How to Install Engineered Wood Siding
Video
If you are thinking about installing new siding on your home, engineered wood siding is becoming a popular choice for residential cladding due to its life expectancy and its ease of use. Although installing engineered wood siding may seem like a complicated project, a few tips and tricks can make it a job many experienced do-it-yourselfers can accomplish. Join our host, Jeff Wilson, as he describes the benefits of engineered wood siding and demonstrates a few installation tips and techniques.
Selecting the Right Siding
Natural wood siding has been used to clad homes for thousands of years because of the availability of the raw material and the ease of working with wood. Unlike brick masonry, wood eventually deteriorates and needs to be replaced. Advancements in modern technology have led to the development of an array of building products that offer the look and variety of wood siding but are made with more durable materials.
Vinyl siding provides one of the most familiar examples of a material that can simulate the appearance of wood. For some homeowners, however, vinyl siding doesn’t come close enough to the look and feel of natural wood.
Fiber cement and engineered wood siding products bear a much closer resemblance to authentic wood, with the advantage of a longer life expectancy, and both fiber cement and engineered wood hold paint better than traditional wood siding, making repainting a less frequent home maintenance job.
Another advantage that traditional wood, fiber cement, and engineered wood siding share is nearly unlimited options in the trim details. The siding panels, from typical horizontal lap siding to shingle-type shake siding, cover the majority of the surface area, but the trim around windows and doors and at corners and eaves completes the look and offers an opportunity to accentuate a home’s design.
One advantage of engineered wood siding is that it’s lighter and easier to work with than fiber cement. Because it is made in a similar manner to oriented strand board (OSB) plywood and structural laminated lumber, it can be cut with standard woodworking tools without the dangerous silica dust you get from fiber cement.
Starting with the Trim
Because siding is considered a cladding material, it is necessary to have a weather or vapor barrier properly installed behind the siding. Be sure all windows, doors, and wall penetrations are properly flashed and sealed. Select trim that is compatible with the siding panels. You want the trim to be thicker than the siding, to allow for proper sealing where the siding butts into the trim.
Engineered wood siding typically butts into the trim pieces, so it is necessary to start by installing the trim at the windows and doors. This is much like building a frame around the windows, so be sure to account for the width of the trim when measuring to cut these pieces. Outside corners are typically trimmed with two overlapping trim boards. For the inside corners, rip a square cross-section, like a 2 x 2, to allow the siding panels to butt squarely into the corner trim. Eave trim and roof trim can typically be installed later, once appropriate scaffolding is set up to safely reach and work on these areas.
Installing the Siding
Once you have installed the majority of the trim, you’re ready to begin installing the siding panels from the bottom up. Generally, a starter piece is installed underneath the first course to simulate the typical overlap and to orient the panel at the proper angle. This project is using an 8"-wide siding with a 1" overlap, resulting in a 7" reveal.
- Use a table saw to rip a 1"-wide strip of the siding.
- The starter strip must be installed level and properly spaced from whatever is below it.
- For an installation over wood frame walls that sit on a concrete or masonry foundation, the starter strip should be installed with the bottom about 1" below the joint between the wood framing and the foundation walls.
- For an installation over an adjacent floor protrusion, like a wood deck, the clearance should be about 1", according to the manufacturer’s directions.
- For an installation over masonry or other surface that extends below grade, the starter strip should be installed at least 6"–8" above grade.
Attaching the Siding
To fasten the siding, use galvanized nails sized to penetrate at least 11/2” into the studs. Whether the substrate is plywood sheathing or foam insulation, most manufacturers require the siding to be fastened into the studs. Ring-shank nails are a popular choice for fastening the siding because they have screw-like rings that offer additional protection against nail pullout. Place the nail about 1/2” – 3/4” from the top of the siding panel to allow the nail to be covered by the 1” overlap of the next row.
If you are using a pneumatic nail gun, be sure that the pressure of the nail gun is set to sink the nails flush with the surface of the wood. If you find a few that have not been sunk far enough, hand-nail them flush. If they go in too far, you should caulk and seal the hole prior to painting.
Cutting the Siding
Engineered wood siding is as easy to cut as any engineered wood, like oriented strand board (OSB) plywood or structural laminated lumber. Any of the conventional woodworking tools, from handsaws to jigsaws, are applicable for cutting engineered wood siding.
- A power miter saw with a 10” blade works well for standard crosscuts, perpendicular to the length of the siding panel, as well as angled cuts, as you may need against eaves.
- A table saw is useful for ripping long lengths of the panels, both for starter strips and for long pieces at window and door heads and at the top course under the eaves.
- A jigsaw is useful for cutting notches around trim and vents.
When measuring to cut specific lengths of siding, be sure to account for a small gap at each end that will allow for the thermal expansion of the siding. Check the manufacturer’s instructions for specific requirements; generally this is about 3/16”. This gap will be caulked later. Where you have areas that are longer than the siding panels, you will also need to plan for a vertical butt joint (with expansion gap) to fall on a stud.
Staging the Project
Typically you’ll want to work with a partner on a siding project, with one person at each end of the siding board. In that case, use a siding gauge to evenly space each course for the 7" reveal. A simple siding gauge can be made from a piece of scrap plywood. If you happen to be working on the siding installation by yourself, locking siding gauges are available that provide a seat designed to equally space and hold the next piece of siding for hands-free fastening. As you work up the wall, check the courses for level every third or fourth course. If you find that you’re starting to get out of whack, you can make minor adjustments over a few courses to get back on track.
Ladders and scaffolding may also be necessary to complete the siding project. A pair of sturdy extension ladders can usually make most wall areas accessible. Other options for those hard to reach areas include scaffolding systems, ladder jacks, and walk planks. No matter which solution you choose, always read the manufacturer’s instructions and take the time to perform safety checks prior to continuing the siding installation.
Finishing Touches
The final steps are to caulk and paint. Use a high-quality caulking to fill the expansion joints where the siding panels butt to each other at joints and at the trim. Check the manufacturer’s instructions for any special requirements before painting. Using a premium, durable paint, cover all exposed surfaces and edges as soon as possible following the installation. This is where you can really get creative by using multiple colors to accentuate design features of the house or to highlight the trim.
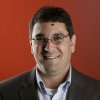
Ryan Carpico
Ryan is a Registered Architect who earned a Bachelor of Architecture from the University of Kentucky in 1998. His experience in a broad spectrum of architectural projects includes design and project management in multi-family residential, general commercial, and institutional projects. This architectural experience is balanced with a background in general contracting of residential and light commercial construction projects. Ryan’s knowledge and ability as both architect and builder enable him to address both the technical and practical sides of the comprehensive body of construction knowledge.
Website: carpicodesign.com/