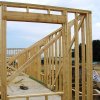
06 10 00 Rough Carpentry
Accoya® Contributes to Sustainable Home in Orange County, California, USA
Accoya Modified Wood Helps Green Home Project In Bid To Achieve Platinum LEED Certification
Structural Insulated Panels vs. Conventional Framing
The all-inclusive, load-bearing design of structural insulated panels (SIPs) offers an energy-efficient, quiet alternative to conventional wood framing methods. In recent years, SIPs have increasingly grown in popularity as builders strive to provide more durable products, use more environmentally sustainable building methods, and reduce costs. According to AMA Research, SIPs are now the fastest growing new building method on the market.
Advanced Framing Techniques
In today’s construction world, where green is the future, it pays to know about building techniques that not only count toward a green building rating but can actually reduce up-front costs. One such method is known as Advanced Framing, sometimes called Optimum Value Engineering (OVE). Advanced Framing takes a good hard look at the way we frame buildings and tries to eliminate wood whenever possible without compromising structural integrity. All of these techniques, when properly executed, comply with the International Residential Code (IRC), but you should check local codes before beginning a project.
Green Building Products: Accoya Wood
Builders looking for a sustainable, environmentally friendly product may want to consider Accoya® wood, which matches or exceeds the durability and stability of the very best tropical hardwoods. Accoya, made from fast-growing softwoods, was introduced to the North American market in 2008. The process used to make Accoya is called acetylation, which has been studied for over 80 years. Accsys Technologies, the makers of Accoya wood, built its production facility in 2007.
Basics of Wood Framing
Wood framing, or light frame construction, is the assembly of dimensional lumber or engineered wood lumber that is regularly spaced and fastened together with nails to create floor, wall and roof assemblies. Wood is the most common material used within the construction industry today.
Glue Laminated Construction
Glue laminated construction (glulam) products are large manufactured structural products used in commercial and residential applications. The idea of laminating lumber with glue for use as beams was originally conceived on job sites in Europe over 100 years ago. This engineered wood product is composed of multiple laminations of kiln-dried, end-to-end or finger-jointed lumber, each bonded together with phenolic resin, a high-strength waterproof adhesive. This process allows for longer and wider structural wood members.
Structural Insulated Panels
Structural Insulated Panels (SIPs) are prefabricated insulated structural elements for use in building walls, ceilings, floors, and roofs. They provide superior and uniform insulation compared to more traditional construction methods (stud or "stick frame"), offering energy savings of 12%–14%. When installed properly, SIPs also provide a more airtight dwelling, which makes a house more comfortable and quieter.
Heavy Timber Construction
Heavy timber construction is a building method that uses large, rustic, heavy sawn timbers or structural glue laminated lumber that is joined together with traditional mortise and tenon joinery or modern metal joinery. Also known as post and beam construction or mill construction, timber framing in floor and roof assemblies dates back to the beginning of civilization. The first completely self-supporting timber frame structure is believed to have been constructed during the 10th century. Developed since that time, the building method was brought to North America in the seventeenth century by European settlers.
Rough Carpentry
This topic covers information related to the design and construction of wood framed structures. Information includes both methods and materials for the erection, connection, joining, anchoring, and blocking of framing.
Shop Fabricated Wood Trusses
Shop-fabricated wood trusses are manufactured engineered products in which the chords and webs are made from wood and connected with metal connectors. The simplest form of truss has a horizontal bottom chord and top chords that form the shape of a triangle which offers support and stability for a roof and roof loads. More complex truss shapes have angled bottom chords and mutli-angled top chords.
Parallel Strand Lumber
Parallel strand lumber is manufactured from long strands of wood veneer that are laid parallel to one another and adhered. PSLs are commonly installed as columns, beams and headers in concealed wall spaces where significant bending strength is required to support loads from above; however, they can also be attractively installed as as an exposed finish material.
Laminated Veneer Lumber
Laminated veneer lumber is a shop fabricated structural wood, composed of wood veneers which are adhered together. Laminated veneers were first developed in the 1940s for aircraft parts. Laminated veneer lumber (LVL), which is a structural composite lumber (SCL), was first produced in the 1970s in response to growing environmental pressures and government regulations. It is an environmentally friendly product that efficiently utilizes wood fibers from smaller trees.
Shop Fabricated Structural Wood
Also known as engineered lumber, shop-fabricated structural wood is manufactured from wood materials or a combination of wood and metal for use in specific structural applications. Shop-fabricated wood is typically used as beams, columns, joists, trusses and other structural members. Types include Laminated Veneer Lumber (LVL), Parallel Strand Lumber (PSL), Wood I-Joists, Metal-Web Wood Joists, Rim Boards and Shop-Fabricated Wood Trusses.
Underlayment
Wood based underlayments are panel or sheet materials that are used between a structural subfloor and a finish floor surface. Also known as overlayment, wood panel materials are commonly used under resilient tile or sheet floors. They can also be used under adhered carpet or other nonstructural flooring as well.
Subflooring
Subflooring is the structural component of a building that provides rigidity to the floor structure, supports live loads, and serves as the surface to which floor finishes can be applied. Wood subflooring is installed in all types of structures, including timber, platform, and balloon framed. It can also be used in special applications such as radiant heat, floating, raised, or sprung floors. Common types of wood subfloor include individual wood boards and wood panels.
Insulating Sheathing
Commonly wrapped around the outside of a structure, insulating sheathing is popular today because of demanding energy codes. Insulating sheathing is a foam insulated board material that reduces energy consumption. It does not have any structural ability and it requires additional lateral bracing to resist seismic and wind loads. Common types of insulating sheathing include polyisocyanurate, molded expanded polystyrene and extruded expanded polystyrene.
Sheathing
Sheathing is the board or panel material used in floor, wall and roof assemblies of both residential and commercial construction. The most basic function of sheathing, in any application, is to form a surface onto which other materials can be applied. There are several types of sheathing, each having a specific function based on its application.
Wood Patio Decking
Wood patio decks are outdoor living spaces that are built above ground. While they typically adjoin a structure, such as a home, they can also be built as a boardwalk or be atop a building as an observation deck. The structure of a wood patio deck is commonly framed with treated lumber. While a number of different types of wood, including softwood, hardwood, domestic or tropical wood, can be used for the top surface deck, each has it's own advantages and disadvantages.
Wood Decking
Wood decking is created using structural boards or planks and attaching them to joists, beams, rafters, or trusses to form a floor or roof surface. Similar to sheathing, the boards act to provide lateral support to the structure and carry the live and dead loads from above to the floor or roof structure below.
Treated Wood Foundations
Treated wood foundations are load-bearing, pressure-treated wood framed walls, used below grade to support light frame construction. Treated wood foundations are commonly called Permanent Wood Foundations or All-Weather Wood Foundations. Since being developed in the 1960s, this unique building system has had its skeptics; however, it has proven to be a durable building system in thousands of physical applications. Treated wood foundations have undergone extensive research, analysis, and testing by several highly respected organizations within the building construction industry. They have been approved for use by model building codes, many state and local building codes, federal agencies, and by lending, warranty and insurance institutions. A treated wood foundation, when installed, waterproofed, and drained properly, and used in conjunction with other waterproof materials, is a viable alternative to poured concrete or concrete block foundations.
Pole Construction
Pole framing or post-frame construction is a simple, cost effective durable design that was developed during the 1930s. Originally constructed with round utility poles, today's pole buildings utilize laminated columns or square posts. The poles or posts are joined to create a building frame that siding is attached to and rafters are rested upon and secured to. Pole construction has commonly been used to build garages, agricultural and equestrian structures, and airplane hangers, but can also be used in the construction of low rise commercial or residential structures.
Log Construction
Log construction refers to a building technique in which a structure is built from logs that have not been milled into conventional lumber. Log buildings are formed by horizontally stacking logs and interlocking their ends with notches. The origin of this type of construction is uncertain, but it is believed to date back to Northern Europe during the Bronze Age. When Europeans settled in America during the 17th and 18th centuries, they utilized this knowledge of handcrafted log construction to create shelter. In 19th century American politics, log cabins came to symbolize humble beginnings, since no fewer than seven U.S. Presidents were born in log homes. Throughout history, log construction was used for homes, churches, schools, barns, mills, commercial buildings, and outbuildings. Typically built in rural settings, this rustic architecture style can be built in any climate. Today log construction can be seen in elaborate homes as well as in simple cabins, built from handcrafted or milled logs, with different styles and options.
Heavy Timber
Heavy timbers are a type of lumber that is differentiated from dimensional lumber by having minimum dimensions of 5 inches. Timber framing consists of joining heavy timbers together with pegged mortise and tenon joints, scarf joints or lap joints. Wood members of heavy timber framing are commonly known as post, beam, jetty, truss and brace. Historically, heavy timbers were hewn with axes or hand sawed. Today, CNC machines have modernized what was once a hand craft, allowing the industry to grow due to greater affordability of products and shorter lead.
Structural Panels
Structural panels are energy efficient, composite panelized systems that are manufactured assemblies used in residential and light commercial structures. Types include structural insulated panel systems (SIPs) or stressed skin panels and cementitious reinforced panels. Used on roofs, walls and floors, structural panels can reduce the time it would take to complete a building envelope with standard materials. Structural panels offer various R-Values, weather resistance, fire retardation, and has the ability to meet extreme structural requirements.
Mechanically Graded Lumber
Mechanically graded lumber is lumber that has been tested and evaluated by a machine rather than by visual inspection. While most lumber is visually inspected and graded, machine grading is a more efficient volume service and creates cost-competitive products, while differentiating the higher strength lumber materials. It is commonly used to deliver materials for more demanding applications. Two types of machines are used to grade lumber, machine-stress rated (MSR) lumber and machine evaluated lumber (MEL) machines.
Engineered Wood Products
Engineered wood materials are manufactured products that utilize strands, particles, fibers, and veneers of wood to produce a range of different types of products. Readily available at lumber yards, these products are cut to length in the field, similar to dimensional lumber. The application of engineered wood products is also similar to that of dimensional lumber; however, each offers its own performance and manufacturing advantages. Engineered wood products also have some disadvantages in comparison to dimensional lumber. They have less fire resistant, require more energy to manufacture, have adhesives that can potentially release toxins into the environment, and are prone to moisture damage. Engineered wood products are often used as columns, beams, girders, joists, purlins, rafters, studs and bracing.
Wood Framing
Wood framing, or light frame construction, is the assembly of dimensional lumber or engineered wood lumber that is regularly spaced and fastened together with nails to create floor, wall and roof assemblies. Wood is the most common material used within the construction industry today.