BIM Strategies: Product Manufacturers Play a Role in Eradicating Project Waste
Video
For decades, the commercial construction industry has been trying to get rid of waste and information loss during the design, construction, and operations processes.
The enormity of this challenge is recognized in the 2012 SmartMarket Report: The Business Value of BIM in North America, which emphasized the usefulness of having building product manufacturers provide Building Information Modeling (BIM) content for the project delivery sequence. As the SmartMarket Report states, “More building product manufacturers providing specific content was ranked fifth in the 2012 report as being of significant benefit to BIM.”
Clearly, change is needed to meet these challenges, and it is now happening with the adoption of BIM and other methodologies that embrace Integrated Project Delivery (IPD). With these tools, the construction industry finally has a way to help designers, building products manufacturers, contractors, and owners work together from the start of a project to build better-performing structures on time and on budget and to exchange project information directly with operations and maintenance. Integrated Project Delivery makes it possible to achieve lower overall costs throughout a building’s life cycle.
Data-Rich Building Product Components Play a Role in Reducing Project Waste
The building industry spends a tremendous amount of money – billions of dollars per year, in fact – making products that don’t “fit” into the design of a specific project. During the project, substitutions may be made without the benefit of knowing why a certain product was built into the design in the first place. Having a relevant, building-product-specific model can help.
Furthermore, the budding collaborative spirit in the building industry is now extending into product life cycle management for building product manufacturers, as well. Manufacturers that want to be regarded as stakeholders in commercial building projects (rather than simply as product vendors) are beginning to adopt systems that harvest data for manufactured components.
It is feasible to imagine other uses for manufactured component data, too. Building product manufacturers are streamlining their processes to knit together potential sales on projects, initiate purchase orders, trigger events for manufacturing, distribute concepts to the supply chain, verify that distribution shipments are on time, and to ensure that materials are packaged and distributed to installation teams armed with the right tools and resources at the right time.
Embedded Component Information Benefits Designers in Justifying Product Selections
Although it makes perfect sense that owners want to reduce costs, substituting a lower-cost alternative doesn’t always translate to a true cost savings. The building’s design team carefully selects building products based on performance, safety, fit, color, and overall building objectives. When a lower-cost alternative is suggested by the contractor or owner to save money, the architect must validate and accept it, including assuming the professional liability and risk if the product compromises design. For example, the substituted product may meet the criteria for design, safety, and performance, but it may not physically fit with other systems or it may not fit with the color and design theme. Forcing a fit can create a domino effect that requires a redesign of other components or other substitutions, stalling the construction process. In the end, the material cost-savings are often negated by the ensuing extra work that has to be done to make the substitution fit.
When detailed component information about the building product in question is embedded in the BIM, the manufacturer can exhibit the product’s value in connecting to the broader building system and communicate how it fulfills the building’s programmatic objectives such as sustainability, energy use, aesthetics, and performance. Having this information intrinsically tied to the building design gives the owner a greater understanding of why a product was chosen; it also gives the architectural designer the power to say “yes” or “no” to a substitution with a greater level of authority, thereby reducing waste and eliminating substitution wars. Moreover, embedding component information has the potential to move the industry away from the practice of value engineering.
Having building product components designed into the BIM benefits the whole team as well as the manufacturer. Sharing common and consistent information through the Specifiers’ Properties Information Exchange (SPie) project and the Construction Operations Building Information Exchange (COBie) early during design will eliminate information loss and waste, keep the team and manufacturers aware of decisions, and keep BIM reconciled with product data to enable better decision-making.
Although embedding data in BIM components is not new, this theme can be expanded to reach other stakeholders in the decision-making process. To that point, extending those data into the supply chain is revolutionary. As designers author BIM, they will use and insert libraries of components. These components provide detailed information about selected products – including the name, model, and specifications as well as performance, installation, maintenance, and replacement information –providing the entire project team with essential information throughout the project’s life cycle.
The building industry is indeed changing, despite being steeped in tradition and typically resistant to doing things differently. Architects, contractors, and owners are adopting BIM and beginning to embrace Integrated Project Delivery (IPD), which in turn challenges the industry – including the building products manufacturer—to consider new, more productive ways to take a holistic approach to design, streamline the manufacturing supply chain, link construction and installation processes to reduce waste, and, ultimately, facilitate operations and maintenance strategies for high-performing buildings.
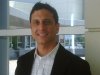
Michael Ruiz
Michael Ruiz is vice president of BIM Strategies for Atlanta-based Applied Software, the largest Authorized Autodesk Reseller in the Southeastern United States and one of the nation’s leading providers of BIM services including BIM modeling, analysis, training, integration and mentoring. He can be reached at mailto:mruiz@asti.com.