Smoke Migration in Elevator Shafts
With the advent of high rise buildings, fire safety has been of particular concern for architects over the last 100 years. Architects must understand the basics of fire and smoke and the risks associated with creating tall buildings. The spread of toxic smoke that results from fires has been shown to often cause more damage than the fire itself, and it is responsible for more injuries and fatalities.

Studies show that, in the United States, the majority of fire victims have been isolated from the original source of the fire. These types of casualties are due to the toxic effects of smoke. Building codes define a high-rise building as one in which an occupied floor is located more than 75 feet above the lowest level of fire department vehicle access. This would typically be a building of six floors or more.
This article will explore the unique problems associated with smoke migration through the elevator doors into the hoistway shafts of high rise buildings, and the resulting risks to the occupants throughout the entire building. As a result of this problem, building codes have evolved to address the need to regulate smoke migration issues in the hoistways. To conclude, there are different methods available to the architect which satisfy the requirements of the code for smoke containment at the elevator hoistway doors.
As large metropolitan urban landscapes became more condensed and congested, architects and engineers started to build vertically. Cities throughout the United States, Asia, and recently, the United Arab Emirates, have built or are planning to build many mega structures. With the upcoming completion of the Burj Dubai in the UAE, man will have created the world’s tallest building at an astonishing 2,684 feet. That’s 162 stories; compare that to the Empire State Building at 1,250 feet and 102 floors. NYC alone has over 5,700 buildings classified as high rise. Within each of these buildings, modern day elevators have provided a safe and efficient means to access all the floors, as would be expected. Indeed, these buildings could not function or even be possible without elevators. The cabs of the elevators move rapidly up and down their elevator hoistway shaft hundreds of times a day. The hoistway shafts are constructed continuously for many stories, and in the case of express and service elevators, the shafts will be continuous and uninterrupted for the entire height of the building. At such heights, the perimeter walls that create the hoistway will be constructed of materials that provide a fire protection rating based on Underwriters Laboratory (UL) classification of 2 hours.
When a fire occurs, smoke will begin to move upward to the top of the building as it finds the path of least resistance. Smoke will move as a result of the difference between the heat of the smoke and the cooler ambient air. Smoke also moves due to the expansion of the hot gases. When smoke is allowed to enter the elevator hoistway, a great many more occupants of the building are put at risk, even though the original source of the fire may have been on a lower floor. Air is entering into the shaft on lower floors by way of building air leakage, and it is forced out into the building on the upper floors. The reason for this is what is referred to as the stack effect.
Stack effect is the vertical movement of air into and out of a building caused by pressure differences. This pressure is created by the differences in air temperature between the outdoor air and indoor air. The resulting air movement can be positive or negative. In colder climates, the air movement is negative, resulting in upward airflow in building shafts; in hot climates the air movement is positive, resulting in downward airflow in shafts. With the increased height of a building, the stack effect is also increased. The higher temperatures of the smoke and gases that enter a shaft will also increase the force of normal stack effect.
Stack effect and winds will intensify the vertical movement of smoke in high-rise buildings; it is primarily the leakage area around elevator doors that creates a situation in which smoke can migrate to upper floors in a building. This phenomena has been investigated and thoroughly documented. Building air leakage can come from many sources, such as: construction gaps; cracks in walls, partitions and floors; gaps around closed doors; elevator shaft vents; elevator and stair shaft walls; and large openings such as open doors and windows, particularly at the lobby level. Smoke will migrate through elevator hoistway doors to locations remote from the fire, because a closed elevator door will have a typical leakage area of approximately 0.6 square feet. That is about 40.5 cubic feet per minute of air leakage. Smoke entering and exiting the shafts through these gaps, combined with the strong forces of the stack effect, will force smoke to migrate to the upper floors of a building very rapidly. The two dangers of smoke are reduced visibility from the particulates, and the toxic gases, which will have lethal results. The most significant toxic gases in smoke are carbon monoxide, carbon dioxide, hydrogen cyanide, hydrogen chloride and nitrogen dioxide. For humans, the most toxic gas from a fire is carbon monoxide, which building fires generate in large quantities. Another important factor of smoke is the concern of reduced visibility. The particulates in the smoke are not usually fatal; at worst they will cause eye and respiratory problems. Reduced visibility brought on by smoke is not directly fatal, but the results of not being able to safely egress may be.
One solution to the air leakage problem would be for elevator doors to have some type of gasket around the opening; however, the maintenance of such a gasket over the life of the building would be problematic, at best. If the leakage area at the elevator doors could be drastically reduced, however, then a significant increase in visibility would be attained on the upper floors of a typical multistory building.
There have been many instances that illustrate the dangers of fires and the lethal effects of smoke in high-rise buildings. In many examples, the fire began in lower levels of high rise buildings. In 1995, a fire began on the 6th floor of a 30 floor high rise apartment building in Toronto, Canada. It was later determined that smoke moved rapidly to the upper floors and caused six fatalities. The MGM Grand fire in Las Vegas in 1980 was the second worst hotel fire in modern U.S. history. It was another alarming example of how the spread of smoke can prove to be fatal; 75 of the 85 fatalities were from smoke and carbon monoxide poisoning. Unprotected vertical openings, which included elevator shafts, were found to contribute significantly to smoke spread throughout the high rise tower.
The purpose of the many building codes is to provide a minimum standard to protect the life and health of the building occupants, as well as to protect property. Building codes are a legal means of giving jurisdictions the authority to regulate a building's construction, quality of materials, use and occupancy, location, maintenance, structure, and certain equipment; codes can even, to some extent, control the design. Changes in the building codes are revised and updated constantly. These updates occur for many reasons, with the most common reason being experiences gained from past events where public safety was jeopardized or, worse yet, there was loss of life.
The 2000 International Building Code (IBC) did not adequately address the migration of smoke throughout the entire building. In April 2000, the International Code Council (ICC) began hearing proposals for the reduction of smoke migration throughout buildings. In particular, proposals were submitted by the fire safety committee to address the movement of smoke throughout a building by way of the elevator shafts or hoistways. Previous regulations have typically focused on limiting smoke movement in areas of egress, such as vertical stair towers or horizontal corridors.
Stairwell shafts, because of their relatively simple design, are able to be successfully pressurized by mechanical means. Providing a pressurized system for the elevator hoistways can prove to be problematic, if not impossible to successfully obtain. The required fan flow rates may be as much as 50 times larger for elevator shaft pressurization systems than for stairwell pressurization systems. To achieve the code's required minimum pressure differences in elevator shafts would require substantially larger air flow rates. This creates a significant over-pressure on the first floor. Many factors, including hoistway vents, will have an effect on the shaft pressurization design. Additionally, it would be essential that door operators and hardware sets, as part of the pressurization system, be able to operate under pressurized static pressure.
Elevator hoistways of more than three stories are required by the IBC to be vented at the top. The purpose of venting the hoistway is that, in the event of a fire, it will provide a means for smoke and hot gases to escape to the outside air. The vent area is required to be 3.5 percent of the total shaft area, or at least 3 square feet per elevator car. However, if the building is equipped throughout with an approved automatic sprinkler system, the code does not require a vent to be installed.
Studies are currently underway using advanced strategies and software programs to predict the movement of fire and smoke and provide floor pressurization to control smoke during high rise fires. With the design of a smoke-control scheme, it is believed that the role of elevator shafts with selective pressurization will form a safer environment from the threat of flames and smoke.
Simply complying with the fire and building codes will not always provide optimum fire safety. Egress systems must provide sufficient evacuation time before smoke reaches lethal levels. By controlling air leakage into elevator shafts, smoke migration through a building can be controlled and minimized. It is important that architects understand smoke movement throughout a building, and it is a topic that has been studied by many engineers and government agencies. Studies have been done that compare typical elevator doors with normal air leakage to other systems with reduced air leakage. Ways in which air leakage into elevator shafts can be reduced include providing an enclosed elevator lobby or making provisions for a temporary barrier system.
Enclosed elevator lobbies consist of walls, doors, floors and ceilings that form a continuous fire rated barrier on all sides of an elevator lobby. The doors would remain open during normal building operations; however, in the event of a fire or when smoke is detected, the doors would release and automatically close. These fire door assemblies would need to meet the requirements for a smoke and draft control door assembly with an artificial bottom seal installed across the full width of the bottom of the door assembly. The air leakage rate of the door assembly would not exceed 3.0 cubic feet per minute per square foot of door opening at 0.10 inch of water for both the ambient temperature and elevated temperature tests.
There are basically two types of temporary barrier systems. The first type is an automatic accordion style barrier that forms an enclosed elevator lobby. The second type is a rolling gasketing smoke containment system used in conjunction with a fire-resistance-rated elevator hoistway door and frame assembly. This system is installed directly above and in front of the elevator doors. When smoke is detected at elevator landings, the screen will automatically deploy, rolling down and magnetically attaching itself to the metal frame of the hoistway. The screen is a polyimide plastic sheet with a factory applied filament yarn for reinforcement. The film protects the elevator opening from vertical smoke migration by creating a tight fitting smoke and draft control barrier. The air leakage of this system is less than 0.5 cubic feet per minute based on UL 1784 test methods. The maximum allowable air leakage is 3 cubic feet per minute.
Issues concerning smoke migration in multi-story buildings have been a serious concern for the life safety of building occupants for many years. Since 2004, The American Society of Mechanical Engineers (ASME) has been conducting hazard analyses to determine how elevators might be safely used for evacuations during a fire emergency. The 2009 International Building Code provides for occupant evacuation elevators as a means of self-evacuation in the event of a fire for buildings greater than 420 feet, but nothing more is said about how the elevators will operate. Though ASME is not affiliated with the International Code Council (ICC), their hazard analysis findings for fire safe building design involving elevators would be submitted to the ICC to be adopted in future editions.
With architects and engineers having an understanding of how fire and smoke can move through buildings, successful strategies and choices in design can made to prevent the spread of smoke migrating through elevator shafts. This will reduce the risk to life and provide a safer environment for the building occupants.
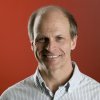
David Ingold
David Ingold is a graduate of The Ohio State University School of Architecture and a member of the Construction Specifications Institute (CSI) with Construction Documents Technology (CDT) certification. With more than 18 years of experience, David brings a broad knowledge base and understanding of design and construction to a wide variety of project types. He is an accomplished senior project administrator with experience in developing all phases of architectural documents. David has performed key responsibilities as a project leader, specifications writer, and coordinator for projects of all types and complexities including low- and high-rise condominiums, sporting facilities, higher education and government research laboratories, manufacturing facilities, wastewater treatment plants, parking garages, and campus master plans. David’s greatest aspiration is to provide construction administrative services to fully execute project designs.
Website: buildipedia.com/channels/on-site