Structural Insulated Panels vs. Conventional Framing
The all-inclusive, load-bearing design of structural insulated panels (SIPs) offers an energy-efficient, quiet alternative to conventional wood framing methods. In recent years, SIPs have increasingly grown in popularity as builders strive to provide more durable products, use more environmentally sustainable building methods, and reduce costs. According to AMA Research, SIPs are now the fastest growing new building method on the market.
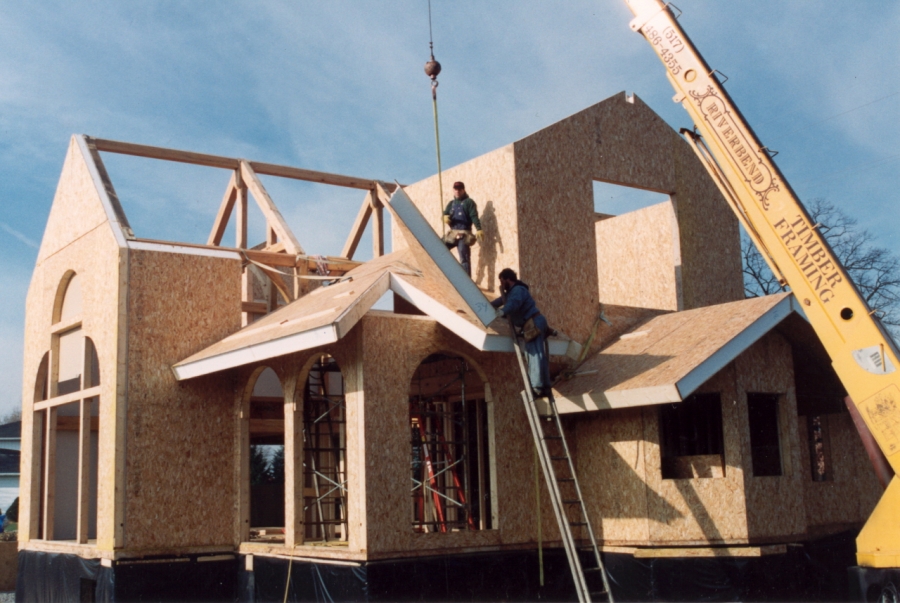
What are Structural Insulated Panels (SIPs)
“[SIPs] offer a tremendous performance in energy efficiency through the air-tight nature of the design,” says Tony Mammone, P. Eng., Insulspan Product Manager. SIPs consist of an insulating layer of rigid foam board sandwiched between two pieces of oriented strand board (OSB). Treated plywood, metal, or fiber-cement boards are occasionally used instead of OSB. The result of this multi-layer, air-tight construction is exterior sheathing, insulation, and structural framing all in one piece. SIPs are available in various lengths ranging from 4'-0" to 24'-0".
Types of SIPs
The material that forms the rigid foam board in SIPs is usually made from polyisocyanurate (a polyurethane derivative) or expanded polystyrene (EPS). The inner board of SIP is also sometimes made from compressed insulating straw, but this method is less common.
- Expanded Polystyrene (EPS) Insulated Panels have a nominal R-value of approximately R-4 to R-5 per inch of thickness and are commonly available in 48" x 96" (other sizes are available) panels, weighing approximately 110 pounds each, according to the U.S. Department of Energy (DOE).
- Polyisocyanurate Insulated Panels used in the form of foam or liquid foam, which later hardens and strengthens have a nominal R-value of approximately R-6 to R-7 per inch of thickness, or a reduced initial R-value of R-9 to R-7 for the liquid foam version, according to the DOE. Polyisocyanurate SIPs used for walls are usually 3.5 inches thick, and ceiling panels can be as much as 7.5 inches thick. Polyisocyanurate SIPs are typically more expensive than other options but are also more resistant to water-vapor diffusion and fire. They insulate up to 30 to 40% better than their polystyrene (EPS) counterpart, according to the DOE.
- While Compressed Straw Core Insulated Panels are considered to be the most eco-friendly option due to the fact that they are made of agricultural straw, which is renewable and recyclable, they also provide less insulation and are heavier than the aforementioned SIPs.
“Not all properties are the same. Some give incredibly high R-values for 90 days, sometimes even for two to five years, but then the R-value might drop significantly,” Mammone says. Mammone recommends kiln-dried EPS, because moisture is removed to make it more stable.
SIPs Advantages
Building with SIPs presents several advantages over conventional framing methods, including increased energy efficiency, reduced possibilities of structural damage and deterioration over time, and reduced costs. SIPs save energy by reducing the heat loss characteristic of conventional wood framing, as well as by reducing air leaks. According to the DOE, homes and commercial buildings constructed with SIP walls save 25% in energy losses. When floors and roofs are constructed by using SIPs, savings increase exponentially. The lifespan of SIPs is 50 years or more with no cost input. The air-tight construction of SIPs also virtually eliminates the possibility of mold in the exterior, nail pops, twisting of studs, and warping. SIPs can also make workers' jobs easier after construction is complete: for example, SIPs eliminate the need to find studs prior to the installation of siding or drywall.
"There is a tremendous savings, and it happens within the first month you go into the house, and savings continue through the life of the mortgage."Tony Mammone, P. Eng., Insulspan Product Manager
Despite these advantages, sticker shock may be a deterrent to using SIPs, which are typically more expensive than the materials used for conventional wood construction. However, while the initial cost of SIPs is higher than material costs for conventional building materials, when waste reduction, increased site productivity, and reduced labor costs are taken into account, the overall cost is virtually the same or sometimes lower than the cost of conventionally constructed buildings. “There is a tremendous savings, and it happens within the first month you go into the house, and savings continue through the life of the mortgage,” Mammone says. Due to the fact that SIPs are lightweight (about 3 pounds per square foot) and easy to assemble, the use of SIPs significantly increases framing productivity. The use of SIPs can reduce framing labor by as much as 55%, according to a study by Reed Construction Data. Labor costs are also reduced, because fewer workers are needed to erect a structure incorporating the all-in-one SIPs. Some manufacturers even offer precut SIPs, which further reduce labor costs.
SIPs Considerations
Manufacturer Spotlight: Insulspan
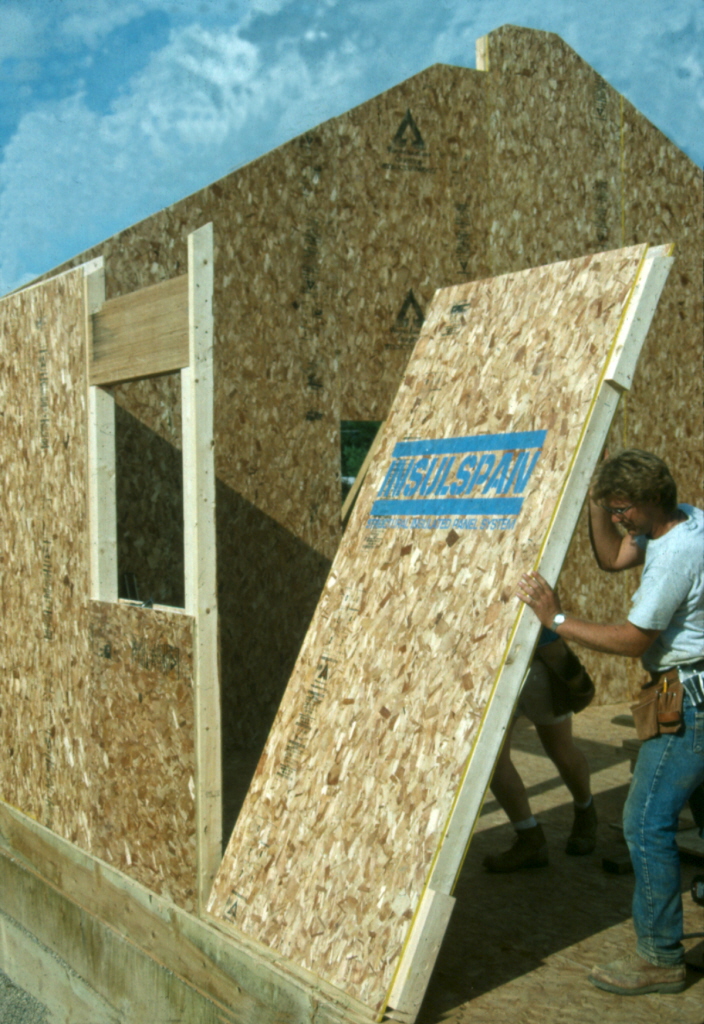
As with any technology, there are a few factors to consider prior to construction with SIPs. As with any building, those constructed by using SIPs can become susceptible to rodents and insects. There have actually been cases where rodents have tunneled through SIP walls, according to the DOE. The DOE suggests applying insecticides to panels, maintaining indoor humidity levels below 50%, and treating the surrounding ground with insecticides before and after construction to help reduce the risk of an insect or rodent invasion. Boric acid-treated panels can also be purchased, which can help repel insects. SIPs may also present challenges during remodeling or installing plumbing lines and electrical wiring, which may require special equipment. Performance during fire is also a common concern for buildings constructed with SIPs. However, covering SIPs with a material such as gypsum can help significantly reduce this risk, because the gypsum cover can help delay the spread of fire and lengthen the escape time. Applying concrete siding over SIPs can also help to reduce the risk of fire for homes in wooded areas, according to Mammone.
Creep, or long-term sagging, is also a common concern with OSB. “There is creep, but you have to design for it,” Mammone says. “OSB is organic living material, which means it can move. Good SIPs are designed with this in mind. It’s important to work with a good SIP company that has a design engineer that considers regional needs.”
As demand increases, manufacturers continue to examine various ways of using rigid fibrous and cementitious insulating materials in SIPs. Cementitious insulation is a spray foam with the consistency of shaving cream. It has an R-value of approximately R-3.9 per inch and can be pumped into hard-to-reach crevices, which increases energy efficiency. The cost of cementitious insulation is comparable to that of polyurethane, but it is also nontoxic and nonflammable, which greatly reduces the fire hazard that is present with current SIPs. Rigid fibrous materials under consideration for use in SIPs consist of fiberglass or mineral wool, both of which are commonly used to insulate air ducts. Rigid fibrous materials have an R-value of approximately R-4 per inch of thickness.There is also a new SIP sealant available through Insulspan that is volatile organic compound (VOC)-free. The zero-VOC sealant improves indoor air quality, which is “better for the people who build the homes, and better for the people who live in them,” Mammone says. “In life you get a report card on everything you do. You have to make the right decision every time.”
- Installation Guidelines (3413 Downloads)
- Construction Assembly Details (3593 Downloads)
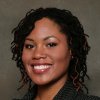
J. Mariah Brown
J. Mariah Brown is a technical research writer and the owner of Writings by Design, a comprehensive business writing service company that specializes in business development, promotion, and client outreach. She has worked in a variety of technical and non-technical industries including, but not limited to, Government, Non-Profit, Engineering, Translation and Interpretation, Christian and Women’s Publications, and Fashion and Beauty. She is a graduate of the prestigious E.W. Scripps School of Journalism at Ohio University and is currently pursuing a master's degree from Gonzaga University in Communication and Organizational Leadership.