Why Are Construction Costs on the Rise?
The answer to this question lies in economics. In a down economy, it would seem logical that the cost of materials would drop in response to a decline in projects, i.e., a lack of demand. However, global events impact construction costs in the United States, specifically the prices and availability of materials. We spoke with Ken Simonson, the chief economist for the Associated General Contractors of America (AGCA), to learn exactly what is driving construction costs and find out his predictions for the coming months.
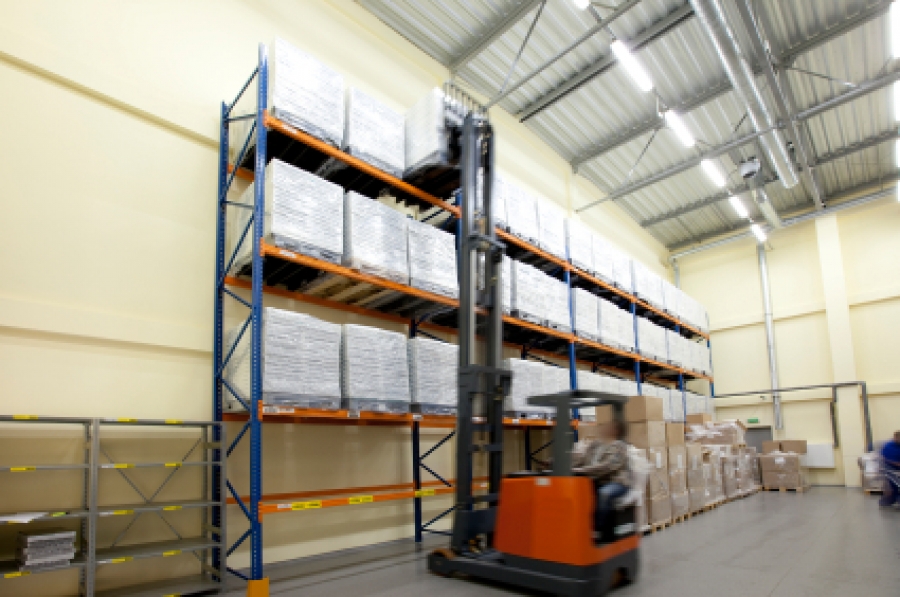
Producer Price Index
To get a feel for what is pushing up costs, take a look at the Producer Price Index, which provides an average of the cost of all materials used in every type of construction from single family homes to infrastructure, as well as the diesel fuel used by contractors. The index soared by 15% in the summer of 2008, the largest peak in costs in recent history. Diesel fuel and materials including asphalt and metals, specifically copper and steel, hit record prices. Then, of course, came the recession, and the following summer prices dropped again by a rate of 9%. Since then they have yo-yoed. From July 2010 to July 2011 the Producer Price Index saw a rise of 8.9%; the Consumer Price Index, by contrast, went up only 3.6%.
Precious Metals
Metals such as steel and copper account for some of the greatest rises in construction costs. They are globally traded, so the U.S. construction industry is competing for the same metal sources with companies that produce electronics and machinery worldwide. The production of these metals depends on the availability of ores, of which the worldwide supply is limited. Relatively few mines produce most of the world’s copper supply, so prices surge when there is a spike in demand, whether the demand is actual or perceived (traders are rumored to be stockpiling copper). Actual disruptions in the mining process, such as strikes or earthquakes, such as those that have disrupted the world’s largest copper mine in Chile, also have an effect on supply. In Africa, military and political turmoil has made production uncertain at times. Just this year, the price of copper rose to a record $4.60 per pound.
Steel is another story. Construction steel in the United States is made from melted scrap, and, although plenty of scrap is usually available, the market can swing when foreign demand rises, causing a doubling or tripling of the cost of steel. Although the costs of metals are up, the costs of other materials are remaining low and steady. The stable costs of these materials can be attributed to the facts that they are produced locally and their only application is in construction. Such materials include concrete, lumber, and gypsum wallboard. Their flat prices have kept the overall index from going up as much this year as in the past.
The Underbidding Issue
Although public projects fueled by federal stimulus money have supplied a consistent volume of work, those funds have dried up as all levels of government cut spending. Contractors are now getting hungry for work, and particularly when bidding for competitive public jobs, they have been undercutting each other with the hope that the prices of materials will fall when the time comes to build. Sometimes, they are caught on the wrong side of this bet. Surprisingly, these risky practices haven’t put many contracting companies out of business, but such failures might not be far off, explains Simonson.
What’s Next?
“I still think that we will see gradual improvement in some categories of private non-residential construction,” Ken Simonson chief economist for AGCA
Although we are not out of the woods yet, economically the last six months have seen a rise in some construction sectors. While the construction of single family homes, offices, and retail projects is still down, many companies are investing in building new factories or expanding and modernizing existing facilities. Other sectors that are experiencing growth include power construction, as well as non-drilling portions and retrofitting coal-fired power plants, and building wind, solar, and geothermal facilities. There has also been an upturn in the construction of warehouses, truck terminals, and hospitals. “I've been too much of a Pollyanna; I kept thinking things would turn up but then they didn’t,” laments Simonson. “I still think that we will see gradual improvement in some categories of private non-residential construction,” he predicts.
Sign up to receive Simonson’s regular reports on the economics behind construction costs here.
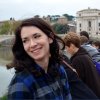
Murrye Bernard
Murrye is a freelance writer based in New York City. She holds a Bachelor's degree in Architecture from the University of Arkansas and is a LEED-accredited professional. Her work has been published in Architectural Record, Eco-Structure, and Architectural Lighting, among others. She also serves as a contributing editor for the American Institute of Architects' New York Chapter publication, eOculus.
Website: www.murrye.com