Seismic Retrofit Lessons Learned: Technical
The project was a seismic retrofit of a 15-story, 750,000 sq. ft. office building constructed in 1991. The steel portion of the project consisted of systematically strengthening the moment connections throughout the building and installing over 200 dampers without interrupting the operation of the tenants. The contract dictated that the work would start in the basement, progress through the ground floor and the parking garage (floors 2-5), and then continue through the occupied office floors (6-15). The contractor could only occupy three half-floors at any one time. Although my team was extremely experienced, with over 20 years of seismic experience and over 50 years of steel work experience, this project provided us with some significant lessons to take with us to our next project.
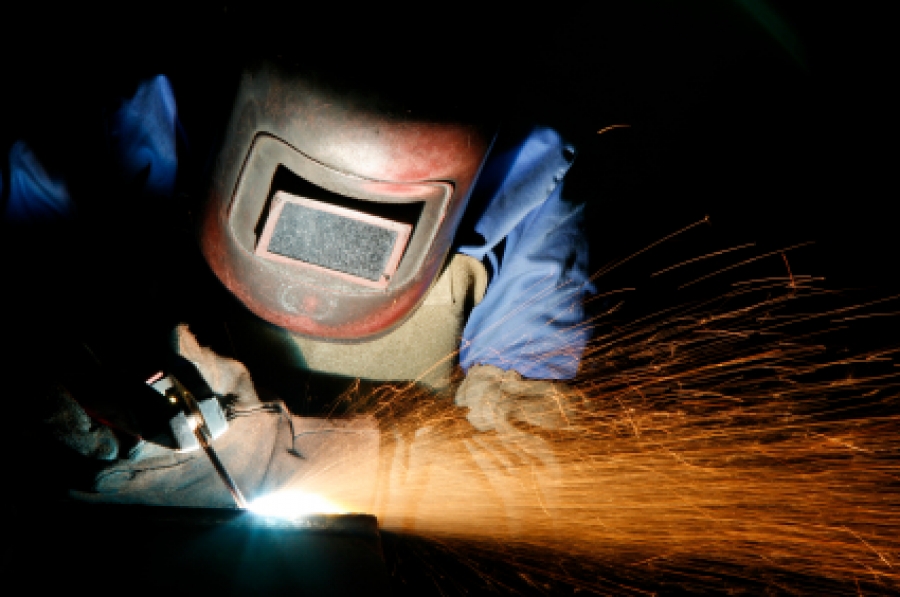
Site Surveys and Details
When dealing with state or government buildings, modifications or upgrades can be made to the existing structure that are required by legislation but are not captured on the building's plan set. In some cases, details of previous upgrades and the identification of pipes, wires, cables, and even water shut-off valves may be unknown.
Site surveys are essential to the success of the fabricator and the manufacturer of the dampers or any other finished product being installed. The damper manufacturer will take 6-9 months to produce and test a viscous damper. Then they will need to ship the parcels by freight. The fabricator does not need as much lead time, but they still have several items to fabricate and ship to the job site. The fabricator’s location, the location of your job site, and the time of year can all effect your delivery outlook, from a couple of days to a couple of weeks. The detailer can also have a serious impact on the job: my crew realized this when we started working on the office floors.
The office floors were the first time we had access to all connections from the inside of the building. While working on the previous five floors, we had to access the connections from the exterior. Once we reached the sixth floor, we realized that the detailer had detailed the entire building from the exterior pointing in. This is the normal orientation when erecting new steel, but no one had communicated to the detailer that we would be accessing everything from the inside once we reached the office floors. This may seem like a minor problem, but all drawings were backward. We had to provide the welders with handdrawn details for 12 different pieces and connections at each work point. The very limited access, in some cases less then 12", made us realize that the orientation of the fabricator’s beveled edge made a significant difference in production time.
Job Site Access
Access to the work points was the greatest factor effecting production on site. The access between the work point and the building envelope was not the only issue. Access to the containment areas was through an occupied office space and the access in the containment area was complicated by air exchange equipment.
Transporting the viscous fluid dampers or seismic dampers through an occupied building is not an easy task. The dampers were between 8'-0" and 15'-0" long, with the lightest unit weighing over 1,000 lbs. To move the dampers from the loading dock to the working points, we had to use a cargo elevator and then maneuver them through office floors with 36"-wide walkways. To accomplish these tasks, we designed and constructed a cart that could handle the load, fit in the elevator, and move in any direction. First, the damper would be lifted onto the cart at the loading dock by a forklift. Once the damper was on the cart, the iron workers were able to elevate the damper by using a chain-fall attached to the head of the front braces. This cart cost my team approximately $6,000 to fabricate and to have an engineer proof the design and certify the safe working loads. The cart saved approximately three crew hours every day we installed dampers for a total savings of over $90,000 in direct labor costs. The cart also provided the iron workers with a safe way to handle the product with only minor surface damage to the pieces. Although the cart was a fantastic homemade tool, it could have been improved by providing a way to raise or articulate the bottom portion of the damper assembly. Had we been able to raise and lower the bottom connection, we could have placed the cart on the floor and installed the dampers without the use of rigging.
Job Site Safety
Demolition and air quality were not the erector's responsibility on this project. On the occupied floors, the contractor used one smoke eater per welder and one air circulation fan per each containment area. The air quality equipment combined with the welding equipment took up almost all of the containment area and caused a significant tripping hazard. When we first setup a containment area with all of the welding and air quality equipment, we quickly realized that no one could walk through, let alone work. The simplest solution was to run wires, leads, air hoses, and anything else we could fit in the plenum ceiling to keep it away from foot traffic. The welders quickly took to the idea and even started running the leads from their welding machines to their guns through the ceiling. This very simple solution allowed us to centralize the equipment while the welders remained mobile.
This project provided my team with valuable tools and techniques. Some of the lessons we learned were refreshers and some were new revelations in their careers.
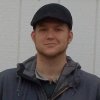
Robert Amstead
Robert is a project manager for a steel erection firm with projects in Northern California, Southern California, and Nevada. His current project types include wind energy, occupied building seismic retrofits, existing bridge seismic retrofits, and new bridge erection. Robert graduated from the University of Missouri Rolla with a Masters in Engineering Management and from the United States Military Academy with a Bachelors Degree in International Relations. Robert has also worked in the luxury residential sector in Florida and as an Officer in the Corps of Engineers.