Life Cycle View: Total Cost of Ownership Drives Behavior
Initial costs represent only 15% of a building’s total cost. If you ignore this when developing a building, you are wasting the other 85% of your costs. Keeping the initial capital cost as low as possible seems right, but it’s costing you a lot more over the life of the building. Visibility into the total cost of ownership is one way to address this. Justification and decisions should be based on the total cost of ownership, not just initial costs.
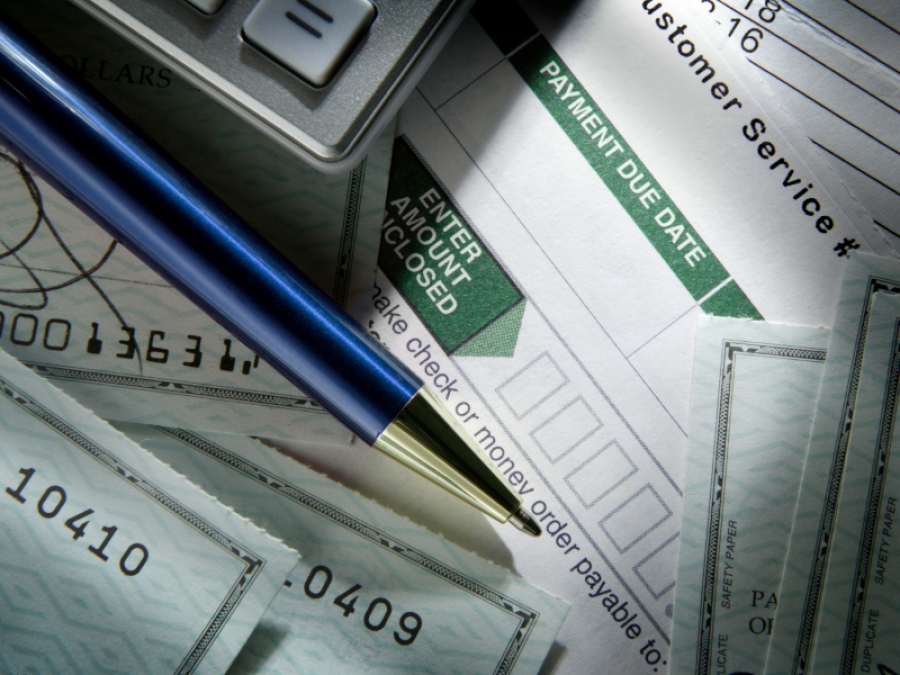
Estimate the total cost of operating over the life of the facility and use this information as part of the budgeting and decision-making process to arrive at better decisions that include more up-front funding to design and build a more efficient building.
Using a lifecycle costing (LCC) approach can help reduce short and long term costs. LCC goes beyond when to replace a particular piece of equipment or building component; it’s about taking a systematic approach to balancing maintenance costs, operating costs and replacement/refurbishment costs over the life of the asset. While it may seem complicated, in practical application, it is very simple.
LCC includes all costs associated with building assets from acquisition to disposal/replacement of the building itself. For practical reasons, a typical lifespan is often used, such as 30 years or 50 years, depending on your organization and the type of facilities you own.
For costs measured in future years, adjust upwards for inflation costs each year and then adjust downwards for the real value of money in that year compared to today’s money, which is easy to do with most spreadsheet’s built-in formulas.
How Can You Use Lifecycle Costing for New Facilities?
While minimizing the initial capital cost of a new building seems right, that save-now approach could cost a lot more over the life of the building. The initial capital cost is the most visible and easily measured part of the decision-making process, yet the high cost of bad decisions is only seen in the future.
The easiest way to reduce total costs is to build operating efficiency into the design and construction of the building using existing techniques, many of which are well developed but not always used. Here are some of the more useful ones.
Green Initiatives
Use green standards and initiatives to lower ongoing energy costs. This includes how the facility is designed and the energy efficiency of the equipment. It’s politically and socially correct while contributing to a lower total cost of ownership.
Facility Operations Input in Design
Involve facilities staff and service providers such as custodial, grounds, mechanical/electrical service contractors to provide guidance on design to minimize operational costs.
Value Engineering
Value engineering goes beyond financial analysis and assesses the design, including materials, equipment and functional requirements to eliminate or modify design elements and reduce unnecessary costs.
Commissioning
Commissioning ensures the building is performing as it was designed, meets specifications and the effort you put into the design to reduce costs will be realized.
How Can You Reduce Operating Costs at Your Current Facilities with Lifecycle Costing?
Your existing facility has an operating budget and a capital replacement budget. You can manage down these costs with an LCC approach, which could include extending or advancing their replacement based on the information you collect. The best part of the process is it forces you to understand your current operational costs and the alternatives.
The most important thing is to understand the costs of your major systems. This includes regular servicing and preventive maintenance, ongoing repairs, consumables and energy costs. With the right software or for smaller portfolios, an up-to-date spreadsheet, you can have the information you need.
Secondly, you need to have information on the condition of your equipment, which is closely related to the reliability, maintenance/repair costs and energy consumption, not to mention the required replacement timeframe.
With your maintenance costs under control, look at your older equipment and using LCC, estimate your current costs, replacement costs and timeframes. Re-do the assessment with earlier replacement that includes lower operating costs, including energy, and make decisions based on that information.
Using the LCC approach will provide you with the financial information you need for an informed decision. It also makes you look at all your costs much more closely, thereby helping to reduce current and future expenses.
Reducing Total Costs Through Design and Construction
The easiest way to reduce total costs is to build operating efficiency into the design and construction of the building using existing technologies.
The caveat is that these techniques may extend the total project time, increase consulting/professional fees up-front and may result in design changes that increase initial costs. Build these techniques into the initial schedule and budget and then use the results, along with the related financial analysis, to justify increased construction costs that reduce ongoing costs.
Multi-Disciplinary Approach to Design
Involving the full range of disciplines throughout the design process, versus an architect-led approach, enables better integration of the disciplines. The end result is driven by solutions rather than design.
Green Initiatives
The increased costs of a green building, especially when it is LEED certified, are usually easier to justify and get approved. Some levels of government are already mandating or encouraging green buildings. Keep in mind that while formal standards and initiatives such as LEED carry the green label, other techniques should also be used to reduce costs. When justifying the increased cost under the banner of green initiatives, be sure to take the full benefits of energy reductions form all initiatives into account.
Facility Operations Input in Design
It is rare during the design phase of a new project for facility professionals to be consulted for input on the design regarding ways to minimize future operational costs.
Since the ongoing costs are up to 85% of the total costs of ownership, this is a significant oversight. If you have adequate internal operations resources with the time and experience necessary, this is a very low-cost method to save money. That said, you may to augment internal resources with external resources or consultants for certain areas. For instance, involving service providers for janitorial, grounds, maintenance, security and other services will provide invaluable guidance on design elements that can reduce operational costs.
Lifecycle Costing Calculations
The LCC analysis takes four key cost components into account to determine the lowest total cost of design alternatives. It’s a well-established economic analysis that takes a component –by-component approach to the initial cost as well as maintenance, energy and replacement or renewal costs of the equipment over the life of the building. The analysis is rigorous, taking into account the time value of money and inflation to develop a net present value for the total cost of the components over their entire life cycle.
This technique can be used for a design/build tender to achieve the lowest total costs rather than the lowest initial construction cost. By requiring LCC analysis by a third party as part of each submission and using the results as a basis for final selection, you can make the best financial decision.
The formula for total costs is simple:
Initial/Capital Cost
Plus Maintenance Cost
Plus Operating Cost (Consumables/Utilities/Staffing)
Plus Refurbishment/Replacement Costs (Reduce by Salvage Value, if any)
Total Lifecycle Cost
Put all your costs in a row in your spreadsheet, inflating your operating costs (especially energy) each year.
Use the net present value (NPV) formula in your spreadsheet software to calculate the real cost of the replacement and operating costs over the anticipated lifespan. Copy it and make changes based on earlier or later replacement and reductions in operating costs to determine the best option.
Value Engineering
This tool is closely related to LCC and they often work together. Unlike LCC, value engineering goes beyond purely financial analysis and assesses the design, including materials, equipment and functional requirements. The intent is to eliminate or modify elements of the design that are either not required to achieve the functional requirements or add unnecessary costs.
Generally, value engineering will drive design and equipment selection alternatives. LCC will then analyze the total economic impact of those decisions.
Commissioning
Even if the design reflects the best value in initial and total cost of ownership, the actual implementation of the design during construction needs to be validated against the design specifications. Payback on commissioning costs for energy alone is under five years. This has a huge impact on the total benefits over the life of the building.
Commissioning is a quality assurance process that verifies that the systems installed during construction meet the original design criteria through testing and documentation. This process is conducted by third party commissioning consultants throughout the construction process.
To get the best value from the commissioning process, the FM staff should be involved in the commissioning and receive training on the systems during the construction phase. Since the cost of operations is by far the largest part of the total cost of ownership, it is critical to give operational staff the knowledge they need to operate the facility efficiently in accordance with the design intent.
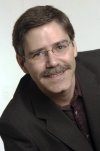
Michel Theriault
Michel Theriault is the author of the new book “Managing Facilities and Real Estate." He is an independent consultant providing strategic and management solutions for Facility Managers. He has many years of experience in all areas of FM, including operations, performance management, change management, customer service, service level definitions, outsourcing, and RFP’s. He authors a blog at thebuiltenvironment.ca and recently started a new website for FM surveys and research at www.fminsight.com. He welcomes your comments and feedback at michel@strategicadvisor.ca or strategicadvisor.ca.