Concrete
Concrete in various forms can be dated back to 5600 BCE, where in Serbia the remains of a hut were found with a floor made of a mixture of red lime, sand, and gravel. In the Roman Empire, a concrete made from quicklime, pozzolanic ash/pozzolana, and an pumice aggregate was used. It was very similar to the modern portland cement concrete which was developed in the 1840’s and is currently in use today.
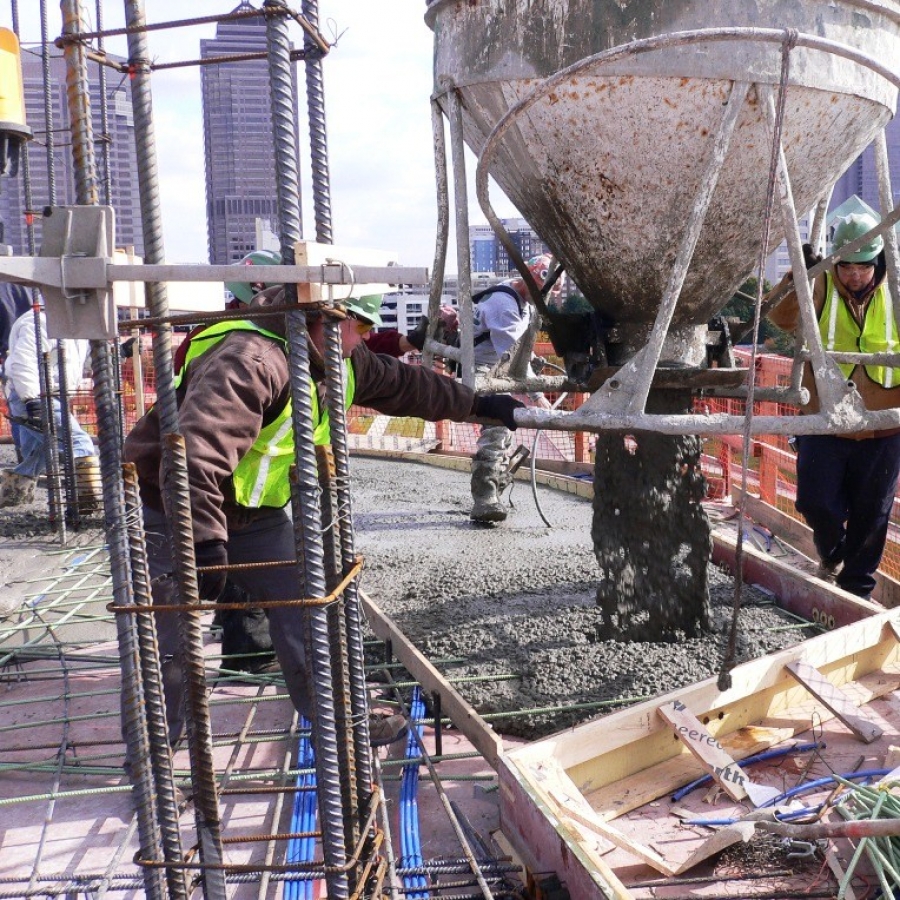
Topic Summary
Concrete has a variety of construction uses including, but not limited to, footings and foundations, both interior and exterior walls, retaining walls, columns, beams, slabs on grade and elevated slabs, stairs, pavements, concrete pipe, mass concrete for dams, structural pre-cast concrete, pre-cast concrete specialties, and decorative items. Concrete is used more than any other man-made material on the planet. As of 2005, roughly six billion cubic meters of concrete was made annually.
When mixing concrete, there are many factors to take into consideration. Depending on the concrete’s structural use, location, and environmental considerations, chemical or mineral admixtures can be used to achieve specific performances.
The strengths of concrete design mixes are normally stated in pounds per square inch (PSI). This can be determined after the concrete has cured for 28 days. The design strengths as stated by a representative Building Code (Ohio Building Code table in this example) are shown in the following chart.
TYPE OR LOCATION OF
|
MINIMUM SPECIFIED COMPRESSIVE STRENGTH (f 'c at 28 days, psi)
|
||
Negligible |
Moderate Exposure |
Severe Exposure |
|
Basement wallsc and foundations not exposed to the weather |
2,500 |
2,500 |
2,500a |
Basement slabs and interior slabs on grade, except garage floor slabs |
2,500 |
2,500 |
2,500a |
Basement wallsc, foundation walls, exterior walls and other vertical concrete surfaces exposed to the weather |
2,500 |
3,000b |
3,000b |
Driveways, curbs, walls, patios, porches, carport slabs, steps and other flatwork exposed to the weather, and garage floor slabs |
2,500 |
3,000b |
3,500b, d |
For SI: 1 pound per square inch = 0.00689MPa.
a. Concrete in these locations that can be subjected to freezing and thawing during construction shall be of air-entrained concrete in accordance with Section 1904.2.1.
b. Concrete shall be air-entrained in accordance with Section 1904.2.1.
c. Structural plain concrete basement walls are exempt fro the requirements for exposure conditions of Section 1904.2.2 (see Section 1909.6.1).
d. For garage floor slabs where a steel trowel finish is used, the total air content required by Section 1904.2.1 is permitted to be reduced to not less than 3 percent, provided the minimum specified compressive strength of the concrete is increased to 4,000 psi.
Assyrians, Babylonians, Egyptians, and Romans all used forms of concrete, but today’s modern designs have required concrete to evolve. Concrete has to be strong enough to withstand the weight and mass of large buildings, huge vehicles, and heavy foot traffic, just to name only a few of the challenges. Pre-cast concrete designs make it possible to pour concrete in a controlled environment, where it is unaffected by climate or temperature, and then transported to job sites for installation. Coloring agents, stamp patterns, and molds create intricate designs, making concrete not only durable but turning the structures into modern art.
What is Concrete?
Concrete is a man-made material composed of aggregates (fine or coarse, usually in the form of sand, gravel, or crushed stone), a binder (usually portland cement, which is made by heating limestone with clay and grinding this product with a source of calcium such as gypsum), water, and admixtures. The strength of the concrete is determined by the water/cement ratio. The workability is affected by the water content, amount of cement paste, and the physical characteristics of the aggregate used. Recycled aggregates from construction, demolition, and excavation waste can also be used as partial replacements for natural aggregates.
Methods and Materials
It is possible to combine admixtures to control for some of the factors that can affect concrete's installation and/or performance. For example, a drop of 20 degrees can double the set time of concrete. A combination of "set accelerators" and "water reducers" could solve this problem.
Supplementary cementing materials may also be used to reduce costs while increasing the concrete's strength, or to influence other concrete properties. These materials include fly ash, silica fume and ground blast-furnace slag (admixtures). While these substitutes can improve what would otherwise be a waste product and create a stronger, more durable product in the long run, it takes them longer to gain strength than portland cements. There are, however, mixes that can set and cure to desired strengths more quickly than normal portland cement mixes. When there is a requirement to place concrete in service in a more timely manner, a concrete mix called "high early" allows for quicker finishing and early removal of slabs. Reducing the amount of water in the mix and/or adding more cement can provide this desired characteristic. The concrete will become less workable and finishing, typically, becomes more difficult. One way to offset this is by adding superplasticizers (admixtures) which will make the concrete easier to work with and can compensate by increasing the slump of the concrete (making it less viscous). Plasticizers are not universally used, however, due to the cost of adding them to the concrete mix.
Cement Substitutes
By-products from other manufacturing or electric generating processes can be substituted for cement. Producing cement uses a great deal of energy, so finding a waste product that can substitute for cement makes good environmental sense. According to Environmental Building News (EBN), as much greenhouse gas is created producing the portland cement used in the U.S. in a year as it is from operating 22 million compact cars in the same year.
- Types of Cement Substitutes: Fly ash, slag, silica fume, and rice hull ash are all types of cement substitutes. To varying degrees, cement substitutes work in two ways. First, they hydrate and cure like portland cement. Second, they are “pozzolans,” providing silica that reacts with hydrated lime, which is an unwanted byproduct of concrete curing.
- Air Entrainment: A significant advancement in the science of concrete was the development of air entrained concrete. Air entrained concrete is recommended and specified in almost all exterior applications and some interior applications. Air entrained concrete has microscopic air bubbles or cells throughout the concrete. It is important that the air cells are distributed as universally as possible. The cells act as expansion chambers for the pressure created when water freezes from a liquid into a solid, creating ice. Without the cells created by air entrained technology, the concrete is more apt to "spall" or "scale off" at the surface. The amount of air entrained in the concrete is typically 5 - 8% of the volume of the concrete.
- Strength: Strength is improved by the substitution of some mineral admixtures for portland cement. Class C fly ash and slag improve strength more than Class F fly ash. In applications where high strength is critical (such as high-rise buildings), silica fume is the cement substitute of choice, resulting in compressive strengths of 15,000 psi and higher.
- Color: Class C fly ash results in a buff-colored concrete; Class F is a darker grey. Slag concrete is lighter in color with high reflectivity. During curing, slag concrete may show a blue-green mottling, called “greening.” However, the color is usually gone from the surface in a week, and its disappearance depends on oxidation.
- Weatherability: Cement substitutes help alleviate permeability and chloride-induced corrosion; de-icing salts can migrate through pores in the concrete, break down the passive protective layer around the reinforcing steel, and cause corrosion that leads to spalling. The pozzolanic action of cement substitutes removes the calcium hydroxide that makes the concrete permeable, and therefore is highly desirable in roadways. A high percentage of fly ash is not recommended for slabs and paving exposed to the weather because of dusting.
- Adobe, Cob, Soil-Cement, and Rammed Earth: Homes made from soil-based materials have been called various names; adobe and cob are terms often used to describe sun-dried clay materials. Rammed earth and soil-cement brick refer to a popular method used today, using a cement additive and pressure to mold the blocks or bricks. Pumice-Crete is a low density and resource-efficient concrete consisting of pumice aggregate, portland cement, and water. It is an economical alternative to conventional building methods and materials because it combines structural strength and insulation in one product. Pumice is a lightweight, volcanic sponge-like rock formed by the expansion of gases while molten lava rapidly cooled.
Environmental Consideration
When pouring concrete, the current weather and temperature should be taken into consideration. In general it is best if the temperature is not below 50 degrees Fahrenheit (10 degrees Celsius) in order to allow for proper curing. In addition to weather and temperature, the location can also affect the concrete. The type of soil, chemicals in the air, exposure to sea water, earthquakes, or exposure to extreme temperature fluctuations may cause the concrete to fail if not mixed properly. Admixtures may be used to compensate for these factors. Supplementary cementing materials can also be used to save energy and dispose of an existing waste product.
Extreme weather temperatures call for special measures when working with concrete. The Portland Cement Association has introduced Hot and Cold Weather Concreting (CD057), a new training program providing an introduction to the effects of hot or cold temperatures on the properties of concrete and the general requirements for producing concrete in hot or cold weather.
Design Basics: Concrete Preparation
First, a limited access area should be set up using barricades or some other method so that the site will not be disturbed once the concrete is poured and before it has had time to cure. There must also be clear access for trucks, wheelbarrows, or pumps depending on how the concrete will be placed. All workers should have on proper safety gear, including boots, gloves, protective eyewear and protective clothing. The thickness of the concrete needs to be determined based on the load it will carry, and the finishing level must be determined. The site needs to be prepared by bringing it to the proper elevation through a process known as grading, which will require the excavation of areas where the finishing level would be too high. The ground must be solid and free from roots and grass. If the soil is too soft, it may need compaction and the distribution of stone or crushed rock over the surface area where the concrete will be installed. Taking the time to prepare the area in advance will avoid problems with the placement of the concrete in the future. The area needs to be measured and staked out, allowing room for forms to be erected around the area where the concrete will be poured. The formwork is what gives the concrete its shape and needs to be braced so that it will not flex or move. Any plumbing, heating or electrical work that runs through the area needs to be in place prior to pouring the concrete. An underlay or vapor barrier may be necessary to prevent water from rising through the hardened concrete. Any need for admixtures should be determined in advance. The type and number of joints (concrete cutting) should be planned in advance of the pour. If steel reinforcing is being used, the mesh sheets or loose bars should be placed. If the surface will be finished using a stamp or other pattern, it should be laid out in advance.
Concrete Applications and Installations
Decorative concrete surfaces are becoming more popular in building design and they are replacing other decorative floor overlays. There are several applications that add visual appeal to both the interior and exterior of structures. In addition to visual appeal, there are also more advanced application methods which compensate for climate, temperature and location issues.
There are several methods for applying a concrete pattern. One of the more traditional, and still the most popular, is exposed aggregate. It is accomplished by either removing the surface mortar to expose the underlying aggregates, or by casting select aggregate over the surface and embedding it prior to the concrete setting. Stamped concrete is also becoming more popular. Patterned or textured mats and templates are applied to the concrete during the finishing process in place of steel troweling. The initial float pass is performed on the fresh concrete and then a release agent is applied (which can be colored) and the pattern is imprinted. Some of the basic patterns include natural stone, rock, wood, brick, and many others in varying shapes and sizes. Saw cuts and joints can also add pattern to the concrete. The saw cuts can be added using an early entry saw or a conventional saw after the concrete has set. Jointing tools can also be used while the concrete is fresh.
In addition to all of the patterns available, there are also assortments of colors and coloring methods that can be applied. Pigments can be added to the concrete mix creating a color throughout the concrete, or added after the concrete is set using stains, tints or dyes on the concrete surface. The greatest range of colors can be achieved if bleached portland cement is used in the original concrete mix. Stains can be either acid or polymer. The acid stains react with the concrete components creating irregular patterns, and tend to have more earth tones, whereas the polymer stains have a broader range of colors. Dyes are either water or solvent based and are very fine pigments that penetrate into the concrete surface. They do not chemically react with the concrete and come in the largest range of colors.
Although aesthetics are important, the quality of concrete is always the primary concern. The ideal temperature for pouring concrete is between 50 and 77 degrees Fahrenheit (10 and 25 degrees Celsius). If the temperature is too high the result could be accelerated setting, a higher water demand (which leads to lower compressive strength), a demand for higher dosages of air-entraining admixtures (for durability in severe climates), and an increased potential for shrinkage and cracking. Some precautions include moistening absorptive aggregates, cooling aggregates and mixing water, dampening the subgrade, and fogging forms before placing concrete, as well as erecting temporary windbreaks and sunshades to reduce concrete temperatures. If the temperature is too low it will extend the setting time and take longer for the concrete to gain strength, which means it will take more time before the forms can be stripped, the joints can be cut, and any load can be permitted on the structure. Some solutions would be: using a higher portland cement content; reducing or eliminating supplementary cementing materials and natural pozzolans (unless required for durability); lowering the air-entraining admixture dosage; adding an accelerating admixture; heating the mix water and/or aggregates; having insulating blankets ready for the curing process; and, ideally, not letting the temperature of the concrete drop below 50 degrees Fahrenheit (10 degrees Celsius) for 72 hours.
In addition to temperature, location can affect concrete quality if it is not prepared properly. Seawater has corrosive effects on concrete. Mechanical damage may occur above the wave surface due to erosion from the waves, the sand and gravel that they carry, or by salt crystallization from water soaking into the concrete and drying. Pozzolanic cements and cements composed using more then 60% of slag as aggregate withstand saltwater better. Acids or sewage can also cause concrete to lose strength. Using limestone as the aggregate will increase the pH, thus counteracting damaging effects. It is important to research your location prior to pouring concrete so that environmental considerations can be made in advance.
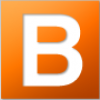
Buildipedia Staff
The Buildipedia research and writing staff consists of dozens of experienced professionals from many sectors of the industry, including architects, designers, contractors, and engineers.
Website: buildipedia.com/