Cast-In-Place Concrete
The concrete slab-on-grade is an economical and durable structure, suitable for a variety of floors and foundations. The slabs are usually reinforced, and various types of joints are used to control cracking due to shrinkage of the concrete. The tendency to shrink also leads to curling (distortion of a slab in a curved shape), primarily at the joints and at the slab's perimeter, but good choices and practices will minimize this problem. Vapor barriers and sheets of polystyrene for insulation can be installed between the slab and the grade.
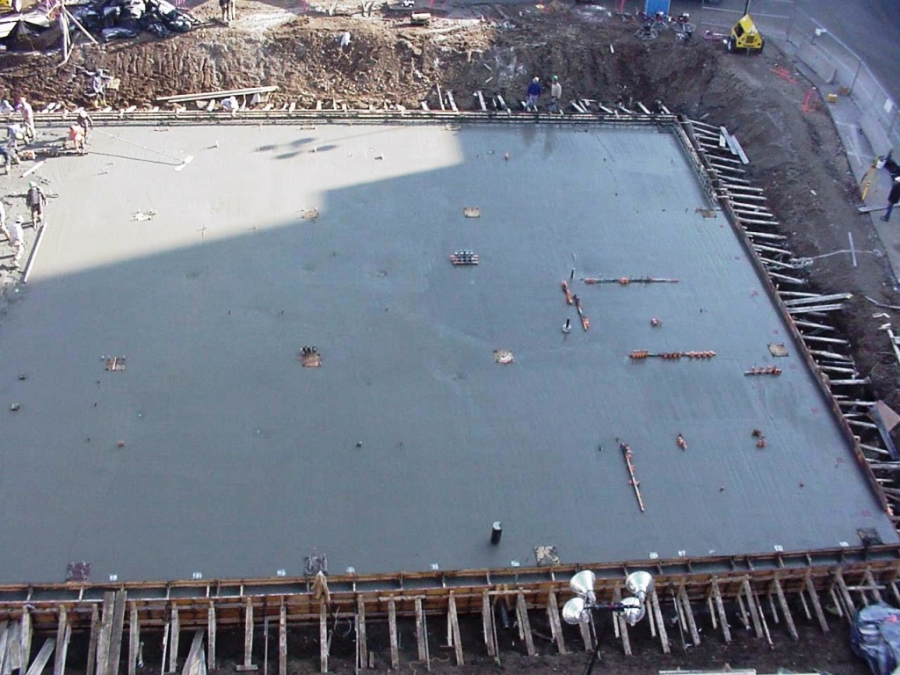
Topic Summary
A concrete slab-on-grade refers to the installation of a layer of concrete directly onto compacted or natural soil. This type of installation is widely used in the construction of foundations for single industrial, commercial, and residential buildings, as well as for driveways and patios. A disadvantage with the slab-on-grade is the lack of convenient access for utilities. Concrete slabs-on-grade are reinforced, usually with steel reinforcing bars or welded wire fabric.
The concrete mix used to construct a slab-on-grade needs to be selected carefully, with particular attention being paid to the compacting and finishing of the concrete. The slab-on-grade tends to curl at the perimeter and joints due to differential shrinkage (for example, the exposed top surface of the slab shrinks whereas the bottom and core do not). This shrinkage is usually the result of drying, but two chemical reactions which can take place in curing concrete, carbonation and desiccation, can also contribute to curling. The main factors determining the degree of curling are those that create the moisture gradient in the slab, e.g., water in the grade beneath the slab, water in the concrete, dry interiors in the buildings, wind, etc.
Traditional slabs-on-grade require joints to accommodate the construction, shrinkage, and movement of the concrete. There are typically three types of joints to consider: the control or contraction joint, the construction joint, and the isolation joint. The control joint is usually a saw cut, made soon after placement to penetrate to a depth of one quarter of the thickness of the slab. Saw cutting a minimum of one quarter of the thickness of the slab causes a "weakened plane" in the concrete, so that as internal stresses build up, the weakened area of the concrete will crack at the saw cut, relieving the stress in the concrete and controlling it to crack along the saw cut and not randomly in the slab. Construction joints are either designed stopping points or where a joint needs to be installed due to an unanticipated stopping. Isolation joints are installed in a concrete slab to relieve flexural stresses, and dowelled joints are used to accomplish this. The dowels are normally steel and can be a round, square, or flat bar, or a plate. It is important to install the dowel in a single plane with true alignment for the joint to be effective.
Environmental Considerations
As with all on-site installations, the concrete should be mixed and poured at temperatures above 40°F and the surface of the new concrete should also be maintained above a temperature of 40°F through the curing process. In the event that placement of the concrete is approved at lower temperatures, the water and aggregate should be heated to at least 50°F at the time of pouring. In hot weather, the reinforcing steel bars should be kept cool prior to installation.
Design Basics
In the design of the slab on grade as a foundation it is important to consider:
- Specified compressive strength of the concrete, typically 2000 - 2500 psi
- Capacity of the soil at the site, i.e., the soil bearing pressure
- Location, size and spacing of the reinforcing steel bars
- Thickness of the slab
The design and sizing of the reinforcing materials must comply with building codes, properly utilizing the strengths of the two materials in composite. Normally, the most economical and constructible solutions are selected. Reinforcing materials add expense to the concrete. Thus, an evaluation should be completed comparing the quantity of the rebar to the volume of concrete. However, it is unacceptable if the design results in insufficient reinforcing material or if the spacing of the reinforcing bars is too wide.
The designation of the reinforcing steel is usually tabulated in a Reinforcing Schedule on the construction drawings. (There are numerous text books available for more in-depth information regarding reinforcing steel and the placement of dowel rods.) Additionally, the concrete strength required for different uses on a construction site can also be assembled in a table. The following are examples of such a schedule:
DOWEL SIZE AND SPACING (INCHES) |
|||
SLAB DEPTH |
DOWEL DIA. |
DOWEL LENGTH |
SPACING O.C. |
5-6 |
3/4 |
16 |
12 |
7-8 |
1 |
18 |
12 |
9-10 |
1-1/4 |
18 |
12 |
CLASS | RECOMMENDED SLUMP (IN.) |
RECOMMENDED 28-DAY COMPRESSIVE STRENGTH (PSI) |
USUAL TRAFFIC | USE | SPECIALCONSIDERATIONS | CONCRETE FINISHING TECHNIQUE |
1 |
5 |
3,000 |
Light Foot |
Residential surfaces; mainly with floor coverings |
Grade for drainage; level slabs suitable for applied coverings; curing |
Single troweling |
2 |
5 |
3,500 |
Foot |
Office and churches; usually with floor covering. Decorative |
Surface tolerance (including elevated slabs); nonslip aggregate; hardener or exposed aggregate; artistic joint layout |
Single troweling; nonslip finish where required |
3 |
5 |
3,500 |
Foot with pneumatic wheel |
Exterior walks, driveways, garage floors, and sidewalks |
Grade for drainage; proper air content; curing |
Float, trowel, or broom finish |
4 |
5 |
4,000 |
Foot with light vehicular traffic |
Institutional and Commercial |
Level slab suitable for applied coverings; nonslip aggregate for specific areas and curing |
Normal steel trowel finish |
5 |
4 |
4,000 |
Industrial vehicular traffic- pneumatic wheels |
Light-duty industrial floors for manufacturing, processing, and warehousing |
Good uniform subgrade; surface tolerance; joint layout; abrasion resistance; curing |
Hard steel trowel finish |
6 |
4 |
4,500 |
Industrial vehicular traffic- hard wheels |
Industrial floors subject to heavy traffic; may be subject to impact loads |
Good uniform subgrade; surface tolerance; joint layout; load transfer; abrasion resistance; curing |
Special metallic mineral aggregate repeated hard steel troweling |
7 |
4 |
Base 3,500 |
Industrial vehicular traffic- hard wheels |
Bonded two-coarse floors subject to heavy traffic and impact |
Base slab - Good uniform subgrade; reinforcement; joint layout; level surface; curing. Topping composed of well-graded all metallic aggregate applied to high strength plain topping to toughen; surface tolerance; curing |
Clean-textured surface suitable for subsequent bonded topping. Special power floats with repeated steel trowelings |
8 |
4 |
Topping 5,000 - 8,000 |
As in classes 4, 5, and 6 |
Unbonded toppings - Freezer floors on insulation, on old floors, or where construction schedule dictates |
Bond breaker on old surfaces; mesh reinforcement; minimum thickness 3" (nominal 75mm) abrasion resistance; curing |
Hard steel trowel finish |
9 |
5 |
4,000 or higher |
Super flat or critical surface tolerance required. Special materials handling vehicals or robotics requiring special tolerances |
Narrow-aisle, high-bay warehouses; television studios |
Varying concrete quality requirements. Shake-on hardeners cannot be used unless special applications and great care is employed. Proper joint arrangement |
Strictly follow finishing techniques as indicated in section 7.15 of ACI 302 |
Preparation
The soil onto which the concrete slab is to be placed should be compact and well drained. The formwork and the accessories for both the forming operations and for the placing, compacting, finishing, and curing of the concrete should be on-site. Reinforcing steel bars should also be on-site and stored in a clean, dry place prior to installation. Any specified vapor barrier and insulation materials must be available at the time of installation of the slab.
For cast-in-place structures the choice of reinforcing materials will be stated in the construction drawings, together with details of the installation and the accessories required. Any rebar, steel tendons, welded wire fabric, galvanized or epoxy-coated rebar, and wire fabric should be clearly labeled and stored in a clean, dry area.
Applications and Installations
It is recommended that the concrete be placed at the rate at which it can be spread, struck off, consolidated and bull-floated. It should be placed as close to its final position as possible, working from one end of the slab formwork. The slab can be finished in various ways, depending on the application, e.g., driveways and patios may require a patterned finish or a color.
The reinforcing material is placed on support chairs to ensure its position and the splices or laps fitted in accordance with the drawings, Building Code, and ACI 318.
Fiber-reinforced concrete is mixed, poured, finished, and cured following the procedures used with regular concrete.
Other Considerations
The use of vapor barriers under slabs-on-grade minimizes the transport of water vapor from the sub-layer. The barriers are typically sheets of low-density polyethylene of a thickness approximately 10 mils. The vapor barrier can be important if the floor is to be covered with carpet, tile, or wood, or if equipment that is sensitive to moisture will be placed in the space. The plastic sheet is placed onto the grade and the formwork for the slab is then installed.
Sheets of polystyrene can be similarly placed under the slab to provide insulation.
Joint-free slabs have recently been introduced, in which a plastic grid induces a network of fine cracks throughout the concrete element. Since it cannot be eliminated, the idea is to dissipate the effects of the drying and associated shrinkage as uniformly as possible, producing cracks that do not adversely affect the surface of the slab.
Combining reinforcement methods can maximize the benefits of the reinforcement within the concrete. The use of admixtures can benefit both the workability and curing time for cast-in place concrete
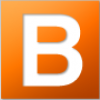
Buildipedia Staff
The Buildipedia research and writing staff consists of dozens of experienced professionals from many sectors of the industry, including architects, designers, contractors, and engineers.
Website: buildipedia.com/