Plaster Assemblies
Plaster assemblies include traditional three coat systems over wood, metal, or rock lath, as well as more recent plaster systems such as veneer plasters.
Plaster in a traditional three coat system is unmatched in its strength and durability. This system is also fire resistive and can reduce sound transmission. Plaster must be applied in such a way that it adheres to the support surface; the support surface, in turn, must be strong enough to carry the weight of the plaster. In the past, applying a plaster coating over a stone or masonry wall seemed to satisfy the strength and texture requirements. However, when framed construction became popular, interior walls lacked both. To solve this problem, thin strips of wood called lath were applied perpendicular to the framing. This solution both strengthened the wall and created a uniform surface to which the plaster could adhere.
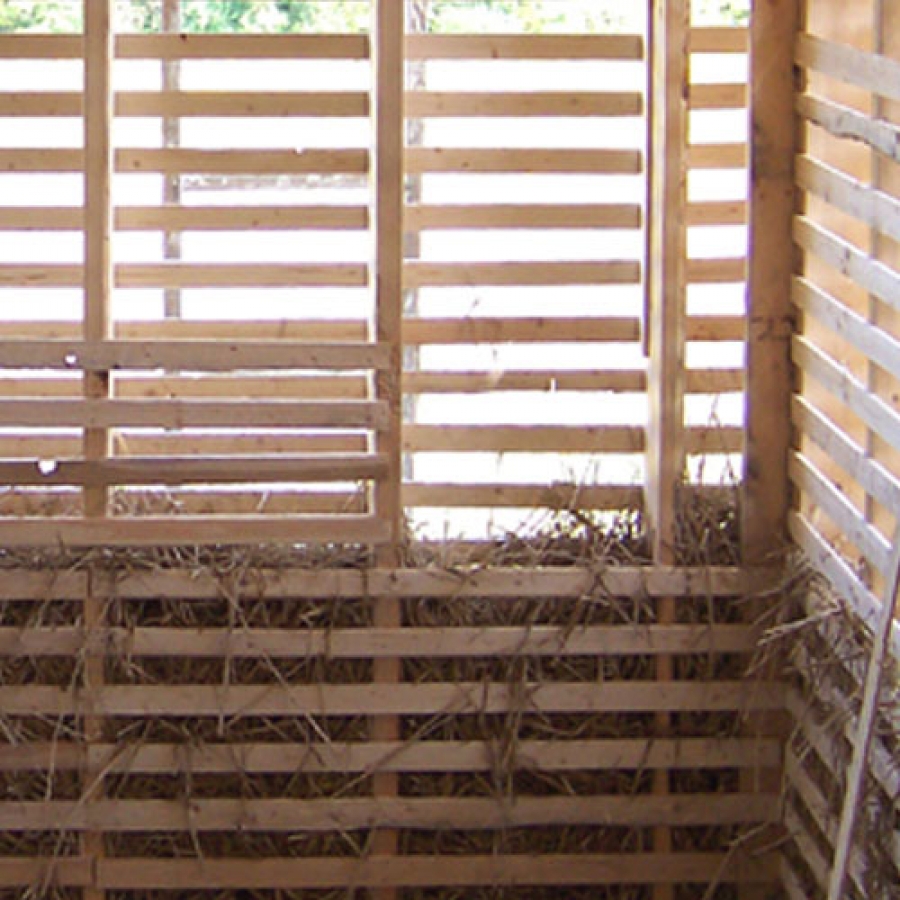
Through the centuries, expertise was gained with gypsum calcinations. Paris, France in the 1700's became the "capital of plaster", because nearly every wooden house was covered with plaster as a protection against fire. This was a decree from the King of France after fire destroyed London in 1666. The large deposits of gypsum near Paris were mined to manufacture "Plaster of Paris". This generic term is used to describe any plaster that results from a mixture of calcined gypsum, sand and water.
To apply plaster using traditional methods, the first coat, called a "scratch" coat, is applied with some of the material being pushed between the lath strips to hold the plaster in place. The surface is roughed up by scratching it with a broom or wire brush and then it is allowed to dry.
Then a second application of plaster, known as a brown coat, is applied. This coat is typically the same thickness as the first, or is a little thinner, and it anchors itself to the first coat while further leveling out the surface. The surface of the brown coat is not further roughened, since the sand in the mixture provides enough texture.
A third and final coat is applied over the brown coat after it has dried. This finish coat is troweled on and smoothed to create a very dense, hard, shiny surface, which is often ready for decoration without any further sanding or preparation.
The plastering process is very labor intensive. Owners, architects, contractors and manufacturers are always looking for ways to save money. Veneer plaster assembly systems came into being for that reason. With veneer plaster, the assembly changes; the lath material has been eliminated. Manufacturers in the plaster industry developed rigid gypsum plaster boards. This plaster base is produced in sheets 4 ft. wide x various lengths x 3/8 in. thick and is directly applied to the wall framing. The plaster board not only adds rigidity to the wall, but because of its size, it covers more area in less time. The manufacturers designed a treated paper surface that reacts with the veneer plaster and creates a strong bond. All manufacturers have different names for their products, but the common thread seems to be the color of the paper. The generic term for this plaster backer board product is "blue board".
In one and two coat systems, veneer plaster finish material in coats of 1/16" to 3/32" thick is directly applied over the prepared blue board. These systems provide a dense, smooth, monolithic surface with good to excellent wear resistance. Because traditional three coat plaster systems can be expensive, these high strength veneer plaster systems make sense when abuse-resistance is a priority. Most manufacturers make veneer plaster finishes with remarkable hardness suitable for walls, column boxes, low partitions and other details in public buildings.
When the goal is to upgrade from a typical drywall assembly, and a hard, smooth, monolithic appearances is a priority, a one coat veneer plaster system is a superior choice. High strength veneer plaster systems offer up to 100 times more abrasion resistance than drywall, and four times the dent resistance.
Veneer systems are a time saver because plastering can take place immediately following the joint treatment ,and a second coat, if desired, can take place after only a short delay. Veneer systems can be ready for decoration in as little as 24 hrs.
Strong interest remains for plaster assemblies. Traditional three coat systems offer abuse resistance, fire resistance, durability, acoustical properties, and outstanding aesthetic design abilities. Veneer plaster finishes offer similar quality traits more economically . Each type of plaster assembly offers a range of choices for the owner, architect, designer and contractor in installed costs and appearance. Like concrete, plaster is hardly new or revolutionary, but it offers many qualities that cannot be duplicated by drywall alone.
See also, Plaster Resoration.
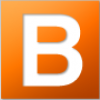
Buildipedia Staff
The Buildipedia research and writing staff consists of dozens of experienced professionals from many sectors of the industry, including architects, designers, contractors, and engineers.
Website: buildipedia.com/