Predictive vs. Preventive Maintenance Concepts
The traditional concept of “preventive maintenance” applies to maintenance on a piece of machinery based on its quantifiable use, or the passage of a set amount of time. A good common example of preventive maintenance is changing the engine oil in your car every 3,000 miles or 3 months, as many automobile owners’ manuals may suggest. “Predictive maintenance” is an attempt to refine maintenance activities to only those times when they are functionally necessary, based on data collection, analysis, and (negative) trend determination from an established “healthy” base level.
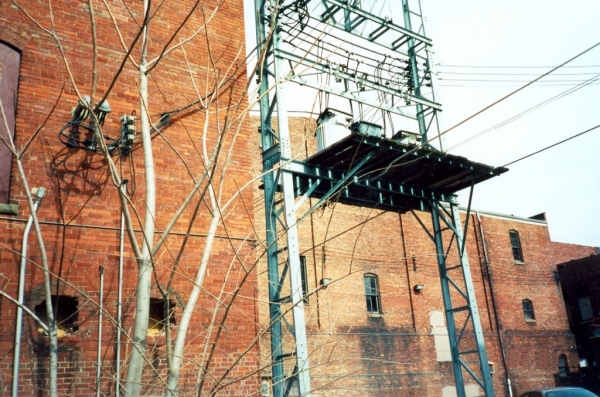
To continue with the automobile analogy, if predictive maintenance philosophies were employed for your car’s oil change routine, perhaps you’d monitor the oil’s pH level, water content, or look for evidence of trace metals present. Then, you would initiate an oil change and new filter (or a recurring engine overhaul) when routine sampling and lab results trended toward an unacceptable range. For most personal vehicle applications, predictive maintenance strategies like these are not cost effective; that is why mileage and age-based preventive maintenance programs are more prevalent for cars. I’m sure in the realm of common automobile engines, the 3,000 or 3 months standard (or something similar for a particular make & model) proved to mitigate most wear issues well before significant deleterious effects began. Additionally, purchasing a new commuter car is typically preferred to over-hauling an engine on an existing vehicle. This is not the case with large industrial vehicles and capital mechanical equipment that may undergo routine major engine repairs.
Predictive maintenance becomes more preferable as the cost of required maintenance actions (and the initial cost of the equipment being maintained) increases. Initiating expensive maintenance routines without good reason, or putting high-cost equipment at risk or at idle, are poor and potentially expensive facilities maintenance pitfalls. A great variety of mechanical and electrical equipment found throughout typical facilities are proven candidates for a predictive maintenance program, including steam lines, chilled-water generators, electrical generators, transformers, and electrical switch-gear, just to name a few. Not to be forgotten are building roofs, which lend themselves well to thermal imaging, as we’ll discuss in a minute.
The categories of predictive field measurements on mechanical and electrical equipment that facilitate trending include vibration analysis, thermal imaging, and ultra-sonic testing (and engine oil analysis, as was just mentioned), among others. The real-world applications for these common categories of predictive maintenance data are too numerous to list. However, the general principles of each category can be readily described.
Vibration Analysis
Any rotating piece of machinery, particularly one that goes through millions of revolutions during its service life, will create consistent vibrations in a repeatable pattern that can be measured. Anyone trying to entice babies into a numbing slumber understands this notion of “good vibrations.” Once a drive shaft, bearings, gear, or other part of a rotating drive assembly starts to wear before its point of replacement, minute changes in the vibration pattern throughout the equipment will occur. Taking vibration measurements at the proper locations, at recommended intervals particular to that equipment, will result in accurate trends to predicate required maintenance actions, such as bearing replacements. Of course, when, where, and how to conduct the vibration analysis and maintenance actions are all equipment specific, based on manufacturers' recommendations, or industry best practices. Additionally, proper diagnostic equipment and training are essential for good results, as with any of these predictive maintenance technologies.
Thermal Imaging
Thermal imaging is based on the general notion that too much heat signals pending troubles. Infra-red scanners in various forms, hand-held through aircraft-mounted, can help facilities managers identify the presence of excessive heat which might not otherwise be visually evident. One example occurs at the cable connections wired into a piece of electrical switchgear or a transformer. There may be a hot spot within the equipment, indicating damage to the cables or a loose connection. Electrons that are flowing through a tighter conductor cross-section than usual, as would occur with a damaged cable, or a loose connection, create excessive heat. This situation would not be obvious during a routine visual inspection until an outright failure occurred.
Over-flying a facility with airborne thermal imaging equipment is a great way to identify steam leaks in buried utility lines, and areas of building roofs that require re-insulation. (Here ’m skipping ahead as a small preview to our aerial engineering services piece!) As an entertaining aside, law enforcement agencies in the past have used this equipment to determine who might be growing marijuana in their attic. As they overfly neighborhoods with thermal imaging equipment, rows of heat lamps in a grower’s attic appear as spotted roof patterns on thermal imaging equipment. A similar concept applies to the roofs of more law-abiding facilities, as locations of poor roof insulation will appear as random “hot spots” of various sizes and locations on the thermal imager. Conversely, areas of problematic wet insulation may appear much colder on the imager.
Ultra-Sonic Detection
Just as the infra-red light spectrum cannot readily be seen by humans, nor can the ultra-sonic spectrum readily be heard. Ultra-sonic detection equipment is perfect for evaluating utility systems with a pressurized flow of gas, i.e. industrial compressed air systems used for pneumatic tools. Escaping gasses from tiny leaks make high-frequency noises, which can be identified and corrected before they become greater issues.
There are many more predictive maintenance technologies available to savvy facilities managers than these few highlights. They all have the same goal of conducting maintenance and repair actions at the most cost-effective time. As with most things in facilities management, the investment, training, use, and maintenance costs of any diagnostic testing equipment needs to be compared with the assumed maintenance cost savings, before embarking on a predictive maintenance program.
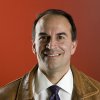
Andrew Kimos
Andrew Kimos completed the civil engineering programs at the U.S. Coast Guard Academy (B.S. 1987) and the University of Illinois (M.S. 1992) and is a registered Professional Engineer in the state of Wisconsin. He served as a design engineer, construction project manager, facilities engineer, and executive leader in the Coast Guard for over 20 years. He worked as a regional airline pilot in the western U.S. before joining the Buildipedia.com team as Operations Channel Producer.
Website: buildipedia.com/channels/operations