Construction of the Vancouver Convention Centre's Habitat Skirt
The Vancouver Convention Centre, which was featured on the Go Green channel as a case study in April, has an extremely unique design feature – an artificial reef (also referred to as a “habitat skirt”). The concrete habitat skirt steps down in five tiers from the underside of the public walkway into the harbor. The skirt was designed with input from marine biologists and other consultants to make it mimic a natural environment.
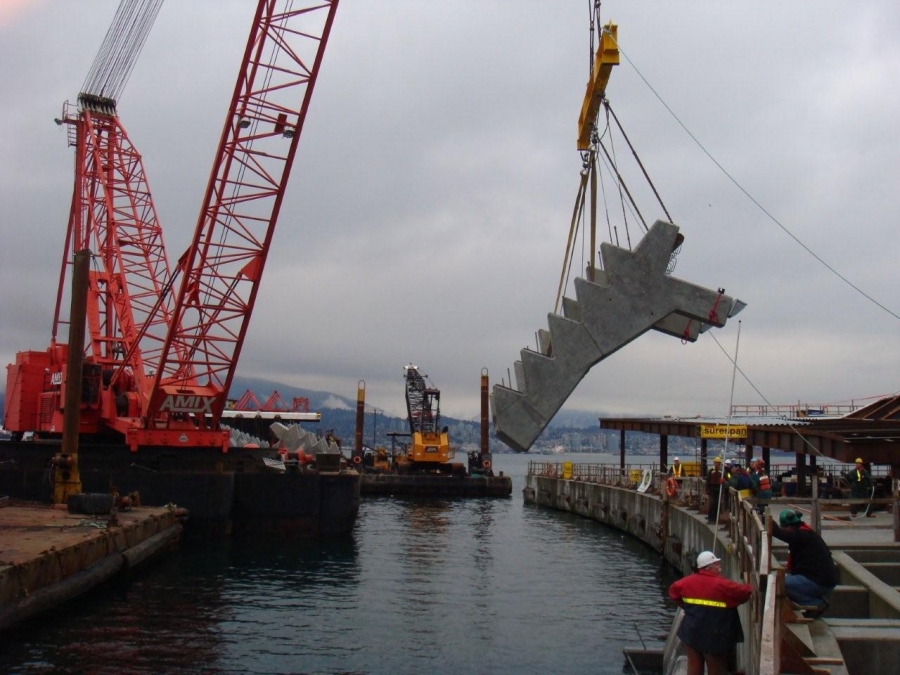
Below are a few excerpts from an award submission primarily focusing on the design process, fabrication, and installation of the habitat skirt courtesy of WorleyParsons Canada Ltd. Refer to the attached fact sheet for design specifications, materials used, project costs, and project timeline, also courtesy of WorleyParsons Canada Ltd.
This submission is specifically focused on the design, fabrication, and installation of the “fish habitat skirt,” or habitat skirt, which was completed in May 2008 for US $8.3 million. The three offshore perimeter faces of the facility have been skirted by this bioengineered structure consisting of a series of stepped, precast concrete benches supported by precast concrete frames that are attached to a specially designed cast-in-place concrete beam. Extending outwards from the facility and downwards over the entire 17 foot tidal range, the habitat skirt is designed to maximize vertical and horizontal ecological connectivity that will create habitat for a diverse mix of intertidal marine life.
Design Process
When deciding on the most appropriate materials to realize the objectives of the habitat skirt, the structural engineers chose to use precast concrete components for several reasons. First, the frames and benches are located in the tidal zone and are exposed to wave forces and impacts from floating debris such as logs. Concrete, due to its mass, is more resistant to upward wave slamming forces and denting from impacts than other materials. Second, the habitat skirt must facilitate rapid colonization of a wide diversity of marine life by providing ideal growing conditions. Exposed aggregate concrete surfaces can best replicate the conditions found on a natural shoreline and the surfaces will not rot or deteriorate over time. Finally, the habitat skirt frames are attached to a cast-in-place concrete foundation structure with typical construction tolerances. By using projecting steel reinforcing bars and shear key ways, the precast concrete frames have been completely locked into the foundation structure by a cast-in-place infill section that was able to accommodate large deviations in the geometry of the foundation while still maintaining the alignment and aesthetics of the habitat skirt frames.
The habitat skirt frames have a unique geometry and connection requirements that prevented the incorporation of either pre-stressing strands or post-tensioning bars. Instead, the frame legs, which will resist both tension and bending forces, are heavily reinforced with regular deformed steel bars to limit the width of any concrete cracks and prevent corrosion.
The habitat skirt benches are pre-stressed with wire strands to further limit concrete crack widths. In addition, several features were added to the top surface of the benches to promote marine growth. A continuous depression, or trough, was placed in each bench so that as the sea level lowers with the tide water will remain in the benches to form tidal pools. The rest of the top surfaces are corrugated and finished to expose the aggregate within the concrete.
In order to extend the serviceable life of the structure and add to the sustainability goals of the overall project, a concrete mix design that has low permeability and contains approximately 25% fly ash was specified.
Finally, special attention was directed towards ensuring that the structural system could be easily installed to reduce project costs and minimize risks to worker safety. To that end, temporary erection hooks were designed to support the habitat skirt frames on the foundation so that the frames could be clipped on to the foundation and held in place by gravity during construction. The benches were also designed so that they could be held in place by gravity during construction.
Fabrication
The unique geometry of the habitat skirt components proved to be a challenge, but a challenge easily overcome by the precaster. The frames were fabricated in a two stage process. First, the frame legs were cast in a specially fabricated steel form complete with chamfered edges along curved corners and hinged release mechanisms. Then, one left leg and one right leg were secured to another, specially fabricated, large steel casting frame. Once secured, each 13.0 ton leg, with several dozen projecting bars, was rotated 90 degrees into place so that three joining beams could be cast. The completed 42.9 ton frames were lifted and transported using specially fabricated steel struts.
In order to achieve the required surface finish on top of the benches, up to five benches were cast at a time orientated upside down in a pre-stressing bed. Many test casts were completed prior to arriving at the optimum corrugated and exposed aggregate concrete finish. The exposed aggregate finish was achieved by using surface retarder and sand blasting after the concrete had cured.
Installation
The special attention on installation procedures taken by the structural engineers during design as well as extensive preparation of the erection hooks by the precaster allowed for both the habitat skirt frames and benches to be installed faster than anyone had predicted. The 76 frames were installed using a 300 ton capacity marine crane in four days. Plastic shims were attached on the rear of the legs to act as a temporary bearing pad after the frames were hung on the erection hooks and rotated under the foundation. Once hung in place, the precaster used hydraulic jacks to slightly rotate the frames and replace the plastic shims with precast concrete bearing blocks that were locked in place with an epoxy adhesive. The gap between the top of the frames and the foundation around the erection hooks were then reinforced, formed, and cast with concrete.
The benches were also placed with a marine crane. The precaster chose, however, not to have their installation schedule driven by the tides and installed the benches with the assistance of divers. The divers guided the 362 benches on to rubber bearing pads placed on the frames in four days. Another crew followed behind installing threaded anchors to secure the benches in place.
- Description_Sheet.pdf (1961 Downloads)
- Fact_Sheet.pdf (1554 Downloads)