Pervious Pavement: Pavement That Leaks Like a Sieve, Part 2
Contractor to Contractor: In this second of a two-part series, contractor-turned-homebuilder Fernando Pages Ruiz shares his knowledge on how to choose a mix, prep the site, and install porous pavement.
Although a blended, high-course aggregate/low-fines concrete (a concrete blend of Portland cement, 3/8" or pea gravel aggregate, and little to no sand) is a simple concept, the logistics of it are far from simple. For this highly porous concrete to provide a durable surface, conditions have to be almost perfect. The concrete requires an exact proportion of aggregates and water, special chemical admixtures, proper mixing during delivery, and expert placement. I recommend that if you decide to use pervious pavement in one of your projects, don’t do it yourself. Hire the very best paving contractor in your area and work with the largest and most sophisticated ready-mix supplier. Pervious pavement is not so much a concrete product as it is a paving system, including soil, sub-grade, and, of course, the mix.
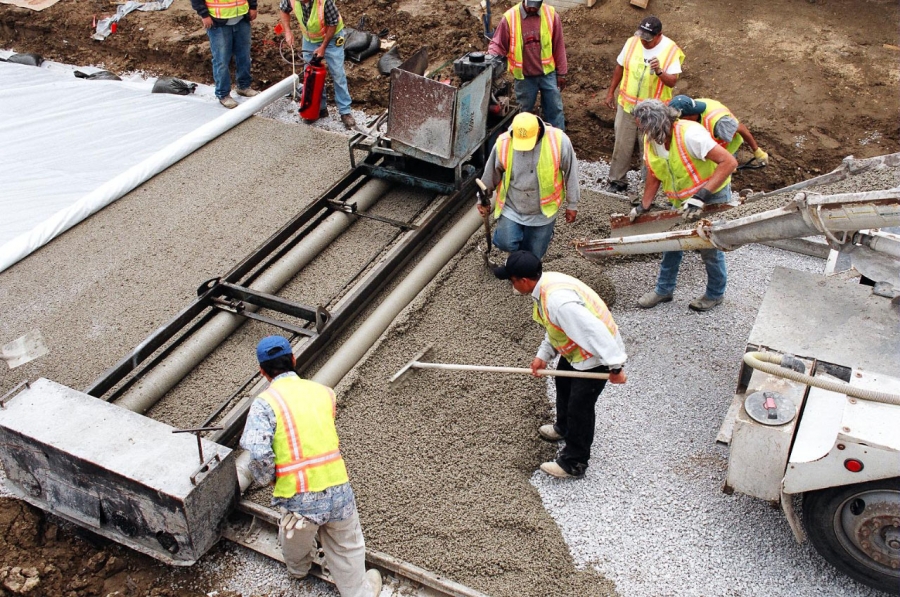
Sub-Grade Prep a Crucial Concern
Because water drains through pervious concrete, it must have somewhere to go. On sandy soils, pervious pavement can sometimes be laid on grade. Most soils require a gravel bed at least 6" thick to act as a drainage plane, holding stormwater as it slowly percolates into the soil. If the soil is high in clay, and/or the soil freezes in winter, you must make sure that any moisture in the concrete will drain immediately; to achieve this, you will have to consult an engineer. In my applications in Lincoln, Nebraska, where the soil is both clayey and freezes, I typically overexcavate the sub-grade by 12". Next, I roll out a layer of non-woven geotextile against the soil to prevent the gravel bed from becoming silted with mud and then add 10" of clean, lightly compacted No. 57 stone (1 1/2" to 3/4" crushed limestone). For insurance, I like to bed-in two or three rows of French drains connected to the nearest storm sewer system; if unusually high precipitation were to cause the thick gravel bed to flood, the storm sewer serves as an emergency overflow valve.
Pervious concrete pavement works a lot like plain gravel; with about 20% of its area made of voids, water penetrates its surface like a sieve. Unlike gravel, pervious concrete also has the advantages of conventional pavement, providing a stable, maintenance-free surface for automobiles, garbage trucks, and, in some areas, the occasional snowplow.
Conventional concrete is always pitched to drain, but it’s important that the gravel bed under pervious concrete remain level to maximize water retention and percolation into the soil. In some cases, this can be an advantage; sometimes it’s difficult to establish water-shedding over a large span of concrete. In one location where I used pervious pavement, a 400' long alley with very little wiggle room for sloped drainage, I poured the alley low and level to drain surface flows from adjacent driveways and lawns, not out to the street, but down into the soil.
A Climate-Suitable Mix
A typical yard of pervious concrete contains pea gravel, six or seven sacks of Portland cement, and water in a ratio of 0.25 to 0.30 (about one-third drier than standard concrete). Because of the low water content, pervious pavement cannot be pumped. It’s difficult mix to work with, it does not pour out of the truck or spread easily, and its high porosity allows air to get in and evaporate moisture quickly (hydration), making it necessary to place, finish, and cover a pour within 20 minutes. To combat these characteristics, your concrete designer will have to add chemicals to slow hydration, stabilize the mix, and provide a slightly longer working time.
Placing pervious concrete requires a well choreographed operation, given only a 15-minute window form the moment the concrete hits the ground to when it’s finished and covered with polyethylene for curing.
In my area, the admixtures include air entraining agents (chemicals that add microscopic air pockets to the cement paste so that moisture has a place to expand without damaging the concrete) to prevent cracking in freezing temperatures, water reducers, and viscosity modifiers to add workability. The objective is a practical mix that is “easy” to place and yields a pavement with 15% to 20% void structure (resembling a rice cake). Your ready-mix company may decide to add a small percentage of fines, usually fly ash (a recycled material derived from coal-burning power plants), to add compressive strength, so your concrete surfaces won’t crumble over time.
Proper Placement and Curing
Pouring pervious pavement demands a highly coordinated effort, a lot like a NASCAR pit stop. Typical challenges include getting the dry mix out of the truck and down the chute, difficulty spreading and striking a virtually zero-slump mix, and then a short working time of 15 minutes or less. It’s important to have enough manpower and for everyone to understand their specific job.
A vibratory screed followed by a roller consolidates the mix; no floating, steel troweling, edging, or control joints are necessary (unless you want edging and control joints for aesthetic reasons). The money saved in labor allows you to pour more square feet in a day and can offset the cost of added sub-grade construction.
It’s a dramatic moment when the dry, silver, metallic paste makes its slow course down the chute. One worker directs the chute while another worker forces the stiff mix down with his hand or shovel. The concrete spills to the ground in a mound as the crew rakes and shovels – a stiff lump and hard to spread, like heavy, damp gravel. Then, to level and strike the mix, you’ll need a mechanical vibratory screed, set 1/2" above the surface. Instead of floating and trowelling, consolidate the pavement in one pass with a steel pipe roller. The surface profile is not critical when finishing pervious pavement. The dimples and dips will not become bird-baths – imperfections become invisible in such a rough surface. On the other hand, it’s important to avoid overworking the surface, which would seal it and therefore defeat the purpose. Strike, screed, and roll are the only steps needed.
A cylinder of pervious concrete with a compressive strength of 3,000 psi (20,684 kPa) allows the passage of nearly 18 gallons of water per minute per square foot.
Immediately after compacting with the steel roller, fog the concrete with a curing compound (I like C2 Products soybean-based curing compound because I am a green, Midwestern builder) and then cover the surface with polyethylene sheathing, all within 15 minutes of placement. With a highly porous structure and very low water content, moisture can evaporate quickly from pervious paving, compromising the cure. Improperly cured concrete is the chief cause of pervious pavement failure. You cannot spray water on the surface to slow hydration, because this would cause the cement paste to settle along the bottom, leaving an impermeable layer below and a lean, crumbly crust above. The plastic sheathing, sealed between laps with duct tape and weighted along the edges with sandbags, must remain in place for seven days. Inspect it daily and repair any tears. After removing the polyethylene, allow the concrete a full 21-day cure before permitting vehicle traffic.
Immediately after compacting with the steel roller, fog the concrete with a curing compound.
Although the process might sound complex and exacting, it’s also very efficient. My paving contractor installed the 400' long, 14' wide strip shown in the photographs illustrating this article in about four hours. No floating, finishing, edging, or cutting required. Once a contractor has developed expertise in working with pervious pavement, the lower labor expense can result in an economical and profitable niche. As demand grows, those with the requisite experience will have the first-mover advantage. The National Ready Mixed Concrete Association offers a well-written brochure if you want to learn more, and the American Concrete Institute offers the ACI Manual of Concrete Practice, 522R-10 Report on Pervious Concrete. Many state concrete aggregate associations offer a pervious concrete certification.
For more information today, and a list of certified pervious concrete installers in your area, go to www.perviouspavement.org, a website of the National Ready Mixed Concrete Association.
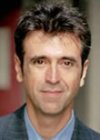
Fernando Pages Ruiz
Homebuilder, developer and author Fernando Pagés Ruiz builds in the Midwest and Mountain States and consults internationally on how to build high-quality, affordable and energy-efficient homes. As a builder, his projects have numerous awards including the 2008 “Green Building Single Family House of the Year” and the 2007 “Workforce Housing Award” from the National Association of Home Builders. In 2006, the Department of Housing and Urban Development's PATH project chose him to build America's first PATH Concept Home, a home that is affordable to purchase and to maintain while meeting the criteria of LEED for Homes, ENERGY STAR, MASCO Environments for Living, and the NAHB's Green Building standards. A frequent contributor to Fine Homebuilding and EcoHome magazines, Pagés is also the author of two books published by the Taunton Press: Building an Affordable House: A high-value, low-cost approach to building (2005) and Affordable Remodel: How to get custom results on any budget (2007).
Contact Fernando on facebook or by way of his website buildingaffordable.com.