Pay Attention Span: Smart Bridges
The various blogs I follow send me newsletters, and one article regarding new smart bridge technology caught my attention last Friday. A “smart bridge” is probably better labeled as a talking bridge – one that communicates its status to those who are listening for follow-on interpretation. Baseline measurements of critical strain, deflection, and corrosive conditions can be established with the structure following project completion, then monitored throughout the bridge’s service life.
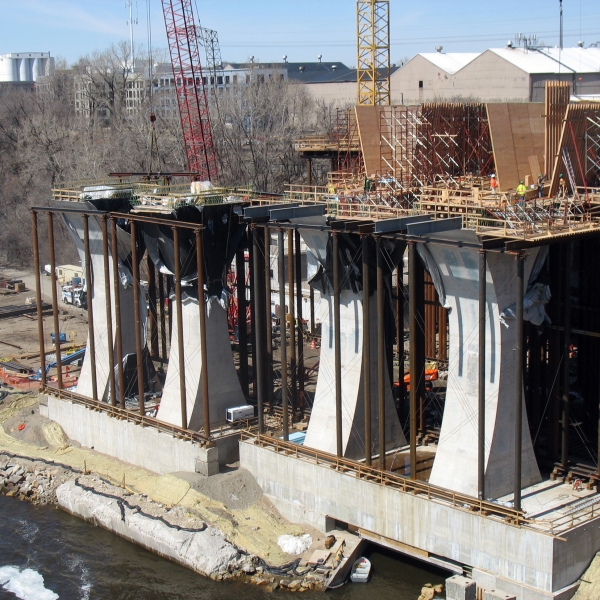
A specific advancement recently is the use of data sensors that can communicate this diagnostic information to remote monitors via a wireless ether-net, with potential cost savings over the currently more common tethered systems. This article discusses state-of-the art bridge monitoring equipment. Since I work for a Columbus, Ohio based company, it pains me to write that this technology has been pioneered by the University of Michigan’s Department of Civil and Environmental Engineering.
In August 2007, the nation mourned following the tragic collapse of the I-35 W bridge across the Mississippi River in Minneapolis, Minnesota. It is very fitting that the replacement bridge, the St. Anthony Falls Bridge (completed in September 2008), was not only built quickly and effectively but also includes “smart” bridge technology, an enhancement that likely would have averted the I-35 bridge collapse and saved lives. The embedded video clip briefly tells the story of the construction process of the new bridge, using a package of tethered sensors that make it “smart.” It also includes the unfortunate and stark footage of the August 1st 2007 I-35 bridge failure.
The video presents an elevation view of the St. Anthony Falls bridge span, including the general locations of its sensors. In this case, the installed monitoring system is not the wireless variety currently in the news but is tethered with cable. The types of sensors in the monitoring package include linear potentiometers, accelerometers, corrosion potential sensors, and temperature gauges. Most of these sensors are focused on the concrete elements of the structure and monitor the movement of expansion joints, as well as the concrete’s temperature, strength (particularly during construction), creep, and shrinkage. The corrosion potential sensors are attached to metal pieces in the bridge deck to warn of advancing corrosion that could affect the bridge’s embedded reinforcing steel. Vibration sensors (the accelerometers) trend any abnormalities that might predict more substantial structural failures. More detailed information regarding the use of this sensor array is discussed in this article, written by DATAQ, Inc., the system vendor.
See also: A Bridge to Everywhere
If you know of any additional “smart” bridges along your daily commute, please let me know with a comment …perhaps we can feature a few of them in future blogs or articles.
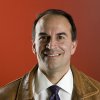
Andrew Kimos
Andrew Kimos completed the civil engineering programs at the U.S. Coast Guard Academy (B.S. 1987) and the University of Illinois (M.S. 1992) and is a registered Professional Engineer in the state of Wisconsin. He served as a design engineer, construction project manager, facilities engineer, and executive leader in the Coast Guard for over 20 years. He worked as a regional airline pilot in the western U.S. before joining the Buildipedia.com team as Operations Channel Producer.
Website: buildipedia.com/channels/operations