Is The Construction Submittal Process Really That Important?
In early 1979, the fabricator and installer for the atrium steel of the new Kansas City Hyatt hotel proposed changes to the connection details for the support of the skywalk system. The original design was thought to be expensive to manufacture and problematic to install. The engineer responded by providing preliminary sketches of the fabricator's proposal without performing basic calculations. These sketches were returned to the fabricator, who assumed these to be the final and approved shop drawings. The revised and ill-fated connection detail was put into production and installed. In 1981, the Kansas City Hyatt skywalk collapsed, causing the deaths of 114 people and injuring more than 200. The ensuing investigations concluded that the fault lay in the engineer's failure to properly review shop drawings and provide adequate communications between the structural engineer and the fabricator of the structural steel for the atrium and skywalk.
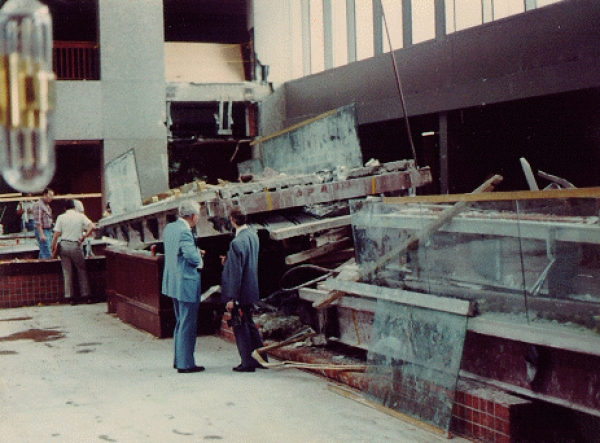
The Missouri Board of Architects, Professional Engineers, and Land Surveyors convicted the engineers who had signed off on the final drawings of gross negligence, misconduct, and unprofessional conduct in the practice of engineering; they all lost their engineering licenses in the state of Missouri. While the engineering firm itself was cleared of criminal negligence, it was banned from practicing as an engineering firm. "The Hyatt Regency Walkway Collapse" presents a complete, detailed chronological timeline of the skywalk failure and the events that followed.
Granted, this is an extreme example of the potential for catastrophic results when the shop drawings, or any portion of the submittal process, is not conducted with diligent professional care and judgment. The construction submittal process poses risks for all parties involved, and to reduce these risks, this process must be carefully monitored and managed. When problems are not managed during the submittal review process, this can lead to incorrect product installations, construction delays and defects, and other costly mistakes as well as personal injury. Risks result both from errors in professional judgment and from failure to maintain a highly organized, efficient, and timely review process.
Shop Drawings are not Contract Documents
It is important to understand that changes made in a shop drawing or submittal do not modify the requirements reflected by the drawings and specifications without an approved change order. Shop drawings do not become contract documents. Until the contractor specifically indicates changes or deviation from the contract documents in shop drawings and an approved change in the work, change order or a construction change directive is issued by the architect, the contractor is required to conform to the approved contract documents. Submittals are not a means for requesting product substitution. If an item or product is to be considered for substitution, it must first be submitted for review and approval prior to submitting shop drawings. Final compliance with the contract documents is ultimately the responsibility of the contractor. The change in the shop drawings and the assumption it was an approved change to the contract documents was a leading problem with the skywalk collapse mentioned earlier.
Section 3.12.4 of AIA Document A201-1997 states: “Shop drawings, Product Data, Samples, and similar submittals are not Contract Documents. Their purpose is to demonstrate the way by which the Contractor proposes to conform to the information given and the design concept expressed in the Contract Documents for those portions of the Work for which the Contract Documents require submittals…”
The Process
The submittal review process provides a critical check-and-balance during the construction phase. This is done to ensure that the end result conforms to the design intent reflected in the architects’ documents, which also reflects the owners’ expectations. During contract negotiations, it is recommended that the contractor, owner, and architect discuss and clearly understand the roles and expectations of everyone involved with the submittal process.
The process is relatively simple and well defined by AIA Document A201 General Conditions of the Contract for Construction. However, the process can be daunting, time consuming and tedious, to say the least. For the process to succeed and be efficient depends on each member of the team performing responsibly. Once the general contractor secures contracts with subcontractors and vendors, they begin to plan and coordinate the shop drawings and sample submissions schedule in a logical sequence, with prioritization given to long lead items. All these submittals must also comply with the project’s construction schedule. The approved submittal schedule, as developed by the contractor, is distributed to all members of the team. This will allow the architect to schedule necessary resources as the submittals start to roll in.
The general contractor is required by the contract to review and approve all submittals first prior to distributing them to the architect. Should the architect receive submittals not reviewed by the contractor, they should be returned to avoid any later issues. Also, if the architect receives a submittal package that clearly does not meet specifications, it should be return to the contractor as a resubmit.
As defined by AIA A201-1997, section 4.2.7, the role of the architect is limited to reviewing submittals for general conformance with the design concept expressed in the construction documents. The architect and engineer's review does not constitute approval of safety precautions, or any construction means, methods, techniques, sequences or procedures. It is also the architect’s responsibility to distribute the necessary submittals to their consultants for review. Should the architect review a consultant’s submittal, the architect assumes responsibility and could be held liable for damages should they occur. The architect or engineer can stamp a submittal either Reviewed, Reviewed as noted, Revise and Resubmit, or Rejected. Words such as Approved or Accepted should be avoided.
Specifying Submittals
The project specifications as prepared by the architect/engineer are where the submittals for each trade and product begin. Many of the specification sections will have a Submittals article section that will clearly define what the contractor shall provide for both review and information. There is no standard list of trades that are required to have their shop drawings reviewed. Each project is unique and therefore it is left to the professional judgment of the architectural/engineering team to define these submittal requirements. Typically, areas involving structural components, or items involving life safety, aesthesis, function, or building code compliance can be expected to have significant submittal requirements.
Product Data, Shop Drawings, Coordination Drawings, Samples for Initial selection, Samples for Verification are among the submittals required for review. Submittals for information and not requiring review include design data, certificates, test reports, inspection reports and manufacturer’s instructions.
Unspecified shop drawings or submittals submitted for review should be returned to the contractor without review. Once the A/E team reviews these submittals they assume responsibility for them, not to mention the unscheduled office resources it takes to complete the review.
Issues will Arise
Even with the best plans and contracts in place, issues will arise that will challenge the team. Actions by the team will be required to keep the project on track and on time. The following are some common pitfalls that might be expected.
- Abbreviated submittal review time by the architect
- Incomplete or no submittal schedule from the contractor
- Late submittals distributed to the team
- Contractor distributing submittals without review
- Submittals with product substitution
- Work installed prior to submittal review
Each of these issues creates greater potential for future litigation if problems with cost or time should arise.
To limit submittal review liability:
- Prepare proper contract language.
- Review of submittals and shop drawings should be consistent with the contract (i.e. shop drawing stamp should matched the contract language).
- Avoid reviewing submittals over and above what is spelled out in the contract. If problems down the road should occur, this could be seen as the architect assuming liability.
Careful and diligent review of shop drawings and other required submittals will help avoid any future shop drawing related liability. Additionally, all parties should have in place a logging system that clearly tracks all required submittals with date-in and date-out. Cutting corners in the submittal review phase can lead to costly claims. So, is the construction submittal process really that important?
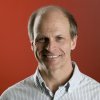
David Ingold
David Ingold is a graduate of The Ohio State University School of Architecture and a member of the Construction Specifications Institute (CSI) with Construction Documents Technology (CDT) certification. With more than 18 years of experience, David brings a broad knowledge base and understanding of design and construction to a wide variety of project types. He is an accomplished senior project administrator with experience in developing all phases of architectural documents. David has performed key responsibilities as a project leader, specifications writer, and coordinator for projects of all types and complexities including low- and high-rise condominiums, sporting facilities, higher education and government research laboratories, manufacturing facilities, wastewater treatment plants, parking garages, and campus master plans. David’s greatest aspiration is to provide construction administrative services to fully execute project designs.
Website: buildipedia.com/channels/on-site