Concrete Reinforcing
The intent of concrete reinforcing is to increase the concrete's strength, and metal reinforcing bars are the additive most commonly used for this purpose. Because of concrete's massive weight and the amount of reinforcing material required to build solid concrete buildings of any significant height, most reinforced concrete is used for horizontal slabs. When buildings are constructed with concrete walls, the buildings are generally limited to a few stories. Reinforced concrete buildings and building components have distinct advantages over other construction methods, including durability, fire resistance, and wind resistance.
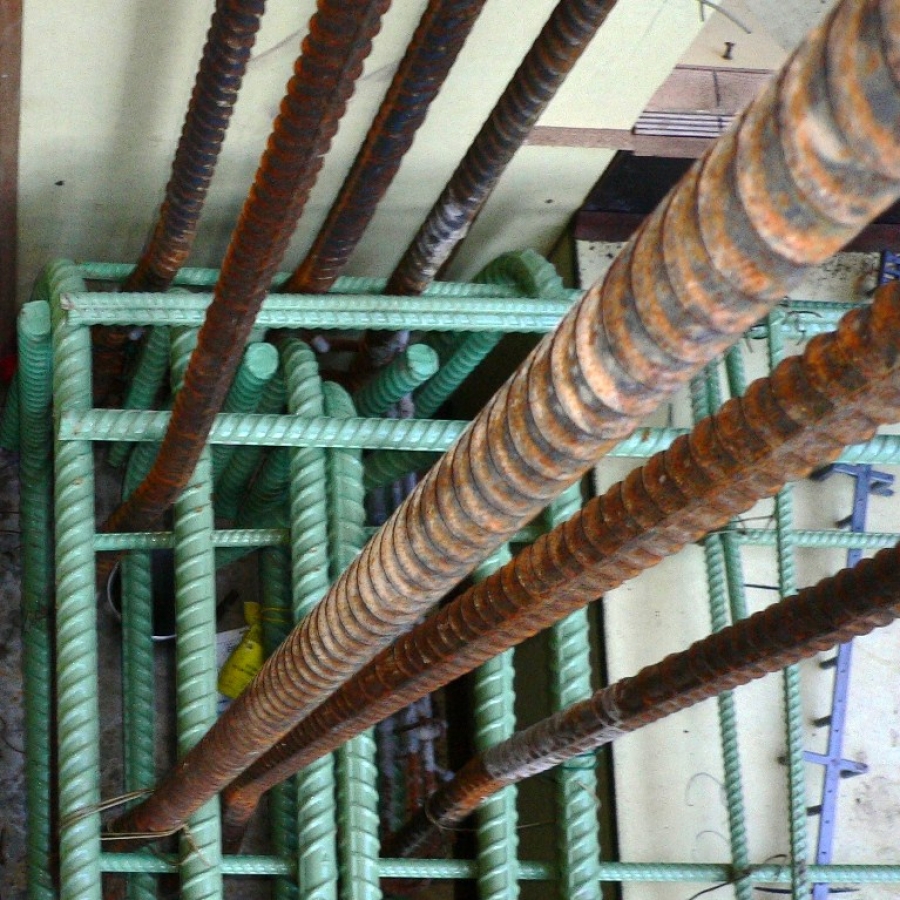
Topic Summary
Standards and Codes
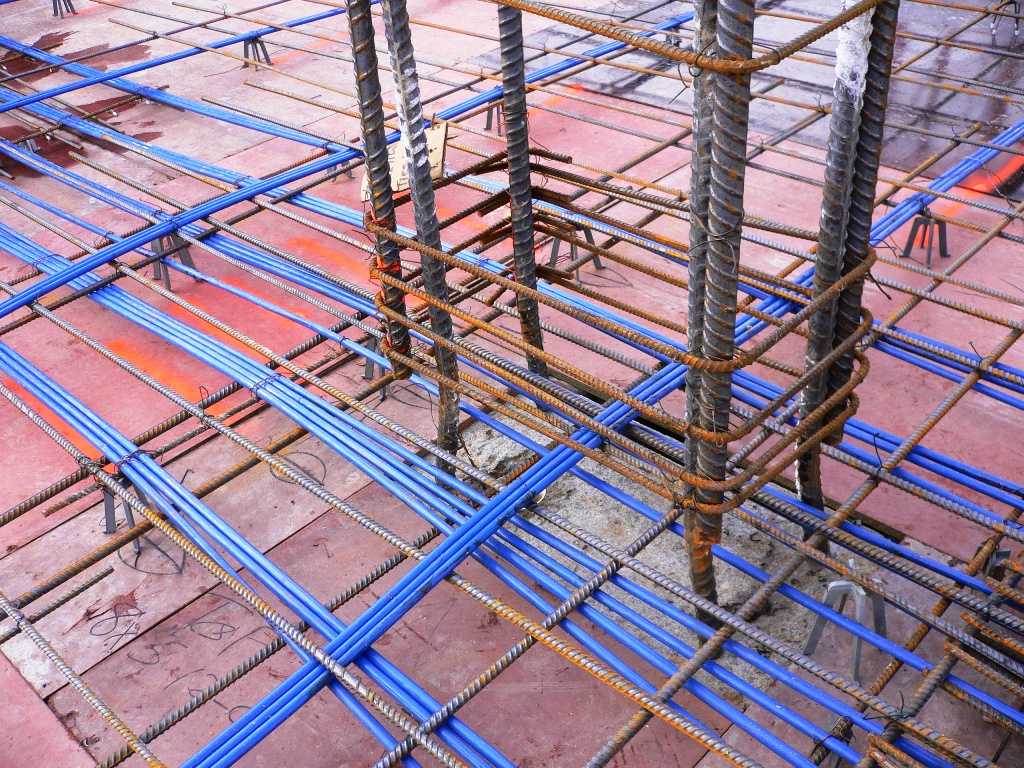
- Minimum Design Standards for Reinforced Concrete: The International Building Code, chapter 19 by ICC
- Reinforced Concrete Shall Comply With: ACI 318 and ACI 318, Section 3.5
- The Welding of Reinforcing Bars Shall Comply With: AWS D 1.4. ASTM Standards
ASTM Standards
- A108-99: cold finished, carbon steel bars
- A184/A184M-05: standard fabricated, deformed steel bar materials for concrete reinforcement
- A974-97: welded wire steel fabric for concrete reinforcement
- A884/A884M-02: epoxy-coated steel wire and welded wire fabric for concrete reinforcement
- A775/A775M: epoxy-coated rebar
- A767: zinc-coated (galvanized) rebar
Without reinforcement, concrete could not be widely used in construction. Concrete is highly resistant to compressive stresses, but requires reinforcing to attain tensile strength, i.e., resistance to bending and flexing. Reinforcement may be provided in several ways: by embedding steel bars (reinforcing steel) or welded wire fabric into the concrete, or by incorporating fibrous materials into the concrete mix. Fibrous materials have been used to reinforce concrete and grout for several centuries, but the emergence of composite materials for this purpose has renewed interest. A variety of steel, glass, and polymeric (plastic) fibers are now available, with each exhibiting unique properties. Pre-stressing and post-tensioning are active forms of reinforcement that take advantage of the inherent compressive strength of the concrete. Steel tendons are used to provide the stress, which may be applied either before the concrete hardens (pre-stressing) or after (post-tensioning). Most pre-stressed elements are prefabricated and transported to the site, which limits their size. The bonded post-tensioning method is used for monolithic slabs in the construction of homes where expansive soils (e.g., adobe clays) may create problems for the foundations. Also, reinforced concrete is the basic ingredient in precast concrete products.
Reinforced concrete is now used extensively in the building industry for the construction of slabs, walls, beams, columns, floor slabs, footings and foundations, pavements, walkways, curbs, and gutters. The use of reinforced concrete has been particularly important in the construction of floor systems, where its design and implementation can be critical to building optimal structures. Concrete reinforced with steel can be aesthetically pleasing and it is economical, reliable, and durable. Determining early-on the most practical method of reinforcement, the proper reinforcement design, and adequate detailing can help to reduce construction costs.
Methods and Materials
The reinforcing bars used in concrete are manufactured from certain grades of carbon steels with high yield strengths, e.g., yield strengths of approximately 500N/mm2. The ductility of the steel bars may also be an important property, since ductile materials tend to absorb greater amounts of energy when deformed. The rebar is usually round, with cross-sections ranging in area from 0.1 to 4.0 square inches, weighing from 3.5 to approximately 14 pounds per foot.
The coefficients of thermal expansion of the carbon steels and concrete are similar, so that internal stresses arising from thermal expansions and contractions are minimized. Furthermore, as the cement hardens it conforms to the surface deformations of the reinforcing bar, allowing stresses to be transmitted efficiently between the two materials. The surface of a reinforcing bar is usually roughened, corrugated, or patterned to enhance the bonding between the concrete and the steel.
In contrast to rebar, steel welded wire fabric is a lightweight reinforcing material with higher tensile strength that is more easily transported, handled, and placed on-site. It can therefore lower costs by reducing manpower and construction time. Welded wire fabric reinforcement is often preferred for the construction of concrete slabs-on-grade and slabs-on-ground. The weight and the size of the welded wire fabric can make it easier to properly place than conventional rebar. Concrete with welded wire fabric provides better control of cracking than concrete without welded wire fabric. The fabric can be readily formed into the shapes required for beams, stirrups, column ties and corner reinforcements.
Exposure to seawater and de-icing salts leads to corrosion of steel reinforcement, resulting in cracking and spalling of the concrete. "Galvanized reinforcing steel" and "galvanized welded wire steel fabric reinforcing" refer to materials onto which a thin layer of zinc metal has been deposited. This coating of zinc affords protection to the steel against corrosive environments. It is an adherent coating that is resistant to abrasion, a property that is beneficial to transportation and on-site handling of the material. An alternative approach for providing corrosion protection is to coat the steel substrate with an epoxy resin, formed from a mixture of the resin, fillers, pigments and flow-control agents.
The addition of fibers to concrete assists in controlling the cracking attributed to plastic shrinking and shrinking from drying. The fibers also reduce water bleeding from the concrete and some fiber types can enhance the resistance to impact and abrasion. Fiber-reinforced concrete can be used for slab-on-ground construction to replace welded wire fabric and has been selected for the construction of base slabs, curbs, stairs, walkways, floor slabs, poured walls and footings. Fiber reinforced concrete can be used in combination with reinforcing bars or welded wire fabric.
Both bonded and unbonded tendons are used in post-tensioning concrete. In the former process, the compressive forces are applied after the concrete has been poured and cured. The steel tendons are located before the concrete is placed, and after the concrete has hardened tension is applied using hydraulic jacks. When the tendons have stretched sufficiently, they are fixed in position and the jacks are removed, transferring the pressure to the concrete. The unbonded post-tensioning method differs from the bonded approach in that each steel tendon has freedom of movement with respect to the concrete. The tension is transferred as the tendons act against the anchors embedded at the perimeter of the concrete slab. The freedom of the tendons or cables allows adjustments to be made as the process is carried out.
The method of pre-tensioning concrete is based upon the development of a strong bond between the steel tendon and the concrete, which facilitates the transfer of the tension. The cured concrete adheres to the tendon causing the tension to be transferred to the concrete as a compressive force.
Design Basics
The design and sizing of reinforcing materials must comply with building codes and properly utilize the strengths of the two materials in composite. Normally the most economical and constructable solutions are selected. Reinforcing materials add cost to concrete construction, thus an evaluation should be completed to determine the quantity of reinforcing required for the volume of concrete. However, it is important to note that mechanical failure of the concrete structure can occur if there is insufficient reinforcing material or if the spacing of the reinforcing bar is too wide. The designation of the reinforcing steel is usually tabulated in a Reinforcing Schedule on the construction drawings.
Preparations
For cast-in-place structures, the choice of reinforcing materials will be stated in the construction drawings, together with details regarding installation and the accessories required. Any rebar, steel tendons, welded wire fabric, galvanized or epoxy-coated rebar, and wire fabric should be clearly labeled and stored in a clean, dry area. Precast units are usually set in place using a crane or other lifting equipment, which should be on-site at the time of delivery of the pre-cast structures.
Welded wire fabric reinforcing material is manufactured and transported in sheets or rolls. Sections are cut and flattened using a roller to allow proper placement. The reinforcing material is placed on support chairs to fix its position and splices or laps are fitted in accord with the Building Code and ACI 318.
Post-tensioning processes typically use 7-wire steel tendons that are located approximately 2 to 3 feet apart and attached to anchor posts. Once the concrete slab has hardened, the tendons are stretched and the elongation applies force to compress the concrete. The amount of post-tensioning depends on the thickness of the concrete used to form the foundations.
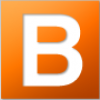
Buildipedia Staff
The Buildipedia research and writing staff consists of dozens of experienced professionals from many sectors of the industry, including architects, designers, contractors, and engineers.
Website: buildipedia.com/