Another Successful Lean Delivery Project: The Temecula Valley Hospital
Upon first blush, the term “Lean Construction” seems to lack the hype usually associated with the latest and greatest, best and brightest product of construction firms interested in getting the attention of their clients, who always want to save money and receive greater value in the buildings. The relentless quest for ways to improve the often provincial construction processes at work for projects from the large to the small, from the simple to the complex. Indeed, the construction industry is haunted by the constant beckoning of high-tech solutions; in most other primary industrial arenas, factory lines, supply chains, and sophisticated “back office” functions have created greater efficiencies and much better products.
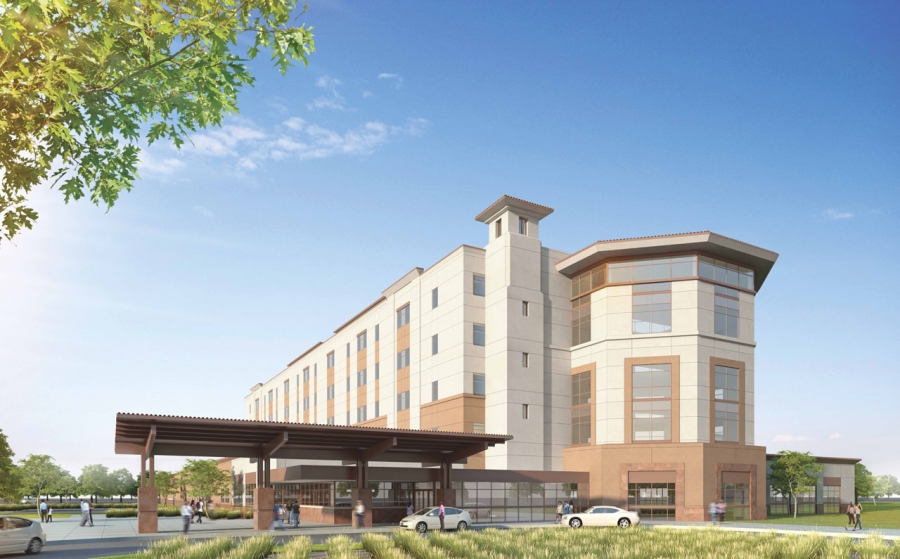
Going Lean
Upon close inspection, the adoption of Lean principles and their implementation at every point in a building project have the potential of making vast improvements in the quality, value, efficiency, usability, and sustainability of our new and remodeled buildings. Learning about Lean Construction provides a pleasant respite from marketing hype and the claims of value made by different brands; the Lean Construction process includes a shared value system found in many open-source, non-proprietary, non-trademarked, commonly held knowledge systems from which we all benefit.
"True to following the principles of Lean Construction, I immediately halted design development on a $150 million hospital project, telling the design and construction team that we have to change the way we look at things, and that that has to start happening today.” Bill Seed, Staff Vice President for Design and Construction for Universal Health Services
On the ground, the shared-values workflow espoused by Lean Construction can be found working well in what workers on a Temecula, California, hospital design and construction project call “The Big Room.” This is not a trademarked name for some oversized space in which to hold yet another series of time-sucking meetings; it is instead the name for the skunk works for the development of ground control for a new health care facility, the Temecula Valley Hospital. Projected to cost half of what a typical acute care facility in California usually costs, the Temecula Valley Hospital also (and perhaps more importantly) promises to deliver much healthier, more positive outcomes for patients and their caregivers. Bill Seed, the Staff Vice President for Design and Construction for Universal Health Services, the owner of the new five-story, 140-bed Temecula Valley Hospital, tells how he came to see the value in Lean Construction. “After sitting down for lunch with one of the guys from Sutter Health and hearing about Lean Construction and reading 'The Toyota Way' at breakfast the next day, I went home and, true to following the principles of Lean Construction, I immediately halted design development on a $150 million hospital project, telling the design and construction team that we have to change the way we look at things, and that that has to start happening today,” Seed says. After a lot of work and with the help of a Lean Construction coach, the Temecula Valley Hospital project team adopted Integrated Process Delivery (IPD) to contractually deliver the Lean Construction process. The team based their approach to Lean Construction on the famous Toyota Production System (TPS), which has two main principles of constant improvement and respect for people's work. These two principles establish the foundation for team work and project flow. Seed used the format provided in "The Toyota Way" by Dr. Jeffrey Liker and explains, “Now, four years later, I have over a dozen IDPs in the works, and the 12 Lean [Construction] completed projects (of 27 underway) have beaten budget and schedule and delivered enhanced profits.”
Likewise, Lean, when boiled down to its essence, is all about preserving value with less work, an obvious choice for any enterprise dedicated to adding value to whatever is being produced. Toyota's view is that Lean processes do not involve just the methods of production but also the reduction of three types of waste: "muda" ("non-value-adding work"), "muri" ("overburdening"), and "mura" ("unevenness"). Muda was originally split into seven types (which have been expanded), and reviewing the seven muda certainly brings to mind thoughts of how they certainly make a project less successful. They are Transport, Inventory, Motion, Waiting, Overproduction, Overprocessing, and Defects.
All-Inclusive, from Start to Finish
Another major benefit of Lean delivery is the shared commitment of an all-inclusive team that is involved from start to finish. Typically using the IPD process and contracts authored by the California AIA, the Temecula Valley Hospital project team also found a way to incorporate Lean principles into financial performance: beating established and fully endorsed project schedule and budget goals means shared profits for everyone involved. According to architect Steven Wilson, Principal-In-Charge for HMC Architects, the designer for the 178,000 sq. ft. Temecula Valley Hospital, “In negotiating our contract for services, UHS brought the Lean delivery system into how we’re compensated, too. Based on an agreed upon, validated cost estimate for the work, the DPR–Turner Construction team agreed to deliver at that cost and a certain schedule. If we deliver at that price, we get rewarded. For every dollar saved by wasting less, we share that cost savings. If we go over the cost, we stand to lose. The owner guarantees their labor, and we agreed to put our profit potential at risk. So it sets up a scenario where you have an incentive to hit the target, to work harder to save money. It guarantees certain behaviors, where nobody’s protecting their own costs; everyone is protecting everyone’s cost. It’s a tough, very open process, but it’s working."
Another specific delivery method that represents a major improvement in the project delivery process is described by architect and HMC Architects Senior Project Manager Ward Thompson: “Part of our lean journey is that our documents include shop drawings as part of documents, provided concurrently with our drawings, which should insure a much smoother process. In some cases the trade partners are doing the drawings. We’ve set up the process so that the trade partner is providing their respective documents. The MEPs have hired engineers to put their drawings together and submit to us for inclusion. We certainly don’t rubber stamp them; we’ll take the documents, review them, and add them to our set. It goes a long way to eliminate waste. It also reduces my design costs and our overall risk profile. We still review the shop drawings just like any other job, and there are still massive amounts or coordination still necessary, but the process works much better for everyone involved."
Maintaining a Collaborative Approach
Although building savings will be significant, the operational efficiencies will be the primary source of savings over the life of the hospital, using the Lean delivery process." Bill Seed, Staff Vice President for Design and Construction for Universal Health Services
George Zettel, with the DPR–Turner Construction team, agrees with Wilson's and Thompson’s assessments. “Not only do we feel that we’re going to meet our target cost estimate, we’re going to deliver one of the lowest-cost new hospitals in California. The California Hospital Association has costs averaging $2 million per bed. We’re on track to produce the Temecula project at roughly half of that. We’ll be really happy if we meet that.” Zettel also mentions that he has encountered some reluctance from team members who aren’t familiar with Lean processes. “As with all things that are new, there’s a natural hesitation in changing the process. But it doesn’t take long for most team members to find that working in a collaborative environment where no one needs to protect their turf [so] that you don’t even think twice about asking a question with someone in the room, feeling safe and not threatened. It’s like everything; every individual adjusts to change at a different pace. Some people can go from first gear to third pretty quick; others have to go first to second to third.” Zettel also proudly mentions another attribute in the Temecula Valley Hospital design that not only provided considerable savings in wasteful project square footage and fire protection needs but also improved the functionality of the critical care unit. “Most California hospitals are designed in part to maximize the relatively quick review by local permit agencies prior to [the] typically onerous, time-consuming review by California’s Office of Statewide Health Planning and Development (OSHPD). The design–build team “swarmed” around the problem of time wasted in the permit review process and decided to submit the entire facility to OSHPD, forgoing the need for local review entirely. When consequently relieved of the need to meet both agencies' requirements, the team then experienced the unforeseen consequence of having to provide far less circulation space, previously provided only to accommodate the designation of room types by the two review agencies.
Seed confirms that cost, effort, time, and operations efficiencies were gained, explaining, “We were also freed up to do a better job at creating the Consolidated Treatment Unit (CTU) where diagnostic services and other patient needs are met with the patient remaining in one place, with services brought to them, not worrying about the typical silo-based, departmental orientation of typical hospitals. Although building savings will be significant, the operational efficiencies will be the primary source of savings over the life of the hospital, using the Lean delivery process. We’re even choosing our staff for the new facility based on their acceptability to the teamwork and commonly held objectives of the hospital that Lean espouses. The benefits of this will accrue back to the hospital in better service, healthier patients, and a happier staff.”
In all of the interviews for this article, one common factor of the success of the Temecula Valley Hospital project arose: “The Big Room,” where weekly meetings are held with everyone in attendance, where timely issues and problems are brought to bear in this Toyota-type “kaizen” setting by individual team members for a collective “pull” toward a solution and corresponding course of action. Indeed, a “Pull Plan” is displayed, outlining issues and their resolutions, for all to carry forward.
As an architect who has long appreciated collaborative work in design–build disciplines, I nonetheless was hesitant about the seemingly harsh, relentless pursuit of absolute perfection that the Toyota system seems to espouse, thinking that another Japanese philosophical view, Wabi-sabi, was being totally ignored. Not easily translated, Wabi-sabi means the aesthetic centered around flow and beauty that is “imperfect, impermanent, and incomplete” and seemed to have no place in the efficient, “less waste” oriented “kaizen” system. Wabi-sabi celebrates the quirks in the process of building objects as a reflection of its ultimate imperfection. Upon learning more about Lean, however, I have seen that the two philosophies are indeed quite compatible and synergistic, as the team leaders involved are quick to profess that constant work is involved in not only solving problems, but living well with their solutions.
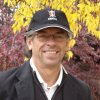
Morey Bean, AIA, LEED AP
Colorado's 1999 Architect of the Year and Vice Chair of the Boulder Chapter of the Urban Land Institute, Morey’s experience includes the successful development of the Colorado Architecture Partnership, an architecture firm dedicated to sustainability and green building. Morey was appointed by the Chief Architect of the GSA to the National Register of Peer Professionals. He serves as a ULI Service Advisory Panelist and was a charter member of the Colorado Chapter of the USGBC and past president of the Colorado South Chapter of the AIA. He is a construction litigation services expert witness, land development analyst and sustainability strategies consultant.
The author was honored by the Colorado Component of the American Institute of Architects as their Architect of the Year in 1999 and is on the Roster of Neutrals for the American Arbitration Association (AAA), providing dispute settlement for the design and construction industry.
Website: www.cyberarchitects.com