Grouting
Grout is a strong cementitious mix or chemically-setting mix used for filling voids, joints, or cracks in concrete or masonry. There are two main categories of grout: cementitious grout and chemical grout. Cementitious grout has been used in the U.S. since the mid-1800's to create grouted reinforced masonry. This construction is normally used on buildings limited to a few stories. Cementitious grout is also used for embedding reinforcing bars, which increases the amount of load-bearing material in a masonry wall; for filling hollow metal door frames; for repairing cracks; and for connecting pre-cast concrete panels. Chemical grouts are fluid and are used for filling under the bearing plates of columns and machine bases or for injection to fill cracks. Grouts used for tiling, flooring, resin grout, flowable fill, stone restoration, and foundation and slab jacking are examples of more specialized grouts.
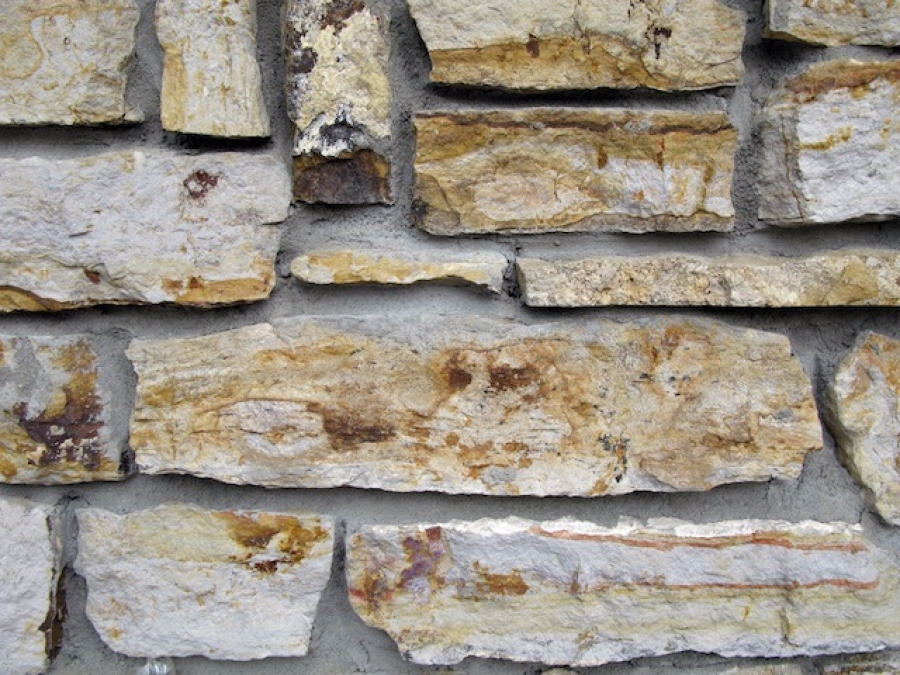
Topic Summary
Cementitious grout is a cementitious mixture of portland cement, sand, or other ingredients, mixed with water to produce a uniform paste used to fill joints and cavities between masonry units. Cementitious grout can include portland cement and cementitious-based non-shrink grouting. Portland-cement grout is portland cement added to fine aggregates and water and pumped or forced into joints, cracks, and spaces as an adhesive sealer or structural fill. Portland-cement grout is used to repair wide cracks. Cementitious-based non-shrink grout contains only natural aggregate and an expansive cementitious binder. Some of its positive characteristics include: high strength, being non-staining and non-shrinking, and being extremely flowable and self-leveling. It has an appearance similar to concrete when cured, and does not contain any added chloride. Some of its primary uses include machine bases of all types, anchor bolts, and column baseplates.
Chemical grout is a grout that consists of solutions of two or more chemicals that react to form a gel or a solid precipitate. Chemical grouts can include epoxy, epoxy-based non-shrink grout, and polyurethane foam repair materials. Chemical grout (such as epoxy grout) can be used to seal cracks in concrete as narrow as 0.002 inches. Some of its disadvantages may include increased cost, limited shelf life, and storage environment considerations, as well as more stringent safety precautions.
Grouting can be used successfully in moist environments, and some grouts are specifically made for underwater installations.
Design Basics
The design considerations for grouting vary according to the type of grouting and the specific use/application. Several books provide specific information on each grout and the basic information for the proper design and application.
- The Practical Handbook of Grouting, published by John Wiley, offers the most comprehensive single-source reference covering all areas of grouting technology.
- The ACI Bookstore offers information on a study and report on the application and use of cement grouting techniques, SP-83: Innovative Cement Grouting.
- Grouting Between Foundations & Bases for Support of Equipment and Machinery is an overview of current practices of grouting for support of equipment and machinery and the materials and installation methods used for the load-transfer material between equipment bases and their foundations.
Preparation
Before grouting, the concrete surface should be properly prepared by chipping, sandblasting, water blasting, or using other accepted methods to remove defective concrete, dirt, oil, grease and other foreign matter to achieve a sound, clean concrete surface. The concrete surface may also be lightly roughened for bonding purposes, but not enough to interfere with proper placement of grout. Remove foreign matter from any steel surfaces that may be in contact with the grout.
In general, the void or area to be grouted must be sealed to keep the grout from leaking out. This is true for masonry wall grouting, crack grouting, column base grouting, or equipment setting. Only dry pack grouting is applied without physical restraint. (See below for a description of dry pack grouting.)
Where the crack face cannot be reached, the backfill material or sub-base material is often an adequate seal. Numerous materials and techniques may be used to seal surface cracks depending on the crack size and grouting pressure to be used. Under normal conditions (not including very low or high grouting pressure) a cement paint or grout seal is used.
For the grouting of voids, the installation of entry ports is required by one of the following methods:
- Drill a hole and insert a fitting (such as a pipe nipple or tire valve stem).
- Bond a fitting flush with the concrete face over the crack (such as a surface port).
- Omit the seal from a portion of the crack. A special gasket device should be used to cover the unsealed portion of the crack and to allow the grout to be injected directly into the crack without leaking.
- Once the vertical void/crack has been cleaned (often by compressed air), it should be sealed.
The final step before applying the grout is to mix it. Cementitious grouts can be mixed at varying ratios from 1:1 to 1:5 parts cement to water. The water/cement ratio should be kept as low as possible to maximize strength and minimize shrinkage. Chemical grouts should be mixed based on the manufacturer’s instructions.
Applications and Installations
There are several different applications and installations for grouting. Examples include dry pack grouting, non-shrink grouting (both metallic and non-metallic), epoxy grouting and polyurethane foam repair materials. All have specific uses, benefits, and drawbacks. Successful grouting requires varying degrees of expertise and installation skills, and requires following written instructions.
Dry pack grouting is a mixture of cement and fine aggregate which has enough moisture for hydration but is dry enough to be rammed into place. Because of the low water/cement ratio of the material, there is little shrinkage. As long as the patch remains tight, it is durable, strong, and watertight. It also has no chloride base or corrosive ingredients. This method should not be used on active cracks. The preparations for dry packing are slightly different than described earlier for non-dry-pack grouting. Before a crack is repaired by dry packing, the portion adjacent to the surface should be opened up to about 1 inch wide and 1 inch deep. After the slot is cleaned and dried, a bond coat consisting of cement slurry or equal quantities of cement and fine sand mixed with water (to a fluid paste consistency) should be applied. Placing of the dry pack mortar should begin immediately. To minimize shrinkage, the mortar should stand for 1/2 hour after mixing and then be remixed prior to use. It should be placed in layers, and each layer should be thoroughly compacted using a blunt tool or hammer. Each layer should also be scratched to facilitate bonding with the next layer. Some of the dry pack method's primary uses include structural baseplates, anchor bolts, precast elements, and honeycombing.
Nonmetallic non-shrink grouting is a nonmetallic cementitious or epoxy-based mix used to fill the gap created between bearing components or base plates and foundation or other supporting elements.
Non-shrink Metallic Grout is grout that has been coated with metal flakes that reflect light. It is internally reinforced with specially processed iron aggregate of exceptional durability under heavy-duty loading. Some of its benefits include being non-shrinking, having no added chloride, and being easy to place at fluid consistency. Some of its primary uses include structural columns, bridge seats, bearing plates, and anchorages. It is virtually non-staining, and therefore is useful in many aesthetic applications.
Epoxy grout is a two-part grout system consisting of epoxy resin and epoxy hardener, specially formulated to have impervious qualities and stain and chemical resistance. One of its benefits is flexibility, which helps to eliminate cracking or bowing due to shrinkage and thermal cycling stresses. Epoxy grout is useful if a crack needs to be structurally repaired and the area around it needs to be as strong or stronger than the concrete around it. This method works best on dormant cracks, and the application of this method may be limited by the ambient temperature. The area should be prepared as described above in preparation. The epoxy should be mixed according to the manufacturer’s instructions. Some of its primary uses include repairing buildings, bridges, dams, and other types of concrete structures.
Polyurethane foam repair materials are similar to epoxy grout. One of the benefits of this product is that it hardens within minutes of injection. This reduces the chances of the material flowing out of an injected crack while still in liquid form. If some does leak out, the foam will fill the void. It is useful if the crack needs to be repaired only to prevent water leakage or if the crack is actively leaking. If there is concern about material leaking out the back of a crack, polyurethane foams should be used.
When grouting small cracks, a manual injection gun may be used. For larger cracks a pump should be used. When injecting epoxy, hydraulic pumps, paint pressure pots, or air actuated caulking guns can be used. The pressure used for injection must be carefully selected based on grout properties, crack characteristics, and the structural integrity of the area being grouted.
If the crack is vertical, the injection process should begin with pumping grout into the entry port at the lowest elevation until the grout level reaches the entry port above. The lower injection port is then capped and the process is repeated at successively higher ports until the crack has been completely filled and all ports have been capped. For horizontal cracks, injection should proceed from one end of the crack to the other in the same manner. The crack is full if the pressure can be maintained. If the pressure cannot be maintained, the grout is still flowing into unfilled portions or leaking out of the crack.
After the grout is applied it needs to cure. For epoxy or polyurethane injection, allow 24 to 48 hours before removing the ports. Once the epoxy has cured, the surface seal should be removed and fittings and holes at entry ports should be painted with an epoxy-patching compound. Cementitious grout can be handled in a manner similar to concrete.
Tools and materials for grouting include a concrete drill, a grout or epoxy injection system, a mechanical mixer or a mixing container and mixing paddles, and a means for cleaning holes and cracks. Normal hand tools such as putty knifes, a margin trowel, plastic sheeting, duct tape, paint brushes and sticks, and either a zirconium grinding disc or a concrete masonry disc are also required. Protective clothing should be worn, such as protective eyewear, gloves, a respiratory or facemask, hearing protection, and boots. A tool such as a power driven saw tooth bit for opening the crack is also required for dry packing.
Most chemical grouts are proprietary products formulated by individual manufacturers. Thus, grout selection for a specific use and its preparation and installation should follow the written recommendations of the manufacturer.
Standards and Codes
- The International Building Code Chapter 19 by ICC states the minimum design standards for concrete.
- Reinforced concrete shall comply with ACI 318 and ACI 318, Section 3.5 and ACI C 504.
- ACI Manual of Concrete Practice
- The International Building Code Chapter 20 by ICC states the minimum design standards for grout for reinforced masonry.
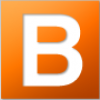
Buildipedia Staff
The Buildipedia research and writing staff consists of dozens of experienced professionals from many sectors of the industry, including architects, designers, contractors, and engineers.
Website: buildipedia.com/