Hydraulic Elevators
Hydraulic Elevators are prevalent in multi-level structures throughout the world. They facilitate and control the flow of people, make the movement of equipment easier, and allow disabled persons access to upper-level floors. Elevators in use today fall into three general categories: hydraulic, electric traction, and Machine Room-Less (MRL). The hoisting mechanisms to lift the cars of elevators generally employ either hydraulics or wire-rope traction systems. The principle of hydraulics is based on Pascal’s law of the incompressibility of fluids: any change in pressure applied at any point in the fluid is transmitted undiminished throughout. This pressurized fluid is used for the generation, control, and transmission of power.
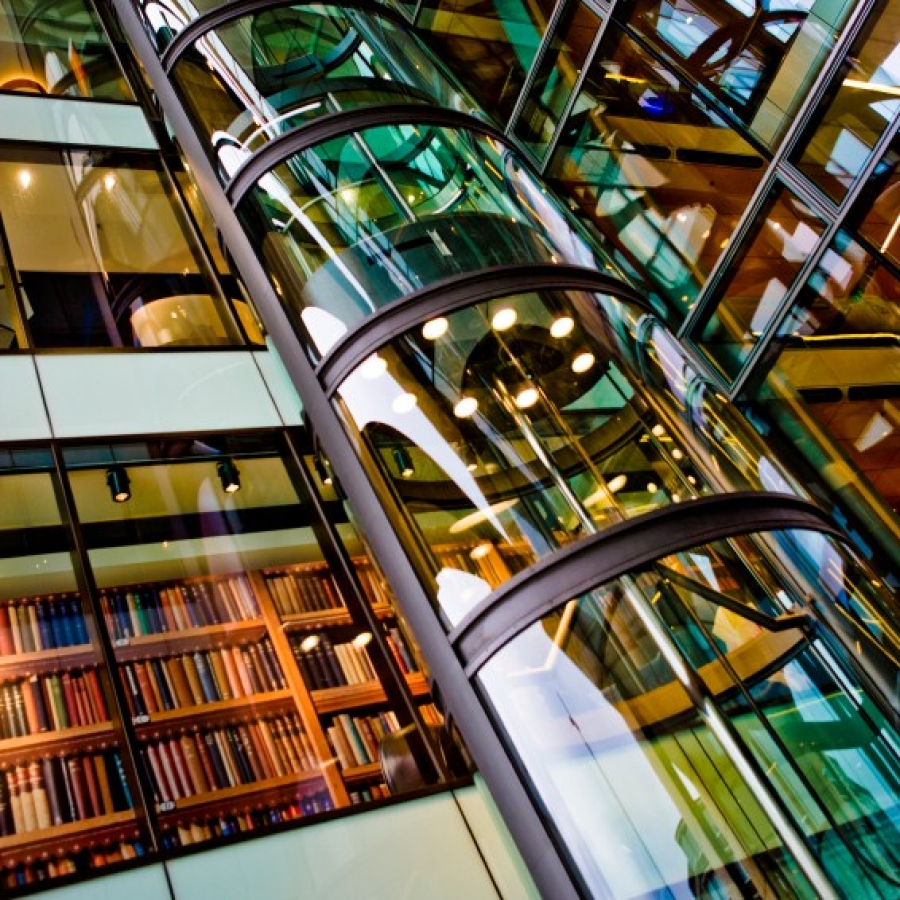
Hydraulic Elevator Background
In the early 19th century, hydraulic plunger elevators were used in some European factories. The car was mounted on top of a steel plunger that dropped into a cylinder buried in the ground. Water was forced into the cylinder under pressure which raised the plunger and car. When water was released in a controlled manner the car would descend. In early installations, the main valve controlling the flow of water was operated by the passenger by means of ropes running vertically through the car. Later improvements on this system led to lever control and pilot valves that could regulate acceleration and deceleration. The use of hydraulics to power machines began in the mid 1840’s, when Sir William Armstrong introduced the hydraulic crane. Then, by the early 1870's, hydraulic machines began to replace steam-powered ones. Later in the 1870’s, the rope-geared hydraulic elevator was introduced. The plunger was replaced by a relatively short piston, which moved in a cylinder that was mounted within the building. With this system, the effective length of the piston stroke was enhanced by a system of ropes and pulleys (sheaves).
Hydraulic Elevator Specifications
Hydraulic elevators are typically efficient up to five or six floors with a typical speed of up to 150 feet per minute (fpm) if powered by a piston. There are three types of hydraulic elevators: in-ground, hole-less, and roped systems. All hydraulic systems consist of four major components: a tank (fluid reservoir for oil); a pump that is powered by an electric motor; a valve between the cylinder and the reservoir; and a cylinder. With each of these systems, a pit at the bottom of the elevator shaft is required. The depth of the pit (located below the floor of the lowest landing) will typically be 4'-0". Upward movement is created by the electric motor pumping oil into the cylinder, causing the piston to lift the elevator cab. To descend, the valve simply lets the oil out of the cylinder, back into the oil tank. The weight capacities of hydraulic elevators are dependent on the size of the car and will range from 2,000 pounds for passenger cars to 5,000 pounds for service elevators.
Hydraulic Elevator Pros
- No overhead machine room is required
- Elevator hoist-way dimensions are minimized
- Elevator loads are distributed to load bearing walls
- Machine rooms can be located remotely
- Installation costs are typically less than with other elevator system
Hydraulic Elevator Cons
- A machine room is required for pump unit and other control components
- Limited speed and performance
- Higher noise levels caused by the pump and hydraulics
- Environmental concerns of hydraulic oil leaking into the ground
- Quality of ride less than that of other systems
Types of Hydraulic Elevators
- In-ground, or holed hydraulic systems, as they are sometimes referred to, require the cylinder to extend into the ground below the elevator to a depth which equals the height of the highest floor to which the elevator will travel. The bottom of the elevator car is mounted on a piston that travels inside the cylinder. Soil borings at the project site will determine if there are any obstacles, such as a high water table, bedrock, or unstable soil conditions, which would prevent the cylinder from being installed. This can often be a significant drawback to an in-ground hydraulic system.
- With a hole-less system, a hole is not required to be dug for the hydraulic cylinder. This system is used when drilling a hole for the cylinder is not possible due to a high water table or other limitations. The elevator cab is raised by a pair of above-ground telescoping cylinders located under each side of the cab and secured to the concrete floor in the pit. Oil leakage into the ground through electrolysis is eliminated because the hydraulics are mounted directly on the floor of a self-contained pit.
- Roped hydraulics use a combination of both ropes and hydraulic power to raise and lower elevator cars. Instead of connecting the plunger(s) directly to the car frame, they are coupled indirectly to the car frame by a rope and sheave arrangement to support the car and its load. An advantage to this roping system is that it produces a 2:1 ratio of car movement to jack movement, which allows the use of a shorter jack or, alternatively, a greater range of car travel.
See also: Elevator Controls, Mitigating Elevator Noise in Multifamily Residential Buildings, Smoke Migration In Elevator Shafts
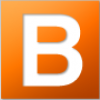
Buildipedia Staff
The Buildipedia research and writing staff consists of dozens of experienced professionals from many sectors of the industry, including architects, designers, contractors, and engineers.
Website: buildipedia.com/