Contractor Selection Moves Beyond the Low Bid
Two large-scale construction projects, one an interdisciplinary research building on the University of Colorado campus and the other a new arena located in Lincoln, Nebraska, shift away from awarding contracts based solely upon lowest bid.
Many business-as-usual practices within the building industry are being rethought. Among them is the practice of automatically awarding a contract to the lowest bidder. It is becoming more common for clients, architects, and general contractors to team up early and work closely together for the good of the client, the project, and the project’s end users. Such is the case for the Colorado Initiative in Molecular Biotechnology, with a new building on the campus of the University of Colorado at Boulder that was designed by Robert A.M. Stern Architects, and for the new Haymarket Arena in Lincoln, Nebraska.
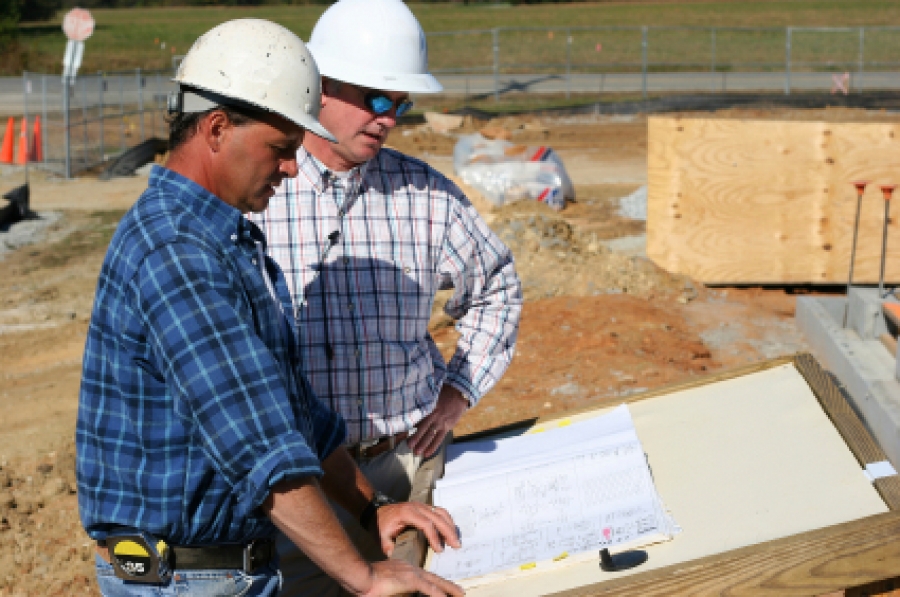
Although construction contractors and their tradesmen have always been respected as valuable building teammates, they typically have been considered “vendors” and not “professionals”; this distinction is evident even in the AIA codes of professional practice and corresponding construction management documents. A general industry litigiousness, to some degree legitimized by the architectural community, has mandated the strict separation of architect from contractor, of professional from vendor. Likewise, construction industry representatives who also played a role in the "litigate game" were bound all too often by mutual distrust to provide fixed prices based on finished design documents. The change order process was then relied upon for all types of corrections. While this process now is widely seen as antiquated, the hard bid process is still appropriately used today, with competitive bids relating to well defined, carefully specified, and competitively bid purchased items including labor, materials, overhead, and profit in straightforward projects.
Tech-Based Changes Preface Work Flow Changes
The design and construction industry of today relies on the powerful costing spreadsheets and databases that allow an owner and architect to be quickly creative during the design process, testing the application of first cost and life cycle cost alternatives on the deployment of a building and its systems. As Paul Leef, AIA, LEED AP, campus architect for the University of Colorado at Boulder campus, states, “In designing high-performance buildings, teaming with sophisticated general contractors allows us to make important decisions about both first cost and life cycle costs that can be informed by an early cost analysis.” As Director of the University’s Planning, Design, and Construction Department, Leef used the Construction Manager/General Contractor (CMGC) negotiated bid process with a guaranteed maximum price to deliver the construction of the new $160 million, 336,800 sq. ft. Jennie Smoly Caruthers Biotechnology Building, set to open on the East Campus of the University of Colorado at Boulder. Including a $15 million American Recovery and Reinvestment Act (ARRA) grant, the LEED-certified building will be home to the Colorado Initiative in Molecular Biology (CIMB) at the University of Colorado, which will foster some of the world’s most important multidisciplinary molecular biotechnology research. CIMB will be home to another inventive genius, 1989 Nobel Prize winner Thomas Cech.
Robert A. M. Stern Architects, in association with HDR Architects, stayed with the Tuscan Vernacular characteristic of the University of Colorado campus. The CIMB building is being constructed by JE Dunn Construction, and time is of the essence with regard to the completion and occupancy of the building. Not only is world-class research occurring on the University of Colorado campus, but the building, slated for completion in March 2012, will also house a technology transfer “community.” This will include the involvement of the Deming Center for Entrepreneurship of CU Boulder’s Leeds School of Business and will provide enterprises focusing on the cancer, aging, cardiovascular, and tissue engineering research occurring in the facility. According to Leef, “One of several compelling reasons for using the CMGC process on the CIMB building is its fast-track delivery, when we have a revenue-producing situation with an auxiliary enterprise, self-sustaining business that’s housed inside the facility. What we’re also finding, with high-performance building contractors, that they’re more sophisticated than they used to be and are good partners to have early on in the process.”
Although support for the facility is nearly universal campus- and state-wide, when asked how the University as a government agency can use a negotiated, non-hard bid process, Leef says, “There’s still a competitive element to the CMGC process. We pay JE Dunn for their professional services on a fixed fee to a guaranteed maximum price, protecting the University. It’s still an open book bid process among JE Dunn’s sub-contractors. It’s still in essence a competitive process.”
Leef also mentions that a low bid/hard bid delivery process is still in the University of Colorado's “tool belt” and that they still use it for the right kind of project, like the relatively simple, straightforward construction of the Athletic Department’s new basketball/volleyball practice facility, which was opened in August 2011.
Local Priorities Inform Contractor Selection
In Lincoln, Nebraska, another major project is being successfully built by using construction management as opposed to the traditional low-bid method. The new Haymarket Arena will soon become a major Lincoln and Lancaster County community asset. Distributed over approximately 450,000 sq. ft. on four concourse levels, the facility will feature the University of Nebraska–Lincoln (UNL) men's and women's basketball teams as anchor tenants, as well as provide a wonderful entertainment venue for the entire Lincoln and Lancaster County region. Local voters are cautiously supportive of the project and passed a bond issue allowing the construction of the $340 million project, which will seat 16,500. The project is owned by the City of Lincoln and overseen by the West Haymarket Joint Public Agency (JPA), a government agency formed by the City of Lincoln and the University of Nebraska-Lincoln. The JPA, comprised of three members (the mayor, a Lincoln City council member, and a member of the University of Nebraska Board of Regents), agreed that a new process should be used to guarantee the project’s success.
According to Dan Martin, City of Lincoln Project Manager for the Haymarket Arena, “One of the things that the board that oversees this project wanted to make sure [is] that when we award work, we keep that work as local for Lincoln and Lancaster Counties [as possible]. Much of the work that has been put on to this job site is all people that are Lincoln and Lancaster companies and employees.”
During the campaign to approve the bonds for the project, one criticism was that too many of the jobs for the arena were going to go to companies from out of town. In response, the City of Lincoln allowed the JPA to use Construction Manager at Risk (CMR) legislation to modify the City’s low-bid selection process, which would have otherwise mandated the selection of low bidders regardless of their location. According to Chris Beutler, the Mayor of Lincoln, along with JPA members Jayne Snyder, a Lincoln City Councilperson, and UNL Regent Tim Clark, in a published opinion in the Lincoln Journal Star: “While 'lowest bid' sounds good, it sets a standard that cannot be lowered further, a detriment to taxpayers.” In the revised approach, instead of automatically accepting the lowest responsible bid, other factors will be weighed, such as safety records and quality of work.
For construction management of the project, national contractor Mortenson Construction was selected in a partnership with local commercial construction firm Hampton, active in Lincoln for over 60 years. The CMR process includes a guaranteed maximum price, and the Mayor and his fellow JPA members mention in their opinion piece that “It is important to remember that if Mortenson–Hampton exceeds the construction cost limit, they are responsible for paying cost overruns,” which is an important statement, ensuring public confidence in the expenditure of public funds. Transparency is also improved with the publication of all bids on the Haymarket Arena project website.
These criteria, and the use of construction management processes, highlight the contemporary construction industry’s improved services, which offer owners, contractors, and sub-contractors who serve the construction industry as professionals, not just as vendors, keeping quality up and price down.
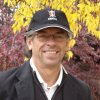
Morey Bean, AIA, LEED AP
Colorado's 1999 Architect of the Year and Vice Chair of the Boulder Chapter of the Urban Land Institute, Morey’s experience includes the successful development of the Colorado Architecture Partnership, an architecture firm dedicated to sustainability and green building. Morey was appointed by the Chief Architect of the GSA to the National Register of Peer Professionals. He serves as a ULI Service Advisory Panelist and was a charter member of the Colorado Chapter of the USGBC and past president of the Colorado South Chapter of the AIA. He is a construction litigation services expert witness, land development analyst and sustainability strategies consultant.
The author was honored by the Colorado Component of the American Institute of Architects as their Architect of the Year in 1999 and is on the Roster of Neutrals for the American Arbitration Association (AAA), providing dispute settlement for the design and construction industry.
Website: www.cyberarchitects.com