Building Maintenance Systems: The AEC End of the Equation
AEC professionals have the opportunity to pass along valuable information to their clients, and to a building’s future maintenance manager. The information sharing and storage capacity of BIM can be leveraged to help architects, system designers, and installers deliver a more complete product than was ever before possible.

BIM for Maintenance
Ask anyone who’s had to do it. Getting asset information into a maintenance system just ain’t fun.
In a typical building, you have multiple systems – mechanical, electrical, plumbing and fire protection – each with dozens of critical components that need to be tracked and managed to make the building run safely, sustainably and cost-effectively. Don’t even mention all the related components, meters, and parts that you need to track! At the end of the day, an average building has thousands of pieces of equipment that facility professionals need to track and manage.
The good news is that, somewhere in the process of designing the systems, building the building, and fabricating or installing the products, AEC professionals have created or gathered the information that operations and maintenance managers need. So what’s the bad news? In traditional workflows, that information gets lost or dumbed-down to paper (at worst) or electronic documents (at best) before it finds its way into the hands of the building maintenance team. Either way, maintenance systems need data as well as documents to do their job. Getting that data into their system sends maintenance professionals on a time-consuming and frustrating document chase that only ends up with a data entry nightmare.
BIM-based tools and workflows have the potential to make this challenge a thing of the past.
The business case for better maintenance
As discussed in the article for BIM-based space management, AEC professionals know building owners commit significant capital to new construction and major projects. However, the first costs of a building are only a fraction of the lifecycle cost for the property. According to the International Journal of Facility Management, design and construction costs account for just 5-10% of the full lifecycle cost of a building. What’s more, real estate and facilities costs typically represent the second largest expense for most organizations (behind personnel).
For an average office building of about 400,000 RSF, operation costs (operation, janitorial, maintenance, and utilities) run about $6.54/sf per year. Assuming the building stays in operation for 40 years, that adds up to roughly $105 million for the life of the building! Maintenance management systems have proven their value in extending the life of a building and reducing the cost of maintenance, but the cost and pain involved in populating maintenance systems often results in limited deployment of the system.
It’s all too common that maintenance managers don’t track all their equipment, or they have inadequate data to properly manage equipment that they are tracking. For example, one facility executive said that he typically receives the building information three months after occupancy. Even then, because the information he needs is locked up in paper or digital documents, it takes his team up to a year to get all the information into his CMMS system. That’s 12-15 months – and potentially voided warranties due to missed maintenance requirements. With a BIM-enabled CMMS system, maintenance managers can get the critical data they need about the building assets before occupancy.
With detailed information about the building systems and assets, maintenance planners can maximize the useful life of building equipment, take full advantage of building and equipment warranties, and avoid costly and disruptive system outages. Even if a system needs to be completely retrofitted, good information about the system and the building can help reduce the cost of system redesign and installation.
Building BIM models for maintenance savings
How can you, as the architect, and your BIM models help? First and foremost, it’s critical that you understand the basic requirements of maintenance management systems. Knowing your customers’ policies and processes for tracking equipment will help you create BIM models that will save your customers time, money and frustration.
There are a number of ways that you can model equipment to support operations and maintenance:
Asset Attributes and Data: The information needs of maintenance professionals are different from the information needs of design engineers. Engineers designing a system typically are concerned with the operating characteristics of the equipment and the overall performance of the building systems. For example, an engineer will model an air handler with certain air flow or other performance characteristics, but a maintenance professional also needs to know the product manufacturer, model number, installation date, warranty expiration date and recommended maintenance schedules. Work with your clients to understand what systems and equipment they need to track and the key attributes for each type of equipment.
Links to Related Documents: Almost every piece of equipment has a library of documents associated with it. While providing only the documents doesn’t address the handover problem, these documents are still important reference points for O&M professionals. Many documents such as installation manuals, specifications, and operating guides are easily available via the Web. By adding Web links to these critical documents, both you and your clients will be able to easily find and access any necessary details. In this way, your BIM model becomes a hub of information that connects to a wide range of information.
Asset Classification: Maintenance planners classify assets to categorize different types of building systems and pieces of equipment; this streamlines the management of equipment and tracking of asset inventories. The OmniClass product classification is an emerging standard for categorizing and managing building products. Most BIM model families provided by product manufacturers will have OmniClass values already. If you are modeling mechanical equipment or other types of assets, be sure to define the OmniClass number for your families.
Equipment Naming Standards: If you want to make the handoff process truly seamless, work with the building owner to understand their asset classification and tagging standards. By adopting the client’s standards earlier in the process, information from a wide range of systems can be more readily joined together and, ultimately, the information in your models will be easier to integrate with their existing data.
As you can see, detailed MEP models of a building can play a key role in helping maintenance planners track and maintain critical building equipment. As a BIM specialist, you can help by making sure that you’re modeling that equipment to properly capture every asset in the building. Start today! Talk to your clients and learn how your firm can use BIM to help support building operations and drive down maintenance costs.
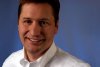
Marty Chobot
As VP of Product Management and Strategic Alliances, Marty helps FM:Systems better understand the needs of its customers and bring new products to market. Marty’s current focus is the convergence of BIM and the operation of sustainable, cost-efficient buildings. Key activities include leading the FM-BIM Working Group and conducting customer and market research on the application of BIM models and data in the operational phase of the building lifecycle.