems if the ducts are not properly sealed, allowing the fibers to circulate within the living space. Be sure to seal all of your home's ductwork, as well as any other openings where insulation could leak out of the wall or ceiling cavities and into your living space.
Article source: The U.S. Department of Energy’s Office of Energy Efficiency and Renewable Energy (EERE). For the most up-to-date information please visit the EERE website.