Decorative Metal
Decorative metal can be defined as metal that provides architectural decoration but has no structural value. Metal can be formed into countless shapes while still retaining many advantageous properties. A wide variety of metals and alloys can be used, including aluminum, brass, steel, tin, silver, gold, and wrought iron. Examples of decorative metal uses are countless but include spiral staircases, guardrails, handrails, gates, decorative brackets, and cornices. For certain projects, designers may specify metals that will react to the elements, resulting in a modified surface appearance called a patina. Other projects may call for painting or factory finishing to protect the metal or add aesthetic detail.
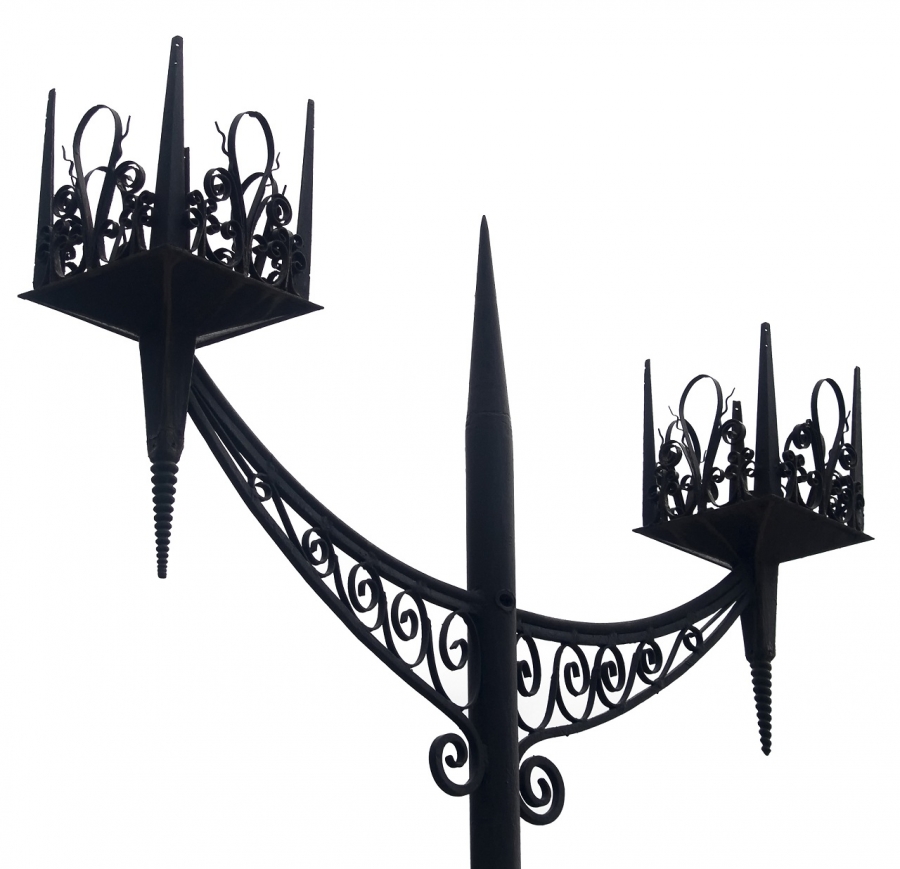
Topic Summary
Forming, casting and forging are some common methods used to shape metals into simple or intricate decorations.
- Metal forming is the relatively simple process of shaping metal by folding or bending it. Metal forming is used in the creation of cornices, cladding panels, trim, gutters, downspouts, brackets, conductors, pitch boxes, and molding.
- Casting is often used to make intricate or complex shapes. This level of detail reduces or eliminates the need for additional adjustments requiring welding or machining, making casting an efficient option. Common examples of decorative metal casting include light posts, brackets, grates, ornate fencing and gates, and other decorative cast iron products.
- Forging is a process in which metal is heated and shaped through plastic deformation by applying compressive force. Forged metal results in a product with greater strength, toughness and ductility that the original material. There are four types of forging for decorative metals:
- Drop forging: the process of hammering hot metal into dies.
- Press forging: uses the slow squeezing action of a press to transfer compressive force.
- Roll forging: sheet metal is pressed between two rollers.
- Cold forging: for smaller products, the metal can be pressed into the die without heating it significantly ahead of time.
The physical properties of forged metal, such as strength, toughness and ductility, exceed that of the base metal. All forging processes provide the same quality, low porosity and high strength-to-weight ratio.
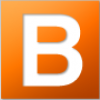
Buildipedia Staff
The Buildipedia research and writing staff consists of dozens of experienced professionals from many sectors of the industry, including architects, designers, contractors, and engineers.
Website: buildipedia.com/